Sand Preparation in Foundry A Critical Process for Quality Casting
The foundry industry plays a crucial role in manufacturing, particularly in the production of metal castings used in various applications across multiple sectors, including automotive, aerospace, and machinery. Among the several factors that influence the quality of castings, the preparation of sand is paramount. Sand serves as the primary molding material, and its properties significantly impact the final product's accuracy and surface finish.
Understanding Sand Composition
In the foundry, the most commonly used type of sand is silica sand, composed mainly of silicon dioxide (SiO2). Its rounded grains, excellent thermal stability, and ability to withstand high temperatures make it an ideal material for casting molds. However, not all sands are created equal. The specific characteristics of sand, such as grain size, shape, and moisture content, can greatly influence the performance of the mold. Therefore, careful selection and preparation of sand are vital steps in ensuring high-quality castings.
The Sand Preparation Process
The process of sand preparation involves several key stages, from sourcing raw materials to mixing and conditioning the sand
. This process can be broadly divided into the following steps1. Sand Sourcing The first step is obtaining high-quality silica sand from reliable suppliers. Properties such as uniformity in particle size, low clay content, and the absence of impurities are essential for optimal performance. Some foundries also utilize synthetic sands designed to meet specific casting requirements.
2. Screening Once the sand is sourced, it undergoes screening to remove any oversized particles and contaminants. This is crucial because larger particles can create defects in the mold, leading to imperfections in the castings. Effective screening ensures that the sand used is uniform in size, contributing to better mold strength and precision.
sand preparation in foundry
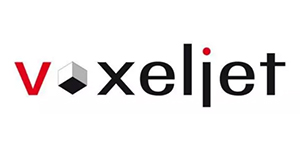
3. Reclamation In modern foundries, sand reclamation is an important process. Used sand from previous moldings is reclaimed and processed to remove impurities and restore its properties. This step not only reduces waste but also cuts down on costs associated with purchasing new sand. Reclamation systems typically include mechanical processes such as crushing, separating, and cleaning.
4. Mixing and Conditioning The prepared sand is then mixed with a bonding agent, which holds the sand grains together to form a solid mold structure. Common bonding agents include clay or resin. The mixture is then conditioned by adding water to achieve the desired moisture content, which is vital for ensuring the right consistency and strength in the mold. The moisture content must be carefully controlled; too much water can lead to defects like steam holes and blowouts, while too little can result in weak molds.
5. Testing and Quality Control Throughout the sand preparation process, quality control is essential. Tests for properties such as permeability, cohesiveness, and compressive strength are performed to ensure the sand meets specific standards. Foundries often use standardized tests, such as the AFS (American Foundry Society) results, to quantify these properties and ensure consistency.
Importance of Proper Sand Preparation
Proper sand preparation is critical to producing high-quality castings. Inadequate sand preparation can lead to a range of defects in the final product, including poor surface finish, dimensional inaccuracies, and internal voids. Moreover, investing in quality sand preparation technology can significantly enhance productivity and reduce production costs by minimizing rework and scrap rates.
Conclusion
In conclusion, sand preparation in foundry operations is a vital process that directly impacts casting quality. By ensuring the right selection, conditioning, and testing of sand, foundries can achieve superior results in their casting processes. As the industry continues to evolve, advancements in sand preparation technologies and practices will be essential for meeting the increasing demands for efficiency and quality in metal casting. Emphasizing this area can lead to improved product performance, reduced costs, and a sustainable approach to foundry operations.
Post time:okt. . 22, 2024 08:05
Next:foundry sand uses