Components of Sand Casting An Overview
Sand casting, also known as sand mold casting, is a widely used metal casting process that involves creating a mold from a sand mixture and then pouring molten metal into that mold to form solid components. This method is favored due to its cost-effectiveness, versatility, and ability to produce complex shapes. Understanding the components of sand casting is essential for grasping how this process works.
One of the main components of sand casting is the mold. A sand mold is typically made up of a mixture of sand, a binding agent, and water. The most common sand used is silica sand because of its high melting point and availability. The binding agent, often clay or a resin, helps to hold the sand particles together, creating a stable mold structure. The quality of the mold is crucial, as it must withstand the pressure of the poured metal, prevent deformation, and maintain the desired shape of the final product.
Another important component is the pattern. The pattern is a replica of the final desired product and is used to create the mold cavity. Patterns can be made from various materials, including wood, metal, or plastic, and are often designed with allowances for shrinkage and machining. There are different types of patterns, such as solid patterns, split patterns, and cope and drag patterns, each serving specific applications based on the complexity of the design.
The core is another significant element in sand casting, particularly when producing hollow sections. Cores are typically made of sand and can be placed within the mold to create internal passages or cavities in the final cast object. They are essential when the design of the component requires intricate internal features, ensuring that the molten metal does not fill every space of the mold, but instead forms the intended hollow shapes.
components of sand casting
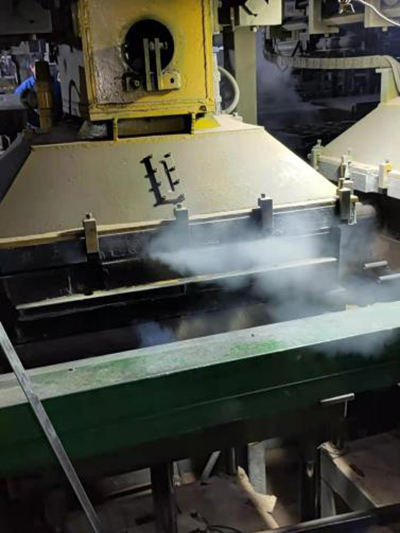
The process of sand casting also requires the use of molten metal, which is a critical component. This can be aluminum, iron, steel, bronze, or other metals, which are heated until they reach a liquid state. The choice of metal is dictated by the desired properties of the final product, such as strength, weight, and corrosion resistance. Once the metal is molten, it is poured into the mold cavity, where it cools and solidifies to take on the shape of the mold.
After the metal has cooled sufficiently, a process known as shakeout occurs, where the sand mold is broken away from the cast piece. This step requires care to prevent any damage to the product. Subsequently, the casting is subjected to finishing processes such as trimming, grinding, or machining to remove any excess material or imperfections and achieve the desired surface finish.
Lastly, sand casting is often accompanied by several auxiliary components, including gating systems and filters. Gating systems are channels that guide the molten metal into the mold cavity, while filters may be incorporated to remove impurities from the metal during pouring, ensuring a cleaner final casting.
In conclusion, the components of sand casting—including the mold, pattern, core, molten metal, and auxiliary systems—work in unison to produce high-quality metal parts. This time-tested method continues to play a vital role in various industries, from automotive to aerospace, due to its reliability and adaptability for producing complex geometries at scale. Understanding these components offers valuable insights into the intricacies of the sand casting process, allowing for improvements in design and execution in future projects.
Post time:دسامبر . 04, 2024 19:50
Next:Exploring the Benefits and Applications of Coated Sand in Modern Construction