Precision Sand Casting A Key Process in Modern Manufacturing
Precision sand casting is a highly regarded manufacturing process that combines traditional techniques with modern innovations to produce intricate metal components. This method involves creating complex shapes by pouring molten metal into a sand mold, which solidifies to create the final product. As industries continue to evolve, the demand for precision and accuracy in casting has propelled this technique to the forefront of manufacturing.
The Basics of Sand Casting
At its core, sand casting is a process that uses sand as the molding material. The first step involves creating a pattern of the desired component, which is often made from metal or plastic. This pattern is then placed in a sand mixture, which is compacted to form a mold. High-quality sand, often bonded with clay or resin, is used to ensure better dimensional accuracy and surface finish.
Once the mold is ready, molten metal is poured into it. The choice of metal varies depending on the application, ranging from aluminum and iron to magnesium and brass. After the metal cools and solidifies, the sand mold is broken away, revealing the finished part. This process allows for excellent dimensional tolerance and surface finish, which is critical for various engineering applications.
Advantages of Precision Sand Casting
One of the primary advantages of precision sand casting is its versatility. This process can accommodate a wide range of materials and complex geometries, making it suitable for industries such as automotive, aerospace, and construction. The ability to produce intricate designs that may be challenging or impossible to achieve through other manufacturing methods is a significant benefit.
Additionally, precision sand casting is cost-effective for both low and high production runs. With the use of advanced technologies such as 3D printing for pattern making, manufacturers can significantly reduce lead times and production costs. This flexibility allows businesses to respond quickly to changing market demands without sacrificing quality.
Another notable advantage is the superior surface finish obtained through precision sand casting
. Traditional sand casting methods often resulted in rough surfaces, necessitating additional machining. However, advancements in materials and techniques have enabled the production of smoother surfaces, reducing the need for post-processing and further enhancing the overall efficiency of the manufacturing process.precision sand casting
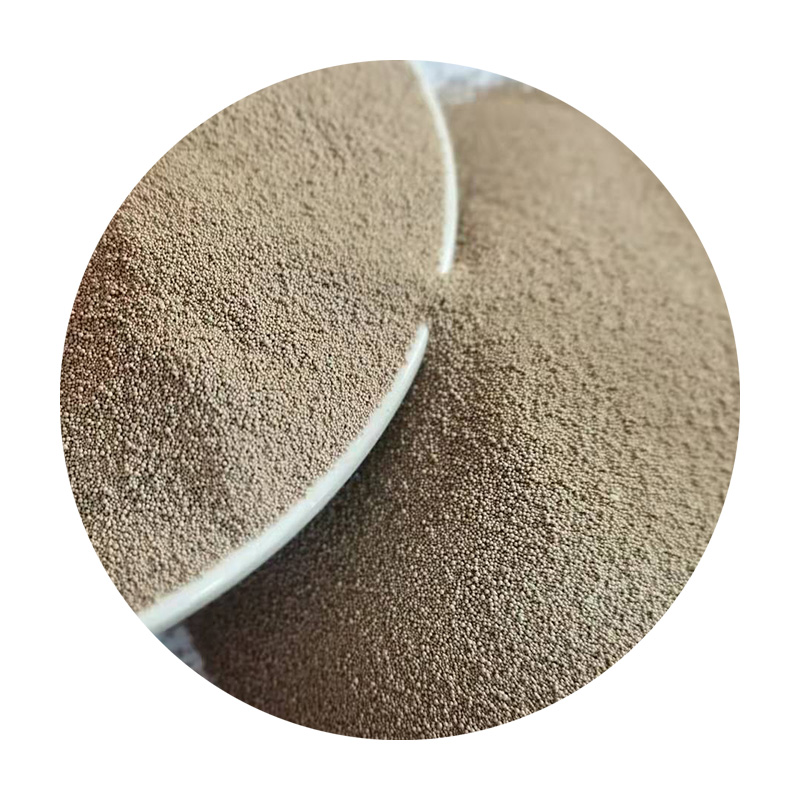
Applications in Various Industries
Precision sand casting finds applications in numerous industries due to its ability to produce high-quality components. In the automotive sector, for instance, it is used to manufacture engine blocks, transmission housings, and various structural components. The aerospace industry benefits from sand casting by producing lightweight yet strong parts that meet strict regulatory requirements.
Moreover, the construction industry employs precision sand casting for creating essential elements such as brackets, fittings, and decorative pieces. These components not only need to meet functional performance criteria but also aesthetic considerations, where precision casting plays a crucial role.
Challenges and Innovations
Despite its many advantages, precision sand casting is not without its challenges. Issues such as sand core integrity, defects in the final product, and the environmental impact of sand disposal are areas that require constant attention. However, ongoing research and innovation in materials, process control, and sustainability practices are paving the way for improvements in the casting industry.
In recent years, the integration of digital technologies into sand casting processes has transformed traditional methods. The use of computer-aided design (CAD) and simulation software allows manufacturers to predict potential defects and optimize the design before production. Furthermore, advancements in materials science have led to the development of more sustainable sand materials, reducing the environmental footprint of casting operations.
Conclusion
Precision sand casting stands as a vital process in modern manufacturing, combining age-old techniques with cutting-edge innovation to produce high-quality, intricate components. With its applications spanning across various industries, the process continues to evolve, addressing challenges, and meeting the increasing demands for precision and sustainability in manufacturing. As technology continues to advance, we can expect precision sand casting to play an even more significant role in shaping the future of industrial production.
Post time:نوامبر . 27, 2024 20:32
Next:Exploring the Benefits and Techniques of Dry Sand Casting in Metal Fabrication