Why Sand Casting is Preferred in Manufacturing
Sand casting is one of the oldest and most versatile manufacturing processes in the metalworking industry. It involves creating a mold from sand to shape a metal object, and it has been used for centuries in various applications. The choice of sand casting over other methods has several compelling advantages that make it the preferred option for many manufacturers.
1. Cost-Effectiveness
One of the primary reasons why sand casting is favored is its cost-effectiveness. The materials used for sand molds, such as sand itself, clay, and water, are relatively inexpensive compared to the metal or plastics used in other manufacturing processes. Additionally, the setup for sand casting is minimal compared to other casting methods, which often require complex machinery and tooling. This lower initial investment makes sand casting an attractive option for both small-scale production and large-volume manufacturing.
2. Versatility
Sand casting is highly versatile and can accommodate a wide range of metals, including aluminum, copper, iron, and steel. This flexibility allows manufacturers to produce a diverse array of components, from intricate designs to large heavy-duty parts. The process can also be adapted to manufacture both ferrous and non-ferrous metals. Furthermore, sand casting can create parts of various sizes, which is beneficial for different industries, from automotive to aerospace.
Sand casting offers designers and engineers the ability to create intricate shapes and complex designs that would be challenging to produce using other methods. The malleability of sand allows for detailed molds that capture fine features and details. Advanced sand casting techniques, such as lost foam or green sand casting, can further enhance the detail level. As a result, components can be manufactured with tight tolerances, which is essential for performance-critical applications.
why sand casting is preferred
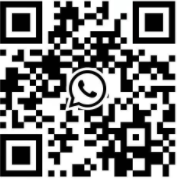
4. Large Production Runs
For large production runs, sand casting is exceptionally efficient. Once the mold is created, it can be reused multiple times, significantly reducing the time and cost involved in producing each individual part. Automation in the sand casting process has also improved productivity, allowing manufacturers to produce high volumes of parts in shorter timeframes while maintaining quality.
5. Easy Mold Making
Creating sand molds is a straightforward process compared to other casting methods like die casting or investment casting. Molds can be made quickly using sand mixtures, and modifications to the mold design can be done with relative ease. This attribute is particularly advantageous when design iterations are needed, as changes can be implemented without extensive retooling.
6. Environmental Considerations
With the growing emphasis on sustainability and environmentally friendly practices, sand casting presents certain advantages. The sand used in the casting process can often be reused multiple times before it requires disposal, minimizing waste. Additionally, compared to other casting processes that may involve hazardous materials, sand casting generally employs materials that have less environmental impact.
Conclusion
In conclusion, sand casting is preferred in manufacturing due to its cost-effectiveness, versatility, ability to produce complex designs, efficiency in large production runs, ease of mold making, and environmental sustainability. These advantages position sand casting as a reliable option for manufacturers looking to produce high-quality metal components across various industries. As technology and techniques continue to advance, the relevance of sand casting is likely to endure, making it a vital process in the metal casting landscape.
Post time:okt. . 17, 2024 03:48
Next:supersand