Understanding Sand Casting Suppliers A Key to Quality Manufacturing
In the realm of manufacturing, sand casting remains one of the most widely used techniques for producing metal parts. This method involves creating a mold from sand, into which molten metal is poured to form intricate shapes and components. The efficacy of the sand casting process relies heavily on the quality of its suppliers. Selecting the right sand casting suppliers can significantly influence the overall quality of the final product, lead times, and production costs.
The Role of Sand Casting Suppliers
Sand casting suppliers play a crucial role in the supply chain by providing not only the raw materials needed for the casting process but also the expertise and innovation required to optimize production. These suppliers source high-quality sand, binders, and additives, ensuring that the molds produced are durable and capable of withstanding the high temperatures of molten metal. Additionally, many suppliers offer a range of services, including molding, finishing, and even machining, which can streamline the manufacturing process for their clients.
Evaluating Potential Suppliers
When looking for sand casting suppliers, several factors need to be considered to ensure they meet your specific requirements. First, assess the supplier's material quality. The type of sand used can significantly impact the final product's surface finish and dimensional accuracy. Suppliers experienced in handling various types of sand, from silica to zircon, are often better equipped to meet diverse project needs.
Secondly, consider the supplier's experience and reputation in the industry. Established suppliers with a proven track record are more likely to understand the complexities of different casting projects, anticipate potential challenges, and provide valuable guidance throughout the production process. In addition, customer reviews, testimonials, and case studies can shed light on a supplier's reliability and work ethic.
sand casting suppliers
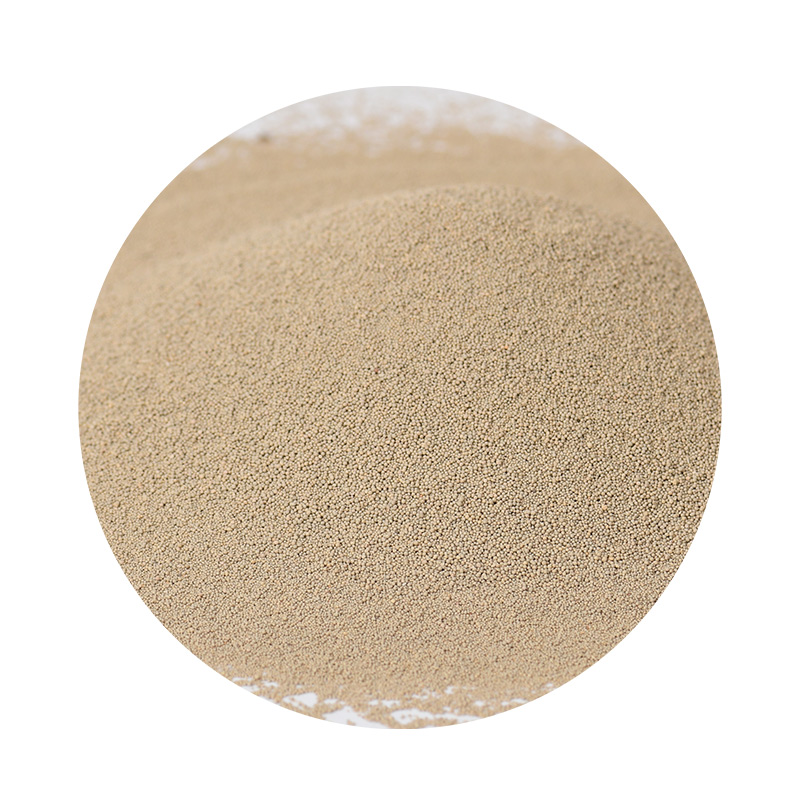
Innovation and Technology
Another essential aspect to consider is the level of innovation and technology that a supplier brings to the table. Many leading sand casting suppliers have adopted advanced manufacturing technologies, such as computer-aided design (CAD) and 3D printing, to enhance the accuracy and efficiency of their molds. By working with suppliers that embrace these technologies, manufacturers can benefit from reduced lead times and increased production flexibility.
Sustainability Practices
In today’s environmentally-conscious landscape, it is also vital to consider the sustainability practices of sand casting suppliers. Many manufacturers are increasingly prioritizing eco-friendly processes, such as recycling sand and utilizing sustainable materials. Partnering with suppliers committed to sustainability not only helps reduce the environmental impact of production but also aligns your business with modern consumer preferences.
Conclusion
Choosing the right sand casting suppliers is a critical decision for any manufacturer involved in producing metal components. By focusing on material quality, supplier reputation, innovation, and sustainability, businesses can enhance their manufacturing processes and ensure high-quality outcomes. Investing time in evaluating potential suppliers can lead to a productive partnership that supports your operational goals and drives long-term success in the competitive manufacturing landscape. Ultimately, the right collaboration with sand casting suppliers is instrumental in achieving excellence in metal casting productions.
Post time:Urr . 11, 2024 12:52
Next:lost foam casting applications