Lost Foam Sand Casting An Innovative Approach to Metal Casting
Lost foam sand casting is an innovative manufacturing process that combines the benefits of traditional sand casting with the efficiency and precision of foam pattern technology. This method has gained significant attention in the metalworking industry due to its ability to produce complex shapes and intricate designs while reducing material waste and labor costs.
The process begins with the creation of a foam pattern that replicates the desired part. This is typically made from expanded polystyrene (EPS), which is lightweight and can be easily molded into various shapes. The foam pattern is coated with a thin layer of a special ceramic material to provide a strong barrier against molten metal. This coating is crucial, as it ensures that the foam does not react with the metal and helps to create a smooth surface finish.
Once the foam pattern is prepared, it is placed in a mold made of sand. The sand is typically mixed with a binder to enhance its strength and stability during the casting process. The foam pattern is then surrounded by the sand mixture, which is compacted to form a rigid mold. After the sand has set, the next step is to introduce molten metal into the mold.
As the molten metal is poured into the mold, the heat causes the foam pattern to vaporize, leaving a cavity that precisely mirrors the shape of the original pattern. This process allows for the creation of complex geometries that would be challenging to achieve using traditional metal casting methods. Additionally, the vaporization of the foam minimizes the risk of defects and ensures clean castings.
lost foam sand casting
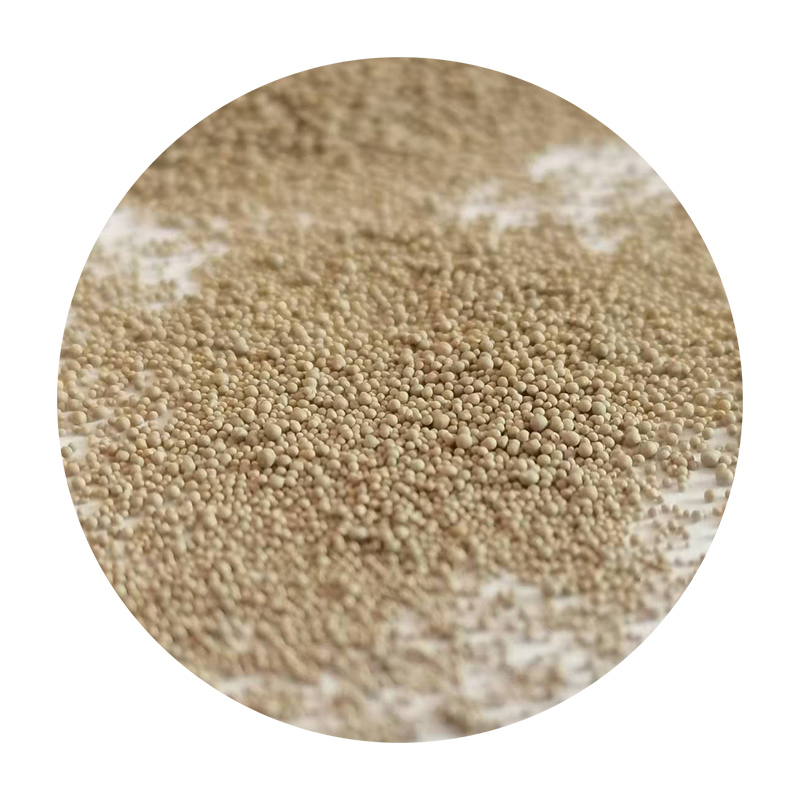
One of the key advantages of lost foam sand casting is its ability to produce highly accurate and dimensionally stable components. This is particularly beneficial in industries such as automotive and aerospace, where precision is paramount. The reduction in machining time and cost is another significant benefit, as many castings can be produced with little to no further processing required.
Furthermore, lost foam sand casting is an environmentally friendly option. The process generates less scrap material compared to traditional casting methods, and the foam patterns are often made from recyclable materials. This aligns with the growing demand for sustainable manufacturing practices and reduces the overall environmental impact of the casting process.
In addition to its environmental benefits, lost foam sand casting offers flexibility in terms of material options. It can be used with a variety of metals, including aluminum, iron, and bronze, making it suitable for diverse applications across different industries. This versatility allows manufacturers to tailor their processes to meet specific requirements, enhancing competitiveness in the market.
Despite its numerous advantages, lost foam sand casting does have some limitations. The initial setup cost can be higher than conventional sand casting, and the process may not be suitable for very large or heavy castings. Additionally, the equipment used for lost foam casting requires careful handling and maintenance to ensure optimal performance.
In conclusion, lost foam sand casting represents a significant advancement in metal casting technology, offering numerous benefits such as improved accuracy, reduced waste, and enhanced design capabilities. As industries continue to seek innovative and sustainable manufacturing solutions, the adoption of lost foam sand casting is likely to increase, paving the way for a new era of efficient metal production. With its unique combination of traditional techniques and modern technology, lost foam sand casting stands out as a compelling choice for manufacturers seeking to optimize their casting processes.
Post time:سپتامبر . 22, 2024 05:16
Next:ceramic sand price