Sand Casting Technology An Overview
Sand casting, also known as sand mold casting, is one of the most commonly used metal casting processes. It involves the creation of a mold from sand, into which molten metal is poured to form a desired shape. This age-old technique dates back thousands of years and continues to be a vital method in various industries today. In this article, we will explore the sand casting process, its advantages, applications, and future prospects.
The Sand Casting Process
The sand casting process consists of several key steps. First, a pattern of the desired object is created, typically made from metal, plastics, or wood. This pattern is used to form the mold, which is usually composed of a mixture of sand and a binding agent. The sand is compacted around the pattern to create a cavity that mirrors the shape of the object to be cast.
Once the mold is formed, the pattern is removed, leaving behind a negative impression. This impression is then carefully assembled, ensuring that any necessary cores are in place to create internal features of the cast object. Next, molten metal is poured into the cavity through a pouring cup or sprue. After the metal has cooled and solidified, the mold is broken apart to reveal the cast part.
Advantages of Sand Casting
Sand casting offers several advantages that make it a preferred choice for many manufacturing processes. Firstly, it is cost-effective. The materials used for sand molds are inexpensive and readily available, making it an attractive option for both small and large-scale production. Additionally, the process allows for the casting of intricate shapes and designs, which would be difficult to achieve with other methods.
Another significant advantage is the flexibility in terms of materials. Sand casting can accommodate a wide range of metals, including aluminum, iron, bronze, and various alloys. This versatility makes it suitable for different applications across various industries, from automotive to aerospace.
sand casting technology
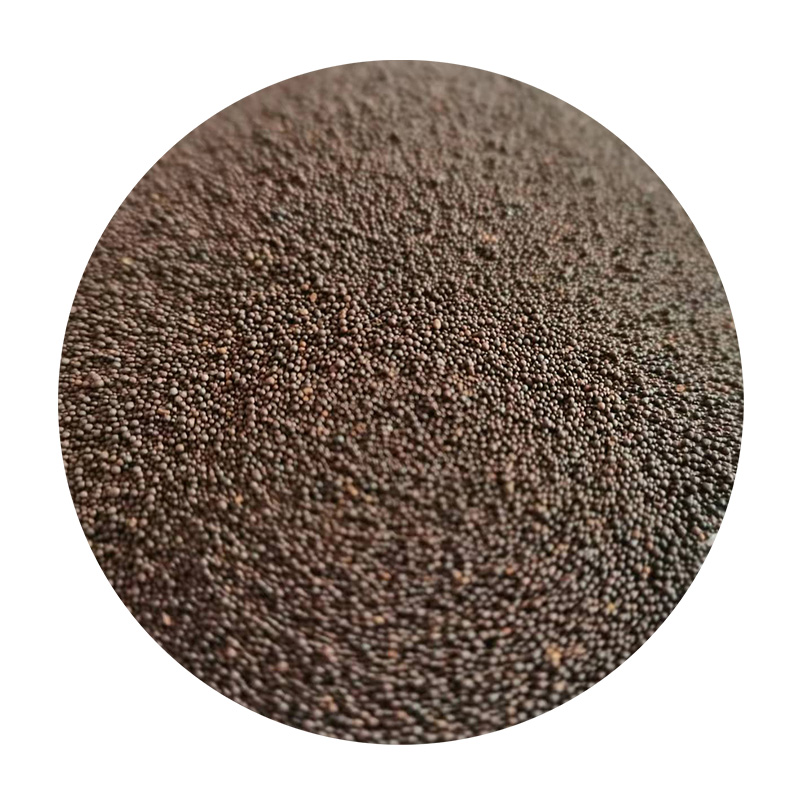
Moreover, sand casting is notable for its tolerance to high temperatures, which allows for the casting of large and complex components without the risk of deformation. This property, combined with its capability to produce parts with excellent surface finish, further enhances its appeal in manufacturing.
Applications of Sand Casting
The applications of sand casting are vast and diverse. In the automotive industry, sand casting is commonly used to produce engine blocks, transmission housings, and other critical components. The aerospace sector also relies on sand casting for parts that demand high strength and lightweight characteristics.
Moreover, sand casting plays a crucial role in the production of industrial machinery, pumps, valves, and a variety of tools. The construction sector benefits from it as well, using sand cast components for structural and decorative elements. Its ability to create custom designs makes it an ideal choice for artistic and sculptural applications as well.
Challenges and Future Prospects
Despite its advantages, sand casting is not without challenges. One of the primary concerns is the environmental impact associated with the production and disposal of molds. The sand used can become contaminated and may require proper disposal or recycling. Additionally, achieving high levels of precision can be difficult, which may necessitate additional machining processes to fulfill stringent tolerances required in certain applications.
To address these challenges, advancements in technology are being explored. Innovations such as 3D printing of molds and cores are beginning to revolutionize the sand casting process by enabling more complex geometries and reducing material waste. The integration of automation and robotics is also on the horizon, promising to enhance production efficiency and quality.
In conclusion, sand casting technology remains a cornerstone of the manufacturing industry. Its cost-effectiveness, versatility, and capability to produce intricate designs make it an invaluable process across a multitude of sectors. As technological advancements continue to emerge, sand casting is poised for further evolution, enabling manufacturers to meet the increasing demands for precision, efficiency, and sustainability in the modern market. The future of sand casting looks promising, with continuous improvements ensuring its relevance in an ever-changing industrial landscape.
Post time:dets. . 14, 2024 05:26
Next:Understanding the Role of Sand in Casting Processes and Its Impact on Quality