Low Pressure Sand Casting An Overview
Low pressure sand casting is an advanced manufacturing process widely used in the metal forming industry. This technique combines traditional sand casting with low-pressure gas methods, providing several advantages in terms of product quality, performance, and cost-effectiveness. This article explores the principles, benefits, applications, and considerations of low pressure sand casting.
Principles of Low Pressure Sand Casting
The low pressure sand casting process involves creating a mold made of sand and then filling it with molten metal. Unlike traditional sand casting methods, where gravity is used to draw the molten metal into the mold, low pressure sand casting utilizes a controlled low-pressure environment (generally below 1 bar) to push the molten metal into the mold cavity. This process typically starts with the creation of a pattern (the model of the final object) which is embedded in a sand mixture to form the mold.
A key feature of this technique is the use of a pressure vessel where the molten metal is stored. Once the mold is prepared and heated to a specific temperature, the pressure is applied to the molten metal, ensuring that it enters the mold evenly and fills all the intricate details of the cavity. This results in a more uniform distribution of the metal and reduces the likelihood of defects such as porosity or incomplete fill.
Benefits of Low Pressure Sand Casting
1. Improved Casting Quality One of the primary advantages of low pressure sand casting is the ability to produce a higher quality product. The controlled pressure helps maintain consistent metal flow, resulting in smoother finishes and improved dimensional accuracy. This method reduces the occurrence of defects such as gas pockets and cold shuts.
2. Material Efficiency Low pressure sand casting can optimize material usage. The process enables the casting of intricate designs with thinner walls while still maintaining structural integrity. This not only conserves material but also makes the casting lighter.
3. Cost-Effectiveness The method can be more economical, especially for medium to large production runs. The reduced need for extensive machining post-casting and the higher yield of quality outputs lower overall production costs.
4. Versatility Low pressure sand casting can accommodate a wide range of metals, including aluminum, magnesium, and zinc alloys. This versatility allows manufacturers to choose the most suitable material for their applications, improving overall product performance.
low pressure sand casting
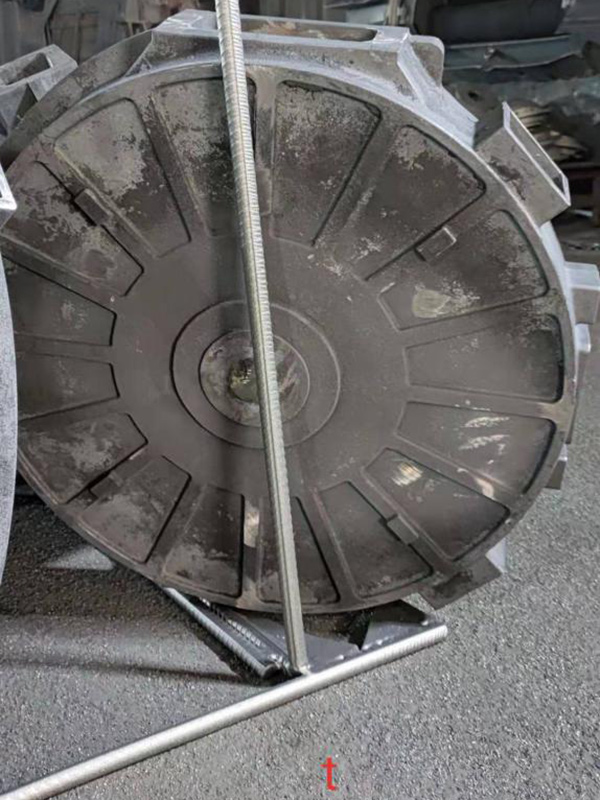
5. Environmentally Friendly The low-pressure process can lead to less waste compared to traditional sand casting methods. Moreover, advancements in sand recycling technologies are enhancing the sustainability of the casting materials used.
Applications of Low Pressure Sand Casting
Low pressure sand casting is employed in various industries, including automotive, aerospace, electronics, and heavy machinery. Its ability to produce complex shapes and components makes it particularly valuable for creating critical parts such as engine blocks, transmission casings, and intricate housings for electronic devices.
In the automotive sector, the lightweight nature of low pressure sand cast components contributes to fuel efficiency and emissions reduction. In aerospace, the durability and precision offered by this method can withstand the rigorous demands of flight. As industries continue to innovate, the applications for low pressure sand casting are likely to expand, driven by a need for more efficient and high-performance materials.
Considerations in Low Pressure Sand Casting
While low pressure sand casting offers numerous benefits, there are some considerations to keep in mind. The initial setup cost, including the design of molds and patterns, can be high. Additionally, the complexity of the process requires skilled operators and stringent quality control measures to ensure optimal results.
Moreover, not all designs may be suitable for low pressure sand casting; intricate geometries or excessively large parts may still benefit more from traditional casting techniques. Therefore, careful analysis and planning are essential before committing to this production method.
Conclusion
Low pressure sand casting represents a significant advancement in manufacturing techniques, merging traditional methods with modern technology to produce high-quality castings. Its numerous advantages, including improved casting quality, material efficiency, and cost-effectiveness, make it an attractive option for various industries. As technology continues to evolve, low pressure sand casting is poised to play a vital role in the future of metal manufacturing, providing innovative solutions to meet the needs of an increasingly demanding market.
Post time:Abe . 13, 2024 07:49
Next:Understanding the Process of Foundry Sand Casting for Effective Metal Production