Advantages and Disadvantages of Sand Casting Process
Sand casting is a widely used metal casting process that involves the creation of a mold from sand and the pouring of molten metal into that mold to create a desired shape. This method has been utilized for millennia due to its versatility and cost-effectiveness. However, like any manufacturing process, sand casting comes with its own set of advantages and disadvantages.
Advantages of Sand Casting
1. Cost-Effectiveness One of the most significant advantages of sand casting is its low cost. The materials used, mainly sand and a binder, are relatively inexpensive compared to those used in other casting processes. This makes sand casting an attractive option for both small-scale and large-scale production.
2. Versatility Sand casting is compatible with a wide range of metals and alloys, including iron, aluminum, bronze, and steel. It can produce both simple and complex shapes, making it suitable for various applications, from automotive parts to intricate sculptures.
3. Large Size Capability Sand casting molds can be made large enough to accommodate substantial parts or components, which is a significant advantage for industries that require oversized castings, such as automotive and aerospace.
4. Mold Adaptability The flexibility of sand molds allows for easy modifications to designs. This adaptability means that prototypes and one-off designs can be produced without the extensive lead times and preparation associated with other methods.
5. No Need for Specialized Equipment Unlike other casting processes that may require expensive machinery, sand casting can often be performed with standard tools and equipment, making it more accessible for small businesses and hobbyists.
6. Good Surface Finish While not the best among all casting methods, sand casting can produce a reasonably good surface finish. Using finer sand and additional finishing processes can improve the final product's quality.
advantages and disadvantages of sand casting process
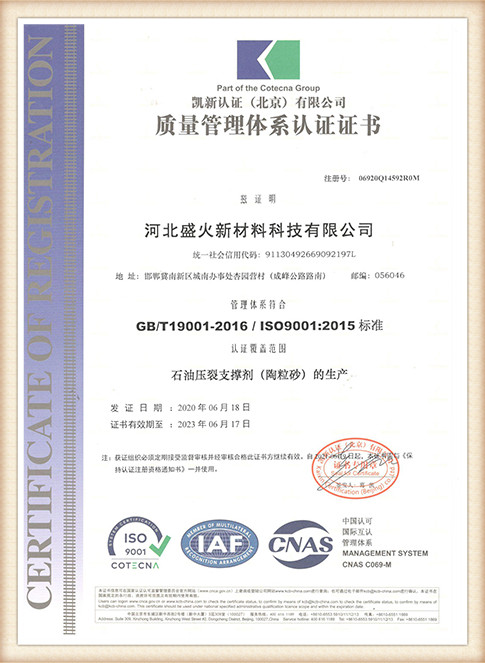
Disadvantages of Sand Casting
1. Lower Dimensional Accuracy One of the primary drawbacks of sand casting is that it does not provide the same level of precision as other casting methods, such as investment casting or die casting. Tolerances may not be as tight, which can result in additional machining or finishing requirements.
2. Surface Roughness Although sand casting can achieve a decent surface finish, it generally has a rougher surface compared to other processes. This roughness may require post-processing, especially for parts that demand high aesthetics or are functionally critical.
3. Labor-Intensive The sand casting process can be labor-intensive, especially in the mold preparation and metal pouring steps. Skilled labor is often necessary to ensure the quality of molds and the accuracy of pouring, leading to higher labor costs.
4. Limited Production Rate Sand casting is not as efficient for high-volume production as methods like die casting. Each mold needs to be prepared, and the process can be slower, which can be a limitation for manufacturers requiring large quantities in a short period.
5. Environmental Concerns The binding agents used in sand casting can sometimes be harmful to the environment, and dust from the sand can pose health risks to workers. Furthermore, the disposal of used sand and other materials needs to be managed properly to mitigate ecological impacts.
6. Porosity Issues Sand castings are prone to defects such as porosity, which can weaken the finished part. These defects can arise from the trapped gases during solidification, leading to pressure and voids within the metal.
Conclusion
In summary, sand casting is an essential manufacturing process with numerous advantages, including cost-effectiveness, versatility, and the ability to produce large components. However, the process also encompasses drawbacks such as lower dimensional accuracy and labor intensity. Understanding these pros and cons is crucial for manufacturers when selecting the appropriate casting method for their specific needs. By considering the intended application, production scale, and material requirements, businesses can make informed decisions that optimize their manufacturing processes.
Post time:Abe . 03, 2024 13:47
Next:smooth 3d prints without sanding