Parts of Sand Casting A Comprehensive Overview
Sand casting, also known as sand mold casting, is one of the most widely used manufacturing processes in the metalworking industry. This method dates back thousands of years and is integral in producing a variety of components across different sectors, including automotive, aerospace, and heavy machinery. Understanding the parts involved in sand casting is essential for anyone looking to grasp the fundamentals of this technique.
At its core, sand casting involves several key components that work together to produce a metal part through the solidification of molten metal in a sand mold
. Let's break down these components.1. Pattern The pattern is a replica of the final part to be cast. It is typically made from materials such as wood, metal, or plastic. The pattern serves as a template to create the mold cavity and must be slightly larger than the final product to accommodate for shrinkage and to allow for easy removal from the sand. Patterns can be classified into different types, including solid patterns for simple shapes, split patterns for complex geometries, and cope and drag patterns that can be separated into two parts.
2. Mold The mold is created by compacting sand around the pattern. The sand used in sand casting is usually mixed with a binding agent, such as clay, to enhance its strength and cohesiveness. The two main parts of the mold are the cope (the upper part) and the drag (the lower part). Once the pattern is removed, the mold retains the shape necessary to create the desired component. The mold can have various features, such as sprues and risers, which are crucial for controlling the flow of molten metal and ensuring proper filling of the cavity.
parts of sand casting
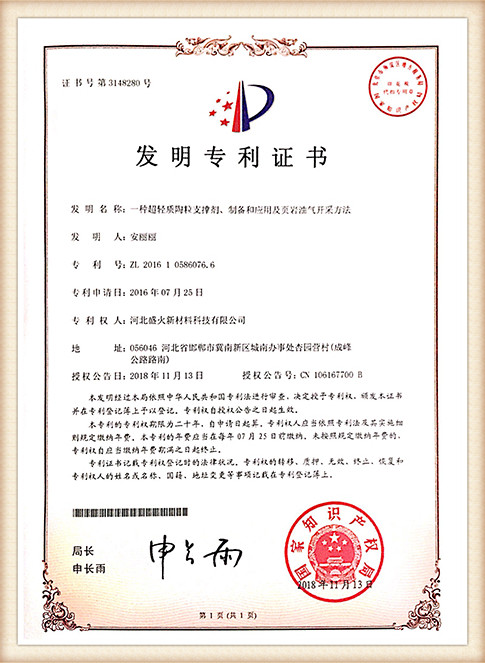
3. Core In cases where internal cavities are required, cores made of sand are inserted into the mold before pouring the metal. Cores define the internal shapes of the casting and are essential for complex designs. They are usually held in place by pins or other securing methods and can have varying compositions, including sand-based materials.
4. Melting Furnace To produce castings, the metal must be melted and poured into the mold. Different types of furnaces can be used, depending on the metal being cast. For example, induction furnaces, cupola furnaces, and electric arc furnaces are common choices. The melting furnace must maintain a consistent temperature to ensure the metal is completely molten and can flow smoothly into the mold.
5. Pouring Equipment Once the metal reaches the desired temperature, it is transferred to pouring equipment. This includes ladles, pouring cups, and spouts. The pouring process must be carefully controlled to minimize turbulence, which can introduce defects into the casting.
6. Finishing Tools After the metal solidifies, the casting is removed from the mold and often requires additional processes to achieve the final desired dimensions and surface finish. This can include grinding, machining, and surface treatment to eliminate imperfections and enhance the part's performance.
In conclusion, the parts of sand casting play a crucial role in determining the quality and accuracy of the final product. Understanding these components is vital for optimizing the sand casting process and ensuring successful outcomes in metal fabrication. As technology advances, innovations in each of these areas are continuously improving the efficiency and effectiveness of sand casting, making it a staple in modern manufacturing.
Post time:Urr . 13, 2024 02:13
Next:resin coated sand price