Lost Foam Sand Casting An Innovative Approach to Metal Casting
Lost Foam Sand Casting is an advanced metal casting process that has garnered increasing attention in various manufacturing sectors. This highly efficient technique combines the simplicity of traditional sand casting with the precision of foam modeling, offering numerous advantages for producing complex shapes and reducing material waste. This article explores the principles, advantages, applications, and future perspectives of lost foam sand casting.
Principles of Lost Foam Sand Casting
The lost foam sand casting process revolves around the use of a foam pattern, usually made of expanded polystyrene (EPS), which is vaporized during the casting process. The steps involved include
1. Pattern Creation A foam pattern of the desired shape is fabricated. This pattern serves as a temporary mold that will eventually be replaced by molten metal.
2. Coating The foam pattern is coated with a thin layer of sandmixed with a binder. This coating serves to create a shell that will hold the shape when the foam is vaporized.
3. Molding The coated pattern is placed in a flask, and dry sand is packed around it, providing support while allowing gas to escape during the casting process.
4. Vaporization When molten metal is poured into the mold, it heats the foam pattern, causing it to vaporize almost instantaneously. This creates a cavity in the mold that precisely replicates the original shape of the foam pattern.
5. Casting The molten metal fills the void left by the vaporized foam, solidifying into the final cast part once it cools.
This process eliminates the need for core and parting lines, which are often problematic in traditional casting methods. The result is a high-quality finish and greater dimensional accuracy.
Advantages of Lost Foam Sand Casting
lost foam sand casting
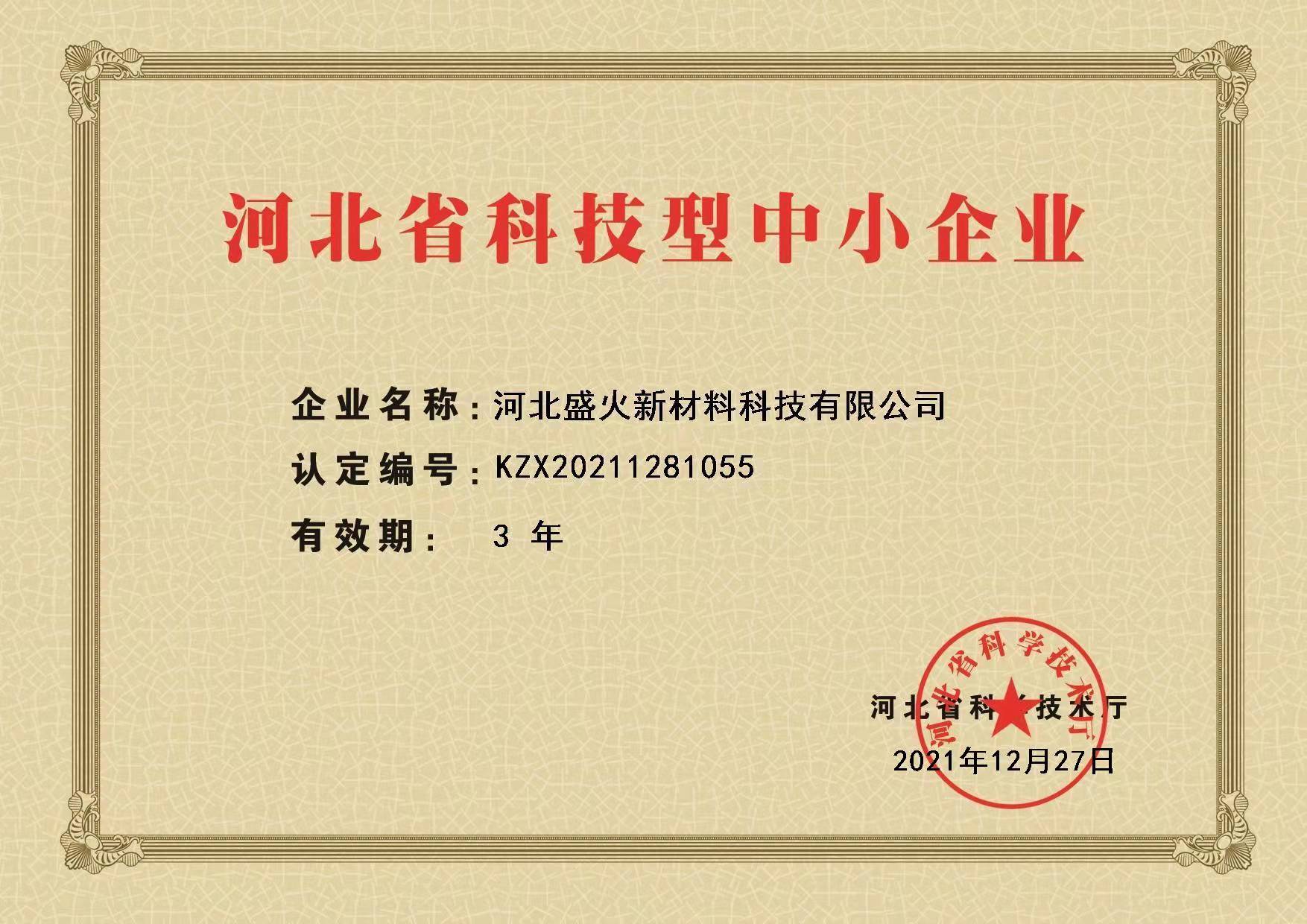
The lost foam process offers several compelling benefits
1. Complex Shapes The ability to create intricate designs is one of the hallmark advantages of lost foam sand casting. The foam patterns can be easily shaped to accommodate complex geometries that would be challenging with other casting methods.
2. Material Efficiency As the foam vaporizes without leaving residue, the process minimizes material waste. Additionally, the elimination of cores and parting lines reduces the amount of metal required.
3. Improved Surface Finish Parts produced with lost foam sand casting often exhibit superior surface finishes compared to those from traditional casting methods. This can reduce or eliminate the need for extensive machining after casting.
4. Reduced Lead Times The simplicity of creating foam patterns allows for faster prototyping and reduced lead times in manufacturing. This expedited process can significantly benefit sectors that require quick turnaround times.
5. Versatility Lost foam sand casting can be utilized across a wide range of metals, including aluminum, magnesium, and iron, making it a versatile option for various applications.
Applications
Lost foam sand casting has found a niche in diverse industries, including automotive, aerospace, and art. In automotive manufacturing, for instance, complex engine components can be produced with higher efficiency and lower costs. Aerospace components require high precision and lightweight characteristics, both of which are achievable through this casting method. The art sector also benefits from lost foam casting, enabling artists to create detailed sculptures and designs with ease.
Future Perspectives
As manufacturing continues to evolve, lost foam sand casting stands to benefit from advancements in technology. Innovations in foam materials, improved binders, and automated processes can enhance the efficiency and scalability of this casting method. Furthermore, as sustainability becomes a focal point for industries, the eco-friendly aspects of lost foam sand casting, including reduced waste and energy consumption, position it favorably for future adoption.
In conclusion, lost foam sand casting is an innovative and efficient method that combines the benefits of traditional sand casting with the precision of foam patterns. With its ability to create complex shapes, reduce material waste, and improve surface finish, this technique is set to play a significant role in the future of manufacturing across various sectors. As industries continue to seek out more sustainable and efficient production methods, lost foam sand casting is poised for growth and continued relevance in the metal casting landscape.
Post time:نوامبر . 08, 2024 06:54
Next:Exploring Materials for Effective Lost Foam Casting Techniques and Applications