Different Types of Sand Casting An Overview
Sand casting is a widely used metal casting process that has been employed for centuries due to its versatility, cost-effectiveness, and the ability to produce complex shapes. This method utilizes sand as the primary mold material, with other additives to enhance its properties. Depending on the requirements of the casting project, different types of sand casting can be utilized, each serving unique applications and providing distinct benefits.
1. Green Sand Casting
Green sand casting is the most common type of sand casting, typically made of a mixture of sand, clay, and water. The term green refers to the moisture content in the sand-mold mixture, which aids in binding the sand grains together. This type of mold is easy to produce and offers excellent adaptability for small to medium-sized production runs. The molds are formed through a simple packing process, and once the metal is poured, the mold is broken away to reveal the cast object.
One of the key advantages of green sand casting is its cost-effectiveness, as it requires minimal equipment and is suitable for a wide variety of shapes and sizes. Furthermore, the sand can be reused multiple times, making it environmentally friendly. However, green sand molds do have limitations in terms of surface finish and dimensional accuracy.
Resin sand casting employs a mixture of sand and a resin binder, which hardens when exposed to heat. This method produces molds with superior strength and thermal resistance, enabling the casting of intricate designs and achieving finer surface finishes. The resin sand mold can withstand higher temperatures, meaning that it is ideal for molten metals with high pouring temperatures, such as aluminum and copper alloys.
The use of resin sand casting has grown in various industries due to its precision and reliability. However, it is worth noting that the cost of resin sand molds typically exceeds that of traditional green sand molds, and the production process is generally more complex.
different types of sand casting
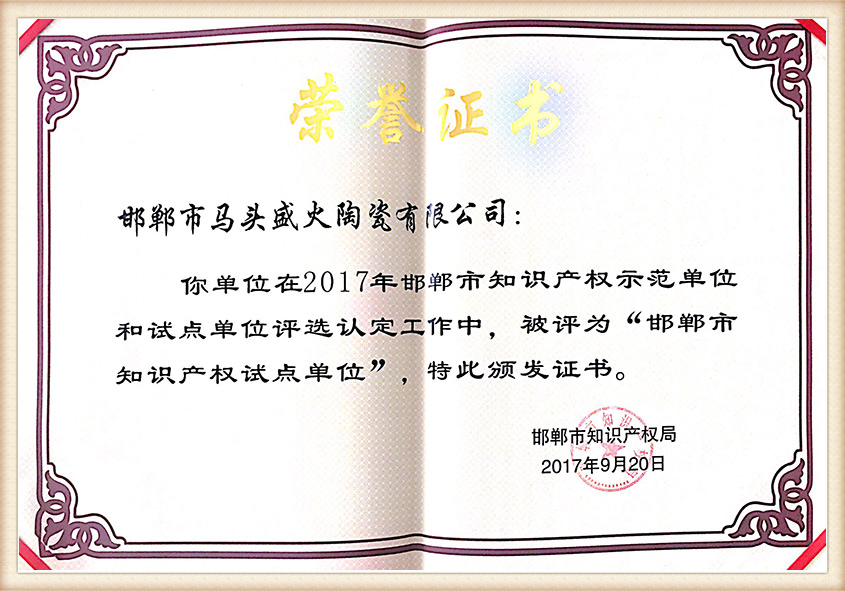
3. Shell Sand Casting
Shell sand casting is a type of sand casting that utilizes a thin shell mold made from a mixture of fine sand and resin. The process begins by heating a metal pattern to a specific temperature, causing the resin to bond with the sand and form a shell around the pattern. Once the shell is formed and sufficiently cured, it is removed from the pattern and assembled for metal pouring.
The primary advantage of shell sand casting is its ability to create highly detailed and intricate designs while providing an excellent surface finish. This method is particularly valuable in industries that require precision, such as aerospace and automotive. However, like resin sand casting, shell sand casting tends to be more expensive and requires specialized equipment.
4. Lost Foam Casting
Lost foam casting is a unique sand casting process that involves creating a pattern from foam, which is then coated with sand. The pattern is placed in a mold box, and molten metal is poured over it. As the metal fills the mold, the foam pattern evaporates, leaving behind the desired shape. This process allows for highly complex geometries and excellent surface finishes, comparable to that of shell sand casting.
The primary benefits of lost foam casting are its capability to produce intricate designs along with minimal tooling requirements. Additionally, there are no draft angles needed since the foam pattern evaporates, making it an efficient option for a diverse range of applications. However, challenges such as foam cost and the need for precise temperature control indicate that this process is best suited for specific projects.
Conclusion
Each type of sand casting has its own set of advantages and challenges, and the selection of a particular method depends on the project requirements, including the complexity of the design, the size of the production run, and the desired surface finish. Understanding these different types of sand casting allows engineers and manufacturers to make informed decisions that can enhance the effectiveness and efficiency of their casting operations. Whether for industrial components or artistic creations, sand casting remains a fundamental process in metal fabrication today.
Post time:Aza . 09, 2024 00:44
Next:Exploring the Enchantment of Golden Sand Beaches and Vibrant Sunsets