Understanding the Sand Casting Process
Sand casting, also known as sand mold casting, is a versatile and widely used metal casting process that has been employed for centuries. It is particularly favored for its ability to create large, complex metal components with high tolerance levels. This process utilizes sand as the primary molding material and is suitable for various metals, such as aluminum, bronze, iron, and even some steels. In this article, we will explore the sand casting process, its advantages, challenges, and applications.
The Sand Casting Process
The sand casting process can be divided into several key steps
1. Pattern Making The initial phase involves creating a pattern of the desired object. This pattern is typically made from materials such as metal, plastic, or wood. The pattern is a replica of the final product and is slightly larger to accommodate the addition of a sand mold.
2. Mold Creation The pattern is placed in a flask (a container made of metal or wood) and sand is packed around it. The sand used is usually mixed with a binding agent (often clay) and water to make it cohesive. The flask is then separated, and the pattern is removed, leaving behind a cavity in the shape of the object.
3. Core Making In cases where the casting requires internal features or hollow sections, cores are created. Cores are made from sand mixed with a binder and are placed inside the mold cavity before the metal is poured.
4. Melting the Metal The metal to be cast is heated to its melting point, typically in a furnace. Different types of furnaces, such as induction, crucible, or electric arc furnaces, can be used depending on the metal and production volume.
5. Pouring Once the metal is molten, it is poured into the prepared sand mold. This process requires careful handling to avoid defects in the casting. The pouring must be done in a controlled manner to ensure that the mold fills completely and evenly.
6. Cooling and Solidification After pouring, the molten metal cools and solidifies within the mold. The cooling rate can affect the properties of the final casting, including its microstructure and mechanical properties.
7. Mold Removal and Finishing Once the casting has cooled, the sand mold is broken away to reveal the finished casting. This step often involves knocking off or shaking out the sand. The casting may then undergo various finishing processes, such as grinding, machining, or surface treatment, to meet the required specifications.
Advantages of Sand Casting
Sand casting offers several advantages, making it a preferred choice for many manufacturers
what is sand casting process
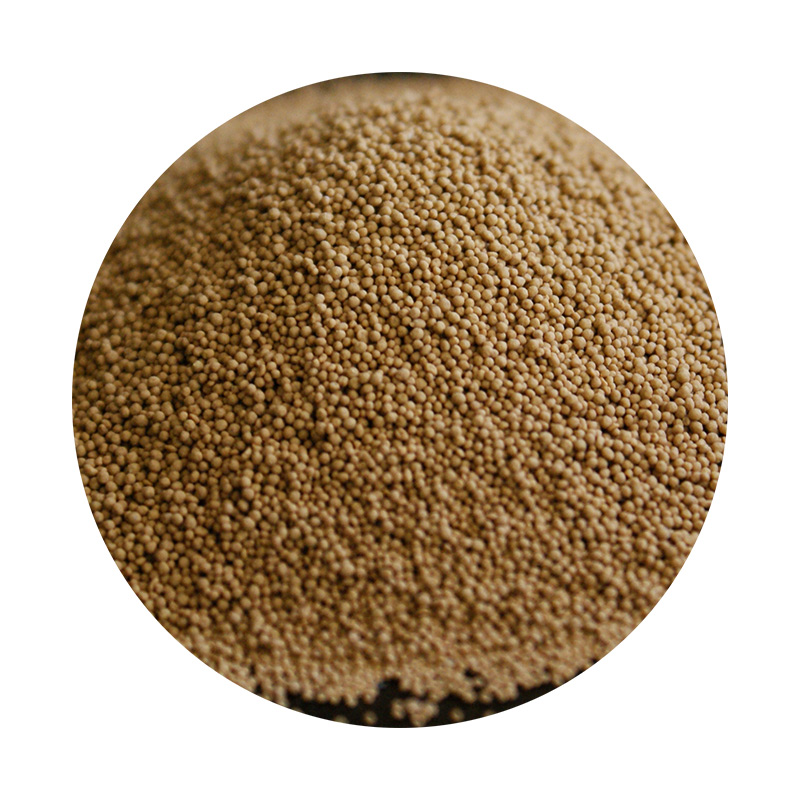
- Cost-Effective The materials used in sand casting, particularly sand, are inexpensive and readily available
. This makes it an economical choice for low- to medium-volume production.- Versatility Sand casting is capable of producing a wide variety of shapes and sizes, from small components to large industrial parts.
- Complex Geometries The process can accommodate intricate designs and complex geometries, making it suitable for a range of applications, including automotive and aerospace components.
- Ease of Modification Patterns can be easily modified or new ones created, allowing for flexibility in design and rapid prototyping.
Challenges of Sand Casting
Despite its many benefits, sand casting also comes with challenges
- Surface Finish Castings produced through sand casting may require additional finishing processes to achieve a smooth surface, as the sand can leave a rough texture.
- Dimensional Accuracy While sand casting can provide reasonable tolerances, it is generally less precise than other casting methods like investment casting or die casting.
- Mold Breakage The sand molds are typically single-use, which means that they need to be recreated for each casting, adding to production time for large quantities.
Applications of Sand Casting
Sand casting is utilized in various industries, including automotive, aerospace, machinery, and art. It is used to manufacture components such as engine blocks, transmission cases, and other essential parts due to its versatility and reliability.
Conclusion
In summary, sand casting is an age-old process that remains vital in modern manufacturing. Its ability to produce complex shapes and accommodate various metals makes it an essential method for creating high-quality components in numerous industries. As technology advances, innovations in sand casting techniques will continue to enhance its efficiency and effectiveness, maintaining its relevance in the ever-evolving landscape of manufacturing.
Post time:okt. . 11, 2024 13:01
Next:Endless Delights in a World of Super Sands Adventure