Understanding Different Types of Foundry Sand
Foundry sand plays a crucial role in the metal casting process, serving as the primary material in the creation of molds and cores, which house the metal being cast. The properties of the sand significantly influence the quality of the final product, making the choice of foundry sand vital. Various types of foundry sand are available, each with its specific properties and applications.
1. Silica Sand
Silica sand, primarily composed of silicon dioxide (SiO2), is the most commonly used foundry sand. Its excellent thermal stability, high melting point, and ability to withstand thermal shock make it ideal for metal casting processes. This sand typically undergoes a process of washing and drying to remove impurities. Its granule size can vary, allowing for both fine and coarse applications, depending on the desired properties of the mold. Silica sand is especially favored in ferrous metal casting because it provides a smooth finish and excellent detail reproduction.
2. Resin-Coated Sand
Resin-coated sand is produced by coating silica sand with a resin binder, enhancing its properties for high-performance applications. This type of sand is ideal for complex shapes and thin-walled castings due to its ability to retain its form during the casting process. The resin bonds the grains together and improves dimensional accuracy and surface finish. However, the use of resin-coated sand requires careful handling and temperature control during casting since the resin can degrade under excessive heat.
3. Zircon Sand
different types of foundry sand
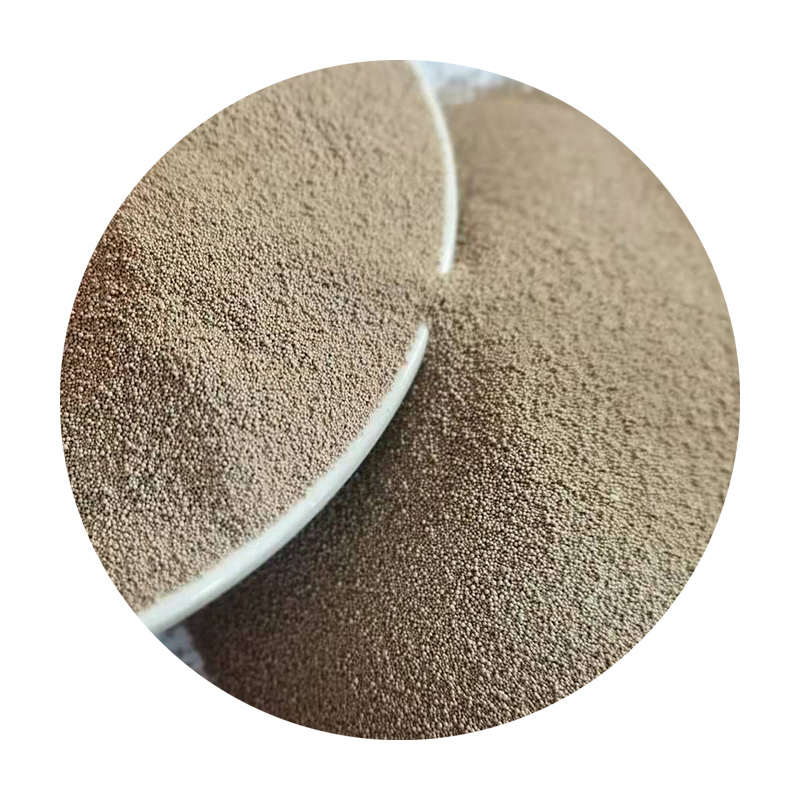
Zircon sand, derived from the mineral zircon, is known for its high melting point and low thermal expansion. As a result, it can withstand extreme temperatures and is often used in high-precision applications. Zircon sand is particularly beneficial for iron and steel castings, providing excellent surface integrity. Despite being more expensive than silica sand, its unique properties make it a valuable choice for specialized casting processes.
4. Chromite Sand
Chromite sand, derived from chromite ore, possesses high thermal stability and excellent resistance to metal penetration. This type of sand is commonly used in steel and iron foundries, especially for casting high-quality metal products. Its ability to reduce casting defects and improve dimensional accuracy makes it a popular option for critical applications such as turbine components and high-performance machinery parts.
5. Olivine Sand
Olivine sand is another specialized foundry sand that is magnesium-iron silicate based. It offers a good balance of properties, including high refractoriness and thermal stability, making it suitable for a variety of foundry applications. Olivine sand is less prone to expansion than silica sand, which minimizes the risk of casting defects. Furthermore, it is environmentally friendly due to its natural origin and low free silica content.
In conclusion, the choice of foundry sand significantly impacts the quality and efficiency of the casting process. Understanding the different types of foundry sand—such as silica, resin-coated, zircon, chromite, and olivine—allows foundries to select the most appropriate material for their specific applications. Each type of sand brings unique advantages that can enhance the quality of castings, reduce defects, and improve overall production efficiency.
Post time:Urr . 06, 2024 17:38
Next:sand preparation in foundry