Materials Used for Sand Casting
Sand casting is a widely utilized process for shaping metal into desired forms through the use of sand molds. This method is favored for its versatility, accessibility, and the ability to produce complex shapes with relative ease. Understanding the various materials involved in sand casting is essential for both professionals in the field and those interested in the fundamentals of metalworking.
1. Sand
The primary material used in sand casting is sand itself. Specifically, foundry sand is employed for this purpose, which is typically composed of silica (SiO2). The suitability of sand for casting comes from its excellent properties it can retain heat, is relatively inexpensive, and can be reused multiple times.
Foundry sand is categorized into two main types green sand and resin-bonded sand. Green sand, which consists of silica sand mixed with a small amount of clay and water, is the most commonly used type. Its moisture content allows it to hold together, forming a mold that can withstand the pressure of molten metal. On the other hand, resin-bonded sand uses resin as a binding agent. This type of sand can produce finer details and is more adaptable to intricate designs.
2. Metal Alloys
The choice of metal alloy is critical in sand casting, affecting the mechanical properties and performance of the final cast product. Common metal alloys used in sand casting include aluminum, cast iron, bronze, and magnesium alloys.
- Aluminum Alloys Lightweight and with excellent corrosion resistance, aluminum alloys are widely used in automotive and aerospace applications. They provide good fluidity, enabling complex shapes to be cast effectively. - Cast Iron Known for its excellent castability and wear resistance, cast iron is often employed in the production of engine blocks, pipes, and machinery parts. It can be easily melted and poured into molds, making it a staple in the sand casting process.
- Bronze Alloys Featuring good strength and corrosion resistance, bronze alloys are typically used in artistic sculptures, marine components, and fittings.
- Magnesium Alloys These alloys are recognized for their high strength-to-weight ratio and are often used in aerospace and automotive applications where reducing weight is paramount
.3. Bindings and Additives
materials used for sand casting
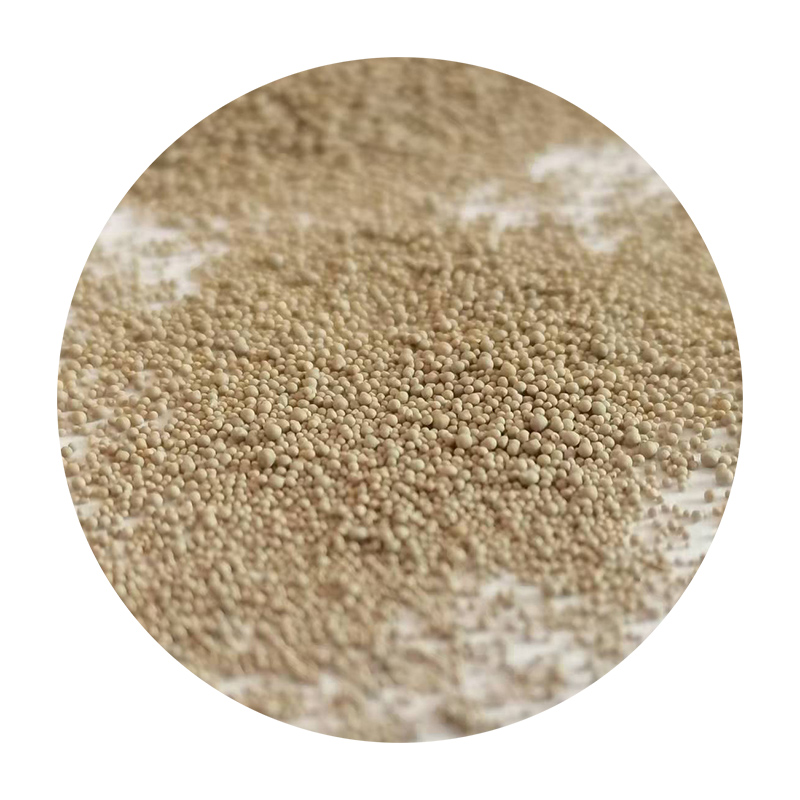
In addition to sand and metals, various binding agents and additives influence the casting process and the properties of the final product.
- Clay Clay is frequently used in green sand molding to improve its cohesiveness. The most commonly used clay is bentonite, which can absorb moisture and help hold the sand particles together. - Resins In resin-bonded sand molds, thermosetting resins such as phenolic or furan resins are utilized. These resins provide superior strength and can create intricate shapes while maintaining dimensional accuracy.
- Additives To improve specific properties of the sand casting mixture, various additives may be included. For example, fire-resistant additives can improve the mold’s ability to withstand high temperatures, while agents that enhance fluidity can help in creating smoother mold surfaces.
4. Core Materials
Cores are used in sand casting to create internal features and hollow sections within the final casting. The materials used for cores range from sand mixtures to chemical binders.
- Core Sands Similar to molding sands, core sands often incorporate additional binders for strength. These sands are designed to break down easily after casting, allowing for easy removal from the final product. - Shell Cores Shell core processes use a resin-coated sand that forms a hard shell when heated, lending additional strength and detail to the internal features of the casting.
5. Coatings
Coatings are often applied to the inner surfaces of molds to assist in the release of the casting and to enhance the smoothness of the final surface. They also help to reduce oxidation of the metal during pouring. Common coating materials include graphite and ceramic-based systems.
Conclusion
The materials used in sand casting significantly influence the quality, characteristics, and applications of the final cast products. Understanding these materials and their interactions allows for optimized production processes and improved mechanical properties in the final components. As the field of materials science continues to advance, innovations in sand casting materials will likely lead to even greater capabilities within the industry.
Post time:Aza . 28, 2024 05:35
Next:Innovative Materials for Lost Foam Casting Techniques and Applications