The Versatility and Applications of Sand Casting
Sand casting, one of the oldest and most widely used metal casting processes, offers a combination of versatility, cost-effectiveness, and ease of use that makes it a go-to choice across various industries. This technique involves creating a mold from sand and using it to cast metal parts. With applications ranging from automotive to aerospace and art, understanding the uses of sand casting reveals its significance in modern manufacturing.
Introduction to Sand Casting
At its core, sand casting involves mixing sand with a binder to form molds. The process typically begins with the creation of a pattern that represents the desired metal part. This pattern is then placed within a flask, which houses the sand mixture. Once the sand is packed around the pattern and the binder is set, the pattern is removed, leaving a hollow cavity that mirrors the part's shape. Molten metal is poured into this cavity, allowing it to cool and solidify, after which the sand mold is broken away to reveal the final casting.
Automotive Industry
One of the primary applications of sand casting is in the automotive industry. Many components, such as engine blocks, transmission cases, and various structural supports, are manufactured using this method. The ability to create complex geometries at a relatively low cost makes sand casting an ideal choice for producing both small and large quantities of parts. Moreover, there is a high demand for custom components in automotive production, and sand casting easily accommodates such requirements.
Aerospace Applications
The aerospace sector also relies heavily on sand casting, particularly for parts that require high strength-to-weight ratios and intricate designs. Components like turbine housings, brackets, and even some engine components can be effectively produced through this casting process. The aerospace industry often needs parts made from alloys that can withstand extreme temperatures and stress, which sand casting can adequately provide.
sand casting uses
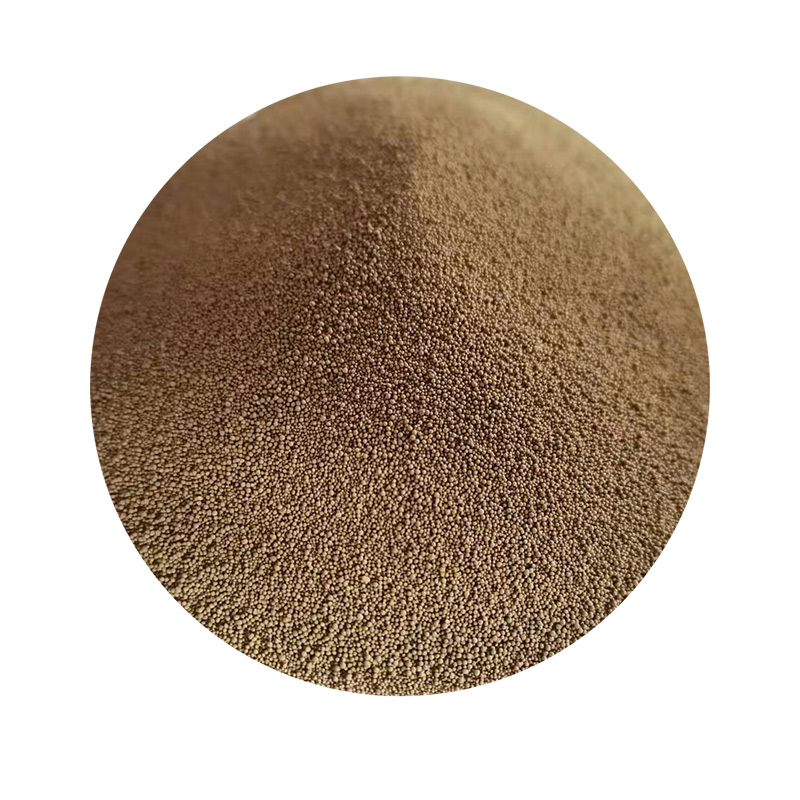
Industrial Machinery
Industrial equipment and machinery components, such as gears, housings, and brackets, often utilize sand casting due to its ability to produce strong and durable parts. The ability to produce heavy and complicated shapes means that essential parts for heavy machinery can be manufactured quickly and efficiently. Additionally, the repair and replacement of worn-out parts is simplified by this casting technique, reducing downtime and maintenance costs.
Artistic and Architectural Uses
Beyond industrial applications, sand casting finds its place in art and architecture. Artists and sculptors often use sand casting to create unique pieces, including sculptures and decorative elements. The process allows for intricate designs to be replicated, making it a popular choice for one-of-a-kind art pieces. In architecture, decorative facades and artistry can be produced using sand casting techniques, showcasing the aesthetic potential of this method.
Advantages of Sand Casting
The advantages of sand casting are numerous. Firstly, the materials required (sand and a binder) are easily accessible and inexpensive. This makes the process highly cost-effective, especially for smaller production runs. Another key benefit is the flexibility in mold design; sand casting can accommodate complex shapes and large sizes that might be challenging to achieve with other methods like die casting. Furthermore, the reusability of sand makes it an environmentally friendly option in terms of waste production.
Conclusion
In summary, sand casting serves as a fundamental method for producing metal parts across diverse industries. Its applications in automotive manufacturing, aerospace development, industrial machinery, and artistic endeavors underscore its versatility. With continued advancements in materials and techniques, sand casting is likely to remain a prominent casting method well into the future. As industries evolve and demands change, the adaptability and efficiency of sand casting will undoubtedly continue to play a crucial role in manufacturing processes globally.
Post time:nov. . 30, 2024 03:05
Next:foundry sand types