Iron Sand Casting An Ancient Art with Modern Applications
Iron sand casting is a fascinating process that has its roots deeply embedded in ancient metallurgy, yet it remains relevant in today’s industrial landscape. This traditional technique involves the use of iron-rich sand to produce intricate metal parts, showcasing both skill and artistry. With advancements in technology and materials, iron sand casting has evolved, becoming more efficient and versatile while retaining its traditional charm.
Iron sand, composed primarily of magnetite, is abundant in various regions around the world, making it a sustainable resource for metalworking. The sand is first collected and prepared, often purified to eliminate impurities before use. The casting process begins with the creation of a mold, which can be crafted from various materials, including metal or sand itself. The choice of mold significantly influences the final product's surface finish and detail.
Once the mold is ready, molten iron is poured into it. This is where the magic happens—the hot liquid metal fills the mold cavity, taking on its shape as it cools and solidifies. The cooling process is critical; it affects the metallurgical properties of the final casting, determining its strength, durability, and ductility. Once solidified, the mold is broken away to reveal the cast part, which may require additional finishing processes such as grinding or polishing to meet specific standards.
iron sand casting
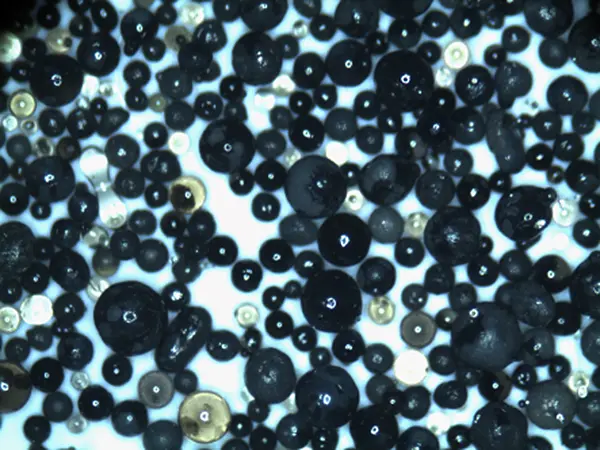
One of the standout features of iron sand casting is its capability to produce complex shapes and designs that would be difficult or impossible to achieve with other manufacturing methods. This flexibility allows for the creation of intricate components used in various industries, including automotive, aerospace, art, and construction. Furthermore, the ability to recycle the sand makes this method environmentally friendly, aligning with modern sustainability goals.
In recent years, technological advancements have enhanced the iron sand casting process. Techniques such as 3D printing are now being integrated to create molds with precision, resulting in reduced lead times and improved accuracy. Additionally, computer simulations are frequently used to predict fluid dynamics and cooling patterns, helping to minimize defects and optimize the casting process.
Despite the rise of modern manufacturing technologies, iron sand casting remains a cherished method among artisans and engineers alike. Its rich history, combined with contemporary innovations, positions iron sand casting as an essential technique in both traditional and modern manufacturing spheres. As industries continue to seek sustainable and efficient production methods, the future of iron sand casting appears bright, proving that ancient practices can coexist and thrive in a high-tech world.
Post time:نوامبر . 20, 2024 05:07
Next:types of sand casting process