Sand Casting Techniques An Overview
Sand casting, also known as sand mold casting, is a versatile and widely used metal casting process that involves the creation of a sand mold in which molten metal is poured to form a desired object. This method has been utilized for centuries, and its appeal lies in its simplicity, cost-effectiveness, and ability to produce complex shapes. In this article, we will delve into the various techniques associated with sand casting, as well as its applications, advantages, and disadvantages.
The Fundamentals of Sand Casting
The sand casting process begins with creating a pattern, which is a replica of the object to be cast. The pattern is typically made from wood, metal, or plastic and is designed to be slightly larger than the final product to accommodate for shrinkage that occurs when the metal cools. The pattern is placed in a mold box, and sand mixed with a binding agent is packed around it to form a mold.
Once the mold is formed, the pattern is removed, leaving a cavity that reflects the shape of the object. The mold is then often coated with a release agent to facilitate the removal of the final casting. After preparing the mold, molten metal is poured into the cavity through a sprue, a channel designed to allow the liquid metal to flow into the mold.
Sand Types and Their Use
A crucial aspect of sand casting is the type of sand used. The most commonly employed sand is silica sand, valued for its availability and heat resistance. However, the addition of clay and water can enhance its binding properties and improve mold integrity. Other materials, such as zircon sand and olivine sand, are also used, although they come with a higher cost.
The choice of sand can impact the quality of the final casting, influencing factors such as surface finish, dimensional accuracy, and the overall strength of the mold. For instance, finer sand typically produces smoother surfaces but may require more careful handling and preparation.
The Process Steps Involved
sand casting techniques
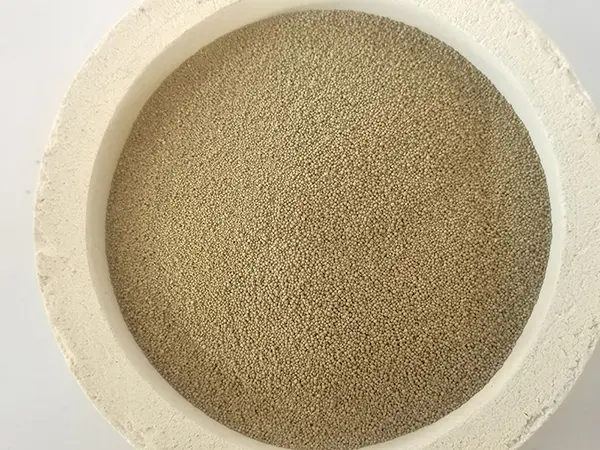
1. Pattern Creation The initial step involves designing and constructing a pattern for the desired object. 2. Mold Making The pattern is pressed into sand to create two halves of the mold, which are then assembled. 3. Melting the Metal The metal is melted in a furnace at high temperatures, depending on the metal type (e.g., aluminum, iron, or bronze). 4. Pouring Once the metal is molten, it is carefully poured into the mold cavity. 5. Cooling The metal is left to cool and solidify. Cooling time can vary based on the thickness and type of metal used. 6. Removing the Casting After cooling, the sand mold is broken away to retrieve the casting. 7. Finishing The final steps typically include cleaning and finishing the casting to remove any excess material or surface imperfections.
Advantages and Disadvantages
One of the significant advantages of sand casting is its flexibility; it can be used to cast a wide range of metals and alloys in various sizes, from small components to large industrial parts. The relatively low cost of materials and setup also makes it an ideal choice for low to medium production runs.
However, sand casting has its drawbacks. The surface finish and dimensional accuracy may not be as high as that achieved through other casting methods, such as investment casting. Additionally, the labor-intensive nature of the process can result in longer lead times, particularly for complex molds.
Applications of Sand Casting
Sand casting finds applications across various industries, including automotive, aerospace, and industrial machinery. Engineers and designers favor it for producing components like engine blocks, cylinder heads, and intricate gear systems. Its ability to accommodate large and heavy castings makes it a preferred choice for manufacturing in many sectors.
Conclusion
In conclusion, sand casting techniques represent a crucial area of interest in manufacturing and engineering. Understanding the different types of sand, the fundamental steps involved in the casting process, and the advantages and disadvantages of this method allows for better planning and execution of casting projects. Despite its challenges, sand casting remains a robust option for producing high-quality metal components across diverse applications, showcasing the ingenuity and utility of this age-old technique.
Post time:dets. . 31, 2024 06:48
Next:difference between die casting and sand casting