Understanding Foundry Sand Its Significance and Applications
Foundry sand is a crucial material in the metal casting industry, serving as a fundamental component in the creation of molds and cores for various metal products. This specialized type of sand is known for its unique properties and characteristics that make it suitable for high-performance applications in foundries. In this article, we'll delve into the significance of foundry sand, its composition, and its applications, as well as the environmental implications of its use.
Composition and Properties of Foundry Sand
Foundry sand, primarily composed of silica (SiO2), possesses several key properties that make it ideal for casting. The most commonly used type is green sand, a mixture of sand, clay, and moisture. The clay serves as a binder, helping the grains of sand stick together and form a stable mold. The moisture content keeps the sand pliable during the molding process.
One of the most important characteristics of foundry sand is its ability to withstand high temperatures without breaking down. This thermal stability is critical as the molten metal is poured into the molds, requiring a material that can handle the heat without losing shape or integrity. Additionally, foundry sand has excellent permeability, allowing gases released during the casting process to escape. This prevents defects in the final cast product, ensuring a high level of quality.
Applications of Foundry Sand
The primary application of foundry sand is in the casting industry, particularly in the production of engine blocks, frames, and other intricate parts for automobiles, machinery, and various metal products. The versatility of foundry sand makes it suitable for different casting methods, including
1. Sand Casting This traditional method utilizes molds made from foundry sand. The process is suitable for large-scale production and is commonly used for components that require detailed features and complex geometries.
making foundry sand
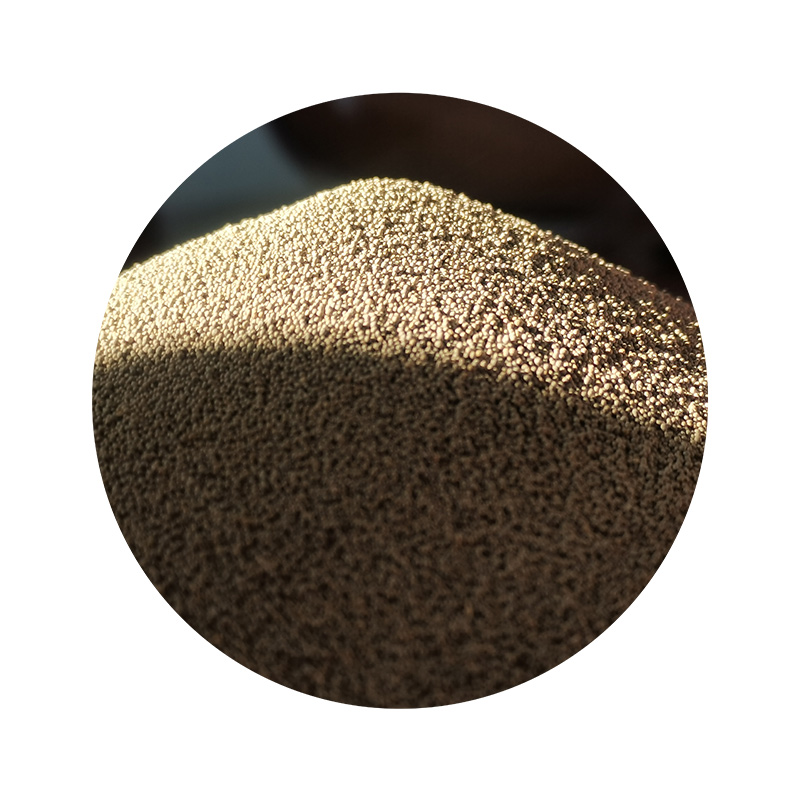
2. Investment Casting In this method, foundry sand is used to create the mold for investment casting, known for producing items with high dimensional accuracy and superior surface finish.
3. Shell Casting Foundry sand is used to form a thin shell around a pattern, which is then filled with molten metal. This process provides better dimensional accuracy and surface quality compared to traditional sand casting.
4. Core Making Foundry sand is also used to manufacture cores, which create internal cavities in castings. Cores are essential for producing complex shapes and hollow sections in metal parts.
Environmental Considerations
The use of foundry sand comes with environmental considerations that must be addressed. Traditional foundry processes often generate waste, and the disposal of used foundry sand poses a significant environmental challenge. To combat this issue, various recycling and reuse strategies have been developed. Many foundries now implement processes to reclaim and reuse spent sand, reducing waste and minimizing the need for new raw materials.
Additionally, researchers and industry professionals are exploring the potential of using foundry sand in construction and other applications, such as road base material and cement production. By finding alternative uses for spent foundry sand, the industry can reduce its environmental footprint while generating economic benefits.
Conclusion
Foundry sand plays an indispensable role in the metal casting industry, providing the necessary properties for producing high-quality components. Its unique characteristics, such as thermal stability and permeability, make it a preferred material for a variety of casting methods. As the industry continues to evolve, the focus on sustainable practices and the recycling of foundry sand will be critical in addressing environmental challenges and ensuring the long-term viability of this essential material. By embracing innovative solutions and responsible practices, the foundry industry can pave the way for a more sustainable future while continuing to meet the demands of modern manufacturing.
Post time:Urr . 13, 2024 12:48
Next:what is resin coated sand