Low Pressure Sand Casting A Comprehensive Overview
Low pressure sand casting is an innovative metal casting technique that combines the advantages of traditional sand casting with the benefits of low pressure injection. This method is particularly suited for creating high-quality castings made from non-ferrous metals, such as aluminum and magnesium. In recent years, low pressure sand casting has gained popularity due to its efficiency, precision, and cost-effectiveness.
At the heart of low pressure sand casting is the use of a sand mold, which is formed by compacting sand around a pattern. This mold is created in two halves, allowing for the intricate details of the design to be captured. Once the mold is prepared, it is heated to a specific temperature to enhance its strength and reduce the likelihood of defects. The low pressure aspect comes into play during the pouring of molten metal into the mold, where a controlled pressure is applied, allowing the metal to flow uniformly and fill all areas of the mold cavity.
One of the key advantages of low pressure sand casting is its ability to produce components with excellent mechanical properties. The controlled pouring process minimizes turbulence and prevents the introduction of air pockets, ensuring a dense and uniform metal structure. This results in castings with improved strength and reduced likelihood of casting defects such as porosity or inclusions.
Moreover, the low pressure method allows manufacturers to produce complex geometries with intricate details that might be challenging to achieve with traditional casting methods. This is particularly beneficial in industries requiring high precision, such as automotive and aerospace, where lightweight and robust components are crucial. Additionally, the process is adaptable to various production volumes, making it suitable for both small-scale custom jobs and large-scale manufacturing.
low pressure sand casting
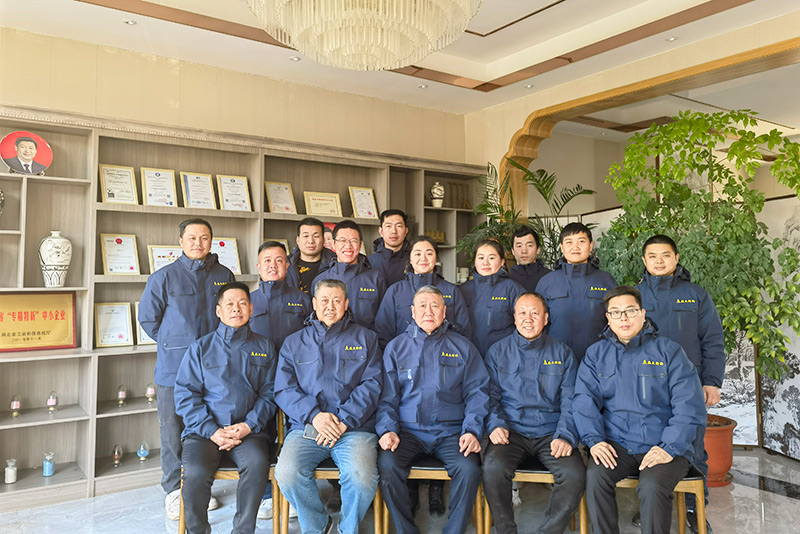
Environmentally, low pressure sand casting offers advantages over other casting methods. The process produces less waste, as the sand can be reused multiple times, thereby reducing material costs and minimizing environmental impact. The low pressure system also results in lower energy consumption compared to high-pressure casting methods, contributing to a more sustainable manufacturing process.
However, like any manufacturing technique, low pressure sand casting has its challenges. The initial setup costs for creating molds can be relatively high, which may discourage smaller operations. Additionally, while this method excels in producing non-ferrous metal castings, it may not be as effective for ferrous metals, limiting its application scope.
Despite these challenges, the benefits of low pressure sand casting make it an attractive option for many industries. As technology advances, the precision and effectiveness of low pressure sand casting continue to improve, solidifying its place as a vital method in modern metal manufacturing. Ultimately, low pressure sand casting is poised to play a significant role in meeting the growing demands for high-quality, lightweight parts across various verticals, representing a blend of traditional techniques and modern innovations.
In conclusion, low pressure sand casting is a remarkable technique that offers efficiency, precision, and sustainability. As industries evolve and seek better solutions for their manufacturing needs, this method stands out for its ability to produce complex and high-quality components, making it an essential player in the future of metal casting.
Post time:Aza . 24, 2024 13:22
Next:Exploring Various Uses of Sand Casting in Modern Manufacturing Techniques