Advantages of Sand Casting Process
Sand casting, a traditional and widely-used manufacturing process, has been a cornerstone of the foundry industry for centuries. This technique involves creating a mold from a pattern, often made of metal or wood, and using sand as the primary molding material. The advantages of sand casting are numerous, making it a popular choice for producing metal parts in various industries. Below, we delve into some of the key benefits of this versatile process.
1. Cost-Effectiveness
One of the most significant advantages of sand casting is its cost-effectiveness. The materials required, particularly sand, are inexpensive and widely available. This accessibility makes sand casting an ideal option for small to medium-sized production runs and prototyping, where high setup costs can be a barrier with other casting processes. Additionally, the process requires minimal investment in specialized equipment, further reducing overall costs.
2. Design Flexibility
Sand casting provides excellent design flexibility, allowing for the creation of complex shapes and large components that would be challenging to manufacture using other methods. The molds can be easily modified to accommodate changes in design, making sand casting suitable for custom parts and prototypes. This adaptability is particularly beneficial for industries such as automotive and aerospace, where intricate designs and specifications are commonplace.
3. Large Size Capacity
Another notable advantage is the capability of sand casting to produce large parts. The process can accommodate sizable patterns and molds, enabling manufacturers to create components that may be difficult or impossible to produce with other casting methods. This feature is especially relevant in sectors like construction and heavy machinery, where large castings are often required.
advantages of sand casting process
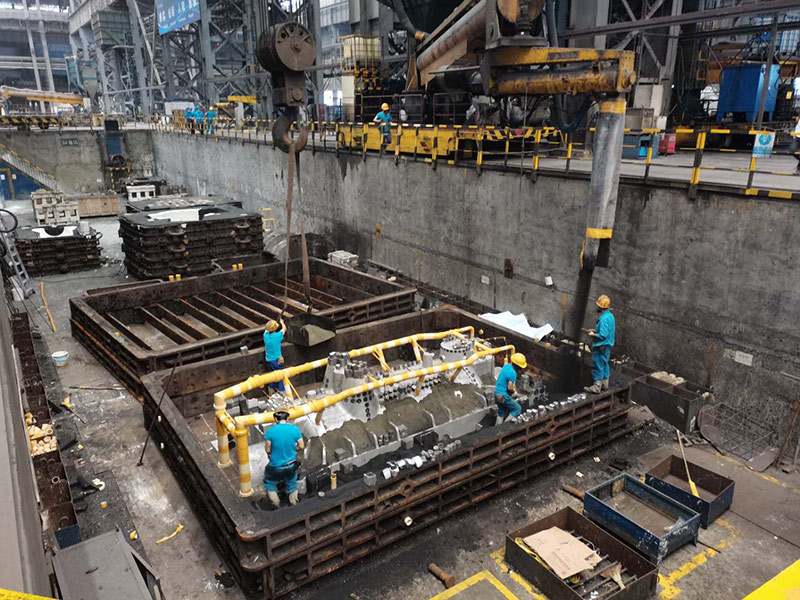
While other casting processes may yield finer surface finishes, sand casting can produce components with a satisfactory surface quality that meets industry standards. Various techniques can be employed to improve the surface finish further, such as using finer sand grains or adding coatings to the molds. As a result, sand casting remains popular in the production of both functional parts and aesthetic components.
5. Versatility in Materials
Sand casting is compatible with a wide range of materials, including ferrous and non-ferrous metals. This versatility allows manufacturers to select the most appropriate material for their specific application, whether it's aluminum, bronze, or iron. The ability to use various alloys enhances the performance characteristics of the final product, enabling manufacturers to tailor properties such as strength, weight, and corrosion resistance.
6. Low Waste Generation
The sand casting process typically generates less waste compared to other manufacturing processes. The sand used in molds can often be recycled and reused multiple times, contributing to efficient resource utilization. Moreover, the design of sand casting processes minimizes excess material, making it an environmentally friendly choice in terms of waste generation.
7. Short Lead Times
Sand casting can often be completed in a relatively short time frame, particularly for small production runs or prototypes. The simplicity of the process, combined with the quick turnaround from pattern creation to the final cast, allows manufacturers to respond swiftly to market demands and changes. This advantage is crucial in fast-paced industries where time-to-market is a key competitiveness factor.
Conclusion
In summary, sand casting is a highly advantageous manufacturing process that offers cost-effectiveness, design flexibility, and the ability to produce large components with a variety of materials. Its versatility and low waste generation, alongside the capacity for rapid production, make it an enduring choice for manufacturers across multiple industries. As technology evolves, sand casting continues to adapt, reinforcing its position as a vital method in the manufacturing landscape. Whether for prototypes or large-scale production, the benefits of sand casting ensure its relevance in today's manufacturing processes.
Post time:دسامبر . 10, 2024 21:45
Next:Guide to Super Sand Bond G2 for Optimal Outdoor Surfaces