The Composition and Importance of Foundry Sand
Foundry sand, especially silica sand, plays a pivotal role in the casting industry, serving as a critical component in the production of metal castings. Its unique properties have made it the material of choice for foundries worldwide, where it is utilized for mold making and core production. Understanding the composition of foundry sand is essential to grasp its effectiveness in foundry applications and the nuances of its interaction with various metals.
Composition of Foundry Sand
Foundry sand primarily consists of silica (SiO2), which can vary in purity and grain size depending on the source and intended application. However, the ideal foundry sand must contain a high percentage of silica, typically around 90-95%, due to its excellent thermal properties and chemical stability. In addition to silica, foundry sand may contain various other minerals and impurities, such as alumina (Al2O3), iron oxide (Fe2O3), and moisture, which can influence its performance and suitability for specific casting processes.
The grain size and shape of foundry sand are also critical factors. Ideally, foundry sand should possess a uniform grain size, which aids in creating precise and detailed mold cavities. The shape of silica grains can range from angular to rounded, with rounded sands typically providing better flow characteristics and packing density, leading to superior mold strength. Moreover, the angular grains can enhance surface roughness, which is sometimes desirable for specific casting applications.
Types of Foundry Sand
There are several types of foundry sand, with each showing variations in composition to suit different casting methods
. The most common types include1. Green Sand This is a mixture of silica sand, clay, water, and other additives. Green sand is widely used due to its ability to maintain moisture and its relatively low cost. The clay content serves to bind the sand grains together, producing strong and durable molds.
2. Dry Sand As the name suggests, dry sand does not contain moisture. It relies on a binder system for cohesion. This type is often used in applications where high-temperature stability is required, as it can withstand higher heat than green sand.
foundry sand composition
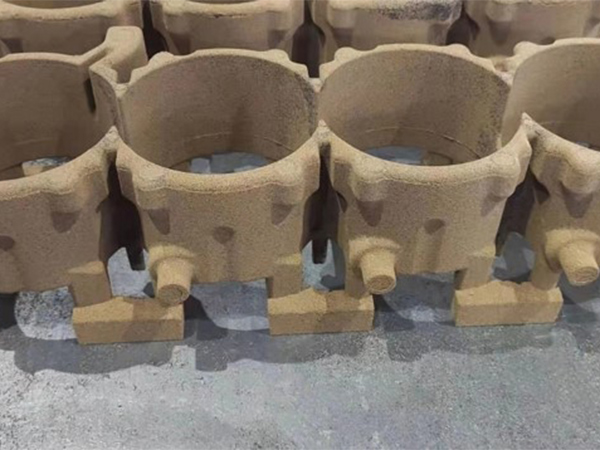
3. Chemical Bonded Sand This type utilizes chemical binders, such as phenolic resins, to bind the sand grains together. This method allows for greater control over mold strength and is particularly useful for complex shapes and larger castings.
4. No-Bake Sand Similar to chemically bonded sand, no-bake sand uses a catalyst system that allows the sand to bond at room temperature. This type of sand is known for its versatility and strength.
The Role of Foundry Sand in Casting
The composition of foundry sand directly influences the casting quality and properties of the finished product. The right sand ensures that molds are strong enough to hold molten metal without deforming or collapsing, which is vital for dimensional accuracy and surface finish. A well-chosen foundry sand can enhance the casting’s mechanical properties, as its composition affects the cooling rates and heat transfer during the solidification of the metal.
Additionally, foundry sand plays a significant role in reducing defects in castings. For instance, proper sand composition can minimize issues like sand inclusion, which occurs when sand particles become embedded in the casting, leading to surface imperfections. The thermal conductivity of foundry sand also helps to control the cooling rates, thereby influencing the structure and properties of the cast metal.
Environmental Aspects and Sustainability
With rising environmental concerns, the foundry industry has adapted by exploring ways to recycle and repurpose used foundry sand. Spent foundry sand is often disposed of in landfills; however, it can be beneficially reused in various applications, such as construction, road building, and as a component in concrete manufacturing. This not only mitigates environmental impact but also offers cost savings for foundries aiming to adopt more sustainable practices.
Conclusion
In summary, the composition of foundry sand is paramount in determining the quality and success of metal casting processes. The balance of silica content, grain size, and type of binder used influences everything from mold strength to casting defects. As the industry continues to evolve, understanding the intricacies of foundry sand enables manufacturers to optimize their processes, ensuring high-quality cast products while addressing environmental sustainability. The future of foundry sand rests on innovative approaches that balance performance with ecological responsibility.
Post time:دسامبر . 11, 2024 07:42
Next:different types of sand casting