Materials Used for Sand Casting
Sand casting, one of the oldest and most versatile metal forming techniques, involves creating a mold from a mixture of sand and other materials. This process is widely utilized in manufacturing various components, ranging from small items to large industrial parts. Understanding the materials that comprise the sand casting process is essential for optimizing both quality and efficiency.
1. Base Material Sand
The primary material used in sand casting is sand itself. There are several types of sand that can be employed, but the most commonly used is silica sand due to its abundance and suitable properties. Silica sand consists of fine grains of quartz, which can withstand high temperatures without melting. Moreover, the spherical shape of the grains allows for excellent flow characteristics and compaction.
Another type is chromite sand, which is more resistant to high temperatures and is often used in applications requiring better thermal properties. Additionally, zircon sand is known for its low thermal expansion and high melting point, making it suitable for high-precision casting.
2. Binders
To create a mold, sand must be mixed with a binder to ensure the grains stick together. The most common binder used in sand casting is clay, specifically bentonite clay. Bentonite enhances the plasticity of the sand mixture, allowing it to retain its shape during the pouring of molten metal.
Resin binders are another option, particularly in modern foundries that utilize “no-bake” or “cold box” processes. These chemically activated resins provide strength and allow for detailed and intricate mold designs. They cure at room temperature, making the process faster and more efficient compared to traditional clay-based binders.
3. Additives
what materials are used for sand casting
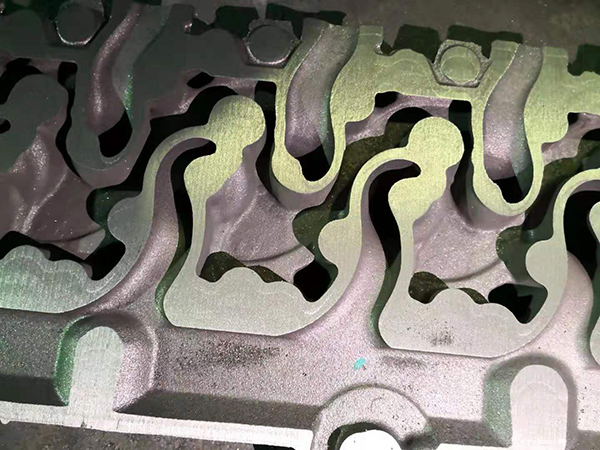
Various additives can be incorporated into the sand mixture to improve its properties. For example, coal dust is often added to enhance the thermal stability of the sand mold. This helps in preventing the mold from cracking when subjected to the high temperatures of molten metal.
Other additives, such as graphite, can be used to improve surface finish and reduce defects in the final casting. Additionally, various oils can be added to the mixture to improve flowability and reduce clumping during handling.
4. Metal Alloys
The choice of metal to be cast is crucial and varies depending on the requirements of the final product. Common alloys used in sand casting include
- Aluminum Lightweight and resistant to corrosion, aluminum alloys are widely used in automotive and aerospace applications. - Iron Both cast iron and ductile iron are popular for their excellent castability and mechanical properties. - Steel Carbon and alloy steels are chosen for their strength and durability, frequently applied in heavy machinery and structural components. - Bronze and Brass These copper alloys are employed for their aesthetic appeal and corrosion resistance, often found in decorative items and marine applications.
5. Core Materials
For more complex designs that require internal cavities, cores made of sand or other materials are used. Core sands are often mixed with resins or other binders to allow for a stable shape during pouring. Common core materials include oil sand, furan sand, and shell sand, each chosen based on specific casting requirements.
Conclusion
The materials used in sand casting are diverse, each playing a significant role in the overall performance and quality of the final product. From the fundamental silica sand to various alloy choices, the selection of materials can influence the molding process, detail retention, and surface finish of cast components. With advancements in technology and material science, the sand casting process continues to evolve, offering improved solutions for modern manufacturing challenges. Understanding these materials allows manufacturers to optimize and innovate within this time-honored method of metalworking.
Post time:Urr . 14, 2024 16:24
Next:advantages and disadvantages of sand casting process