Lost Foam Metal Casting An Innovative Approach to Metal Fabrication
Lost foam metal casting is an advanced manufacturing process that has gained traction in the metalworking industry due to its unparalleled precision and efficiency. This technique, which involves the use of polystyrene foam patterns, offers several advantages over traditional casting methods. It combines the benefits of traditional sand casting with the capabilities of modern technology, providing manufacturers with an innovative solution for producing complex metal parts.
Understanding the Process
The lost foam casting process begins with the production of a foam pattern that closely resembles the final product. This pattern is typically made from polystyrene foam, a lightweight and easily molded material. The foam pattern is then coated with a thin layer of sand and a binder, creating a mold that can withstand the high temperatures of molten metal.
Once the mold is prepared, the foam pattern is subjected to heat, which causes it to vaporize, leaving behind a cavity in the sand mold that is a perfect replica of the original foam shape. This process eliminates the need for traditional mold-making methods, which can be time-consuming and labor-intensive. As a result, lost foam casting allows for quicker production cycles and reduced lead times.
Advantages of Lost Foam Casting
One of the primary benefits of lost foam metal casting is its ability to create intricate designs with high dimensional accuracy. The smooth surface finish of the foam pattern translates into a high-quality cast product, reducing the need for extensive machining processes after casting. This not only saves time but also minimizes material waste, making it a more environmentally friendly option.
lost foam metal casting
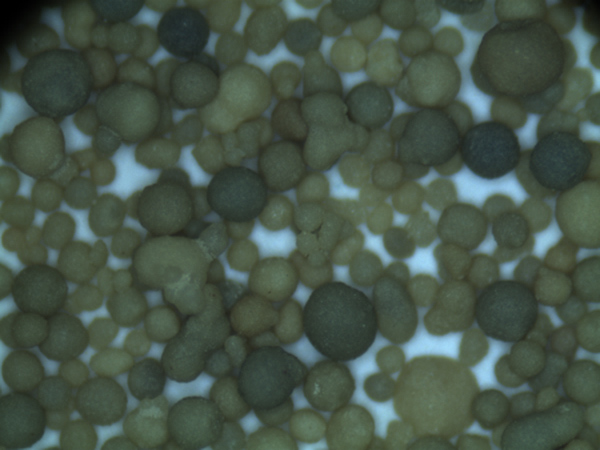
Moreover, the lost foam process is highly versatile. It can be used for a wide variety of metals, including aluminum, cast iron, and various alloys, making it suitable for different applications across industries such as automotive, aerospace, and machinery. This flexibility allows manufacturers to produce both small and large components with ease.
Additionally, the method reduces the overall number of steps involved in the casting process. Since the foam vaporizes during casting, there is no need for the traditional pattern removal and subsequent mold assembly. This streamlining of operations contributes to lower production costs, making it an attractive choice for manufacturers looking to enhance their competitiveness in the market.
Applications in Various Industries
Lost foam casting has found applications in numerous sectors due to its unique advantages. In the automotive industry, for example, it is used to produce engine blocks, transmission housings, and other critical components where precision and durability are essential. The aerospace sector also benefits from lost foam casting, as it allows for the creation of lightweight yet strong parts that meet stringent safety standards.
Furthermore, the process is gaining popularity in the manufacturing of industrial equipment and machinery. The ability to produce components with complex geometries and tight tolerances is a significant advantage in maintaining the performance and reliability of these machines.
Conclusion
In conclusion, lost foam metal casting represents a significant advancement in the field of metal fabrication. Its unique combination of efficiency, precision, and versatility makes it a preferred choice for manufacturers across various industries. As technology continues to evolve, the adoption of lost foam casting is likely to increase, paving the way for innovative designs and high-quality components that meet the demands of the modern market. With its potential for reducing costs and improving production efficiency, lost foam casting is poised to shape the future of metal casting processes.
Post time:Urr . 22, 2024 03:21
Next:Exploring the Art and Techniques of Sand Casting in Metalworking Projects