Understanding Foundry Sand Specifications
Foundry sand plays a crucial role in the casting process, providing a medium for shaping molten metal into various forms. Its specifications are essential in determining the quality of the final product. In this article, we will explore the key aspects of foundry sand specifications, including its composition, properties, and testing methods.
Composition of Foundry Sand
Foundry sand is primarily composed of silica (SiO2), making up about 85-95% of its content. The most commonly used type of foundry sand is called green sand, which is a mixture of silica sand, clay, water, and additives. Clay serves as a bonding agent, ensuring the sand retains its shape during the mold-making process.
The quality of foundry sand is significantly impacted by its grain size and distribution. The ideal sand grains should be round and uniform in size, allowing for easy compaction and minimal gaps. Grain size is typically measured in mesh; common sizes for foundry applications range from 50 to 70 mesh, providing an optimal balance between strength and permeability.
Key Properties of Foundry Sand
Several key properties define the effectiveness of foundry sand
1. Permeability This property refers to the ability of sand to allow gases to escape during the casting process. High permeability is essential to prevent gas entrapment, which can lead to defects in the casting. The permeability of foundry sand is often measured using a permeameter.
foundry sand specifications
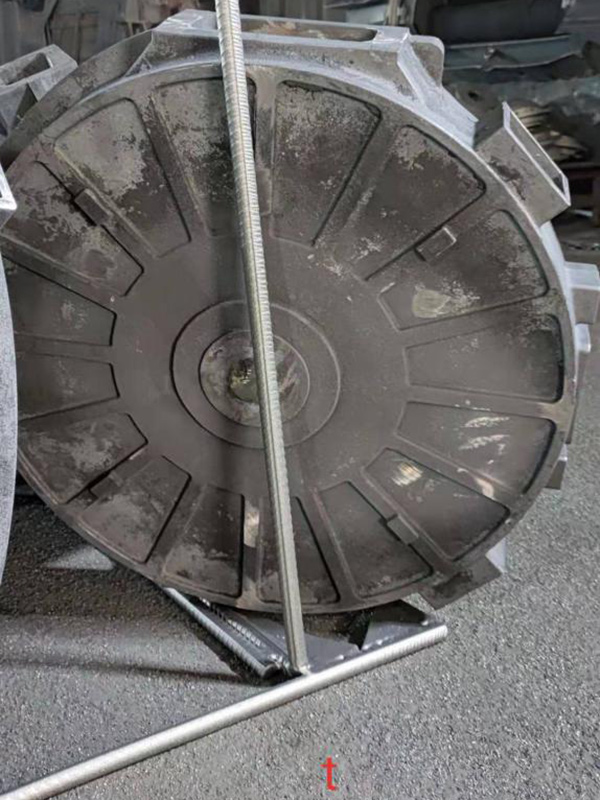
2. Strength The mechanical strength of the sand is vital for maintaining mold integrity during metal pouring. This includes both compressive and tensile strength metrics. A strong mold ensures accurate reproduction of the desired shapes and minimizes defects.
3. Refractoriness Foundry sand must withstand high temperatures without breaking down or losing its structural integrity. The refractoriness of the sand is gauged by its melting point and thermal stability, which ensures it can endure the heat generated during metal casting.
4. Moisture Content The moisture content of foundry sand must be carefully controlled. Too much moisture can lead to gas bubbles and mold collapse, while too little can reduce the effectiveness of the binding clays. Generally, a moisture content ranging from 2% to 5% is optimal for green sand.
Testing Methods
Several standardized tests are conducted to ensure that foundry sand meets the required specifications. Common testing methods include
- Grain Size Analysis Using sieves to determine the particle size distribution. - Permeability Testing Assessing the airflow through the sand and its ability to vent gases. - Compressibility Testing Examining how sand compacts under pressure, revealing its strength characteristics. - Moisture Content Testing Utilizing methods such as a moisture balance to determine the sand’s water content accurately.
Conclusion
In summary, foundry sand specifications are fundamental to the success of the casting process. By understanding the composition, properties, and testing methods, foundry engineers can select the appropriate sand for their specific applications. Maintaining stringent quality standards not only ensures high-quality casting outcomes but also enhances the efficiency and reliability of the foundry operations. As industries evolve and new materials emerge, staying updated on sand specifications will remain essential for success in metal casting.
Post time:اکتبر . 13, 2024 07:53
Next:foundry sand reuse