Materials Used for Sand Casting
Sand casting, a widely used manufacturing process, involves creating a mold from sand to form metal parts. This method is favored for its versatility, cost-effectiveness, and ability to produce complex shapes. Understanding the various materials utilized in sand casting is essential for optimizing the quality and performance of the final products. The main materials employed in sand casting include mold sand, binders, additives, and metals.
1. Mold Sand
The primary material in sand casting is mold sand, which consists mainly of silica particles. Silica sand, due to its high melting point, is the most common choice as it withstands the temperatures associated with molten metal. The grain size and shape of the sand influence the mold's strength and porosity. There are different types of mold sand, such as green sand, dried sand, and sodium silicate sand.
Green Sand is a mixture of silica sand, clay, and water. It contains about 2-10% clay, which enhances the binding properties and gives the mold its strength. This type of sand is reusable, making it an economical choice for many foundries.
Dried Sand, as the name suggests, is sand that has been dried to remove moisture. This type is often used for applications that require higher dimensional accuracy and surface finish.
Resin-bonded Sand utilizes synthetic resins as binders instead of clay
. This method allows for a more precise mold, enabling the production of intricate features and finer details in the castings.2. Binders
what materials are used for sand casting
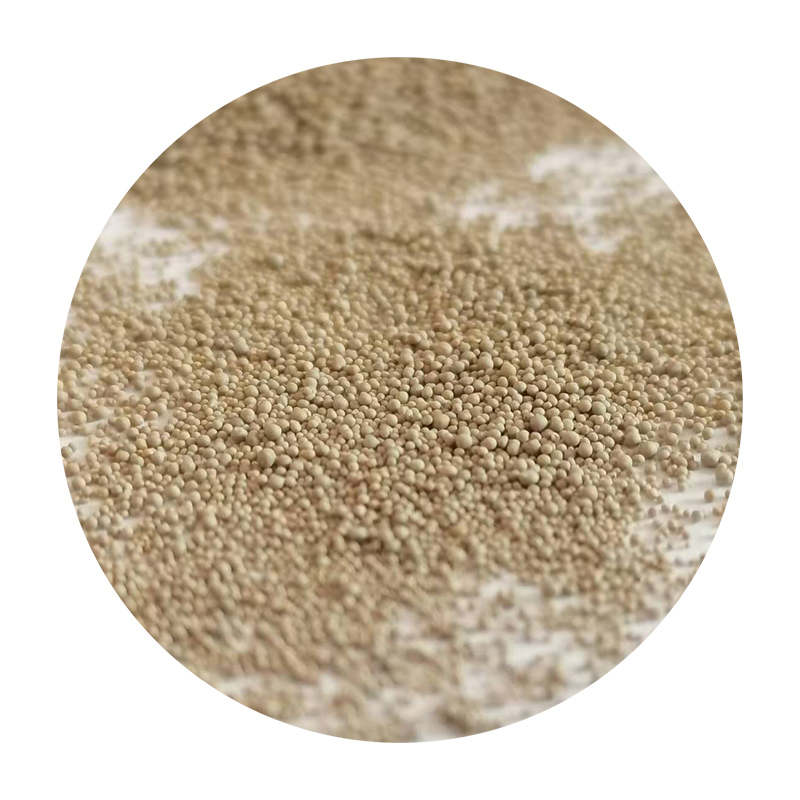
Binders are materials added to sand to enhance its ability to maintain shape and resist deformation during metal pouring. In addition to clay, which is the traditional binder used in green sand, resin systems are popular in modern setups due to their superior strength. Epoxy and phenolic resins are commonly used as they improve the thermal stability and reduce the gas emissions during casting. The selection of the binder significantly affects the mold's performance and the quality of the final casting.
3. Additives
Additives play an essential role in sand casting. They are introduced to improve specific properties of the sand mold, such as permeability, strength, and reduce the likelihood of defects. Some common additives include
- Coal Dust Used to reduce sticking between the mold and the metal, thus aiding in easier cleanup and preventing mold damage during removal. - Surfactants These additives help in achieving better moisture distribution within the mold material. - Other Fillers Materials such as clay particles or fine sand can be added to improve the overall strength and surface finish of the casting mold.
4. Metals
Once the mold is prepared, metal is poured into it to create the final product. Various metals can be employed in sand casting, each with unique properties and applications. Commonly used metals include
- Aluminum Known for its lightweight and good corrosion resistance, aluminum is frequently used for automotive and aerospace components. - Iron Cast iron is popular due to its excellent casting characteristics and wear resistance. It is widely used in industrial and machinery applications. - Steel As a versatile metal, steel is used in applications where high strength is required, such as in machinery parts and tools.
In conclusion, the materials used in sand casting—mold sand, binders, additives, and metals—play a critical role in determining the efficacy and quality of the casting process. The selections made in each category can greatly influence the performance, durability, and cost-effectiveness of the final product. Understanding these materials allows manufacturers to enhance their processes and achieve superior casting outcomes.
Post time:Urr . 19, 2024 16:30
Next:золотий пісок