Understanding Resin-Bonded Sand Casting
Resin-bonded sand casting is a modern technique in the foundry industry that has gained significant popularity due to its numerous advantages over traditional sand casting methods. This innovative process employs a mixture of sand and resin to create molds for casting metal parts, offering better accuracy, surface finish, and versatility. In this article, we will explore the principles of resin-bonded sand casting, its benefits, applications, and considerations for its use.
At the core of resin-bonded sand casting is the combination of fine sand and a thermosetting resin binder. This mixture is prepared using various methods, often involving the addition of a hardening agent or catalyst to initiate the curing process. The sand mixture is then shaped into a mold using either a manual or automated process. Once the mold is formed, heat is applied to cure the resin, hardening the mold and making it ready for the pouring of molten metal.
Understanding Resin-Bonded Sand Casting
Additionally, resin-bonded sand casting exhibits excellent dimensional accuracy. The molds created using resin-bonded sand are stable and maintain their shape even at high temperatures, ensuring that the final castings meet the required specifications. This accuracy not only enhances product quality but also minimizes waste, as fewer defective parts are produced.
resin bonded sand casting
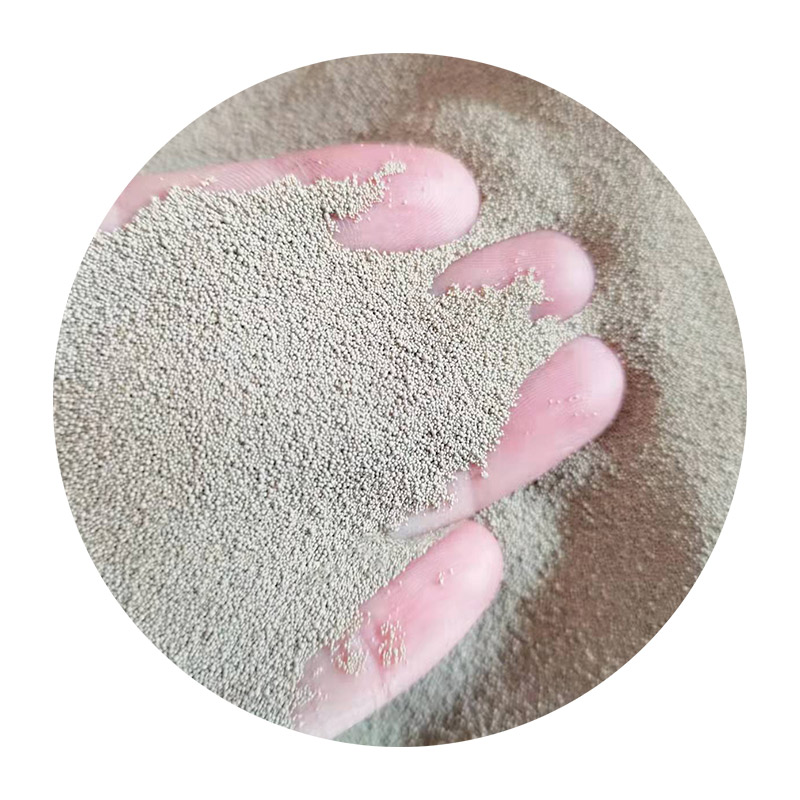
Another noteworthy benefit of this casting method is its ability to handle a wide range of materials. Whether it is aluminum, steel, or other alloys, resin-bonded sand casting can accommodate various metals, making it a versatile option for manufacturers. This versatility extends to the production of both small and large components, enabling businesses to adapt to diverse market demands.
While resin-bonded sand casting presents numerous benefits, it is essential to consider some challenges associated with the process. The preparation of resin-bonded sand requires careful control of the mixing and curing conditions to ensure optimal performance. Improper ratios or inadequate curing can lead to defective molds, which may compromise the quality of the final casting.
Furthermore, the use of chemical binders introduces environmental considerations. Although many manufacturers are adopting eco-friendly resins, it is crucial to implement proper safety and ventilation measures in foundries. Managing the environmental impact while ensuring worker safety remains a critical aspect of resin-bonded sand casting operations.
In terms of applications, resin-bonded sand casting is widely used in various industries that demand high-quality castings. The aerospace industry utilizes this technique for producing components subject to strict regulatory standards, while automotive manufacturers benefit from its efficiency in producing engine blocks, transmission cases, and intricate parts. Furthermore, the process is increasingly being explored in art and sculpture, where artists create unique designs using resin-bonded sand molds.
In conclusion, resin-bonded sand casting is a valuable technique in modern manufacturing, offering superior quality, accuracy, and versatility compared to traditional casting methods. As industries continue to evolve and require higher-performance components, the role of resin-bonded sand casting is likely to expand, making it an essential consideration for companies seeking innovative solutions in the foundry sector. While challenges exist, the benefits of this casting method justify its growing prominence in various applications, from industrial parts to artistic creations.
Post time:دسامبر . 17, 2024 01:52
Next:why is sand casting used