Understanding the Sand Casting Process Techniques and Applications
Sand casting, one of the oldest metalworking processes, has stood the test of time due to its versatility and effectiveness in producing complex shapes with relatively low costs. This time-honored technique involves creating a mold from sand to hold molten metal, which subsequently cools to form solid objects. It is widely used across various industries, from automotive to aerospace. In this article, we will delve into the sand casting process, exploring its components, methods, advantages, and applications.
Components of Sand Casting
The primary components of the sand casting process include the pattern, mold, core, and the casting itself.
1. Pattern The pattern is a replica of the object to be cast, made from materials such as wood, metal, or plastic. It is utilized to create the mold cavity in the sand. Patterns can be classified into different types, including solid patterns (for simple shapes) and split patterns (for more complex shapes that require multiple sections).
2. Mold The mold is typically made from a mixture of sand and a binding agent (such as clay or resin). This mixture forms the mold cavity after the pattern is removed. The quality and composition of the sand are crucial, as they determine the mold’s strength and ability to retain its shape during the casting process.
3. Core In cases where internal cavities or hollow sections are needed, cores are used. Cores, which are also made of sand, are placed in the mold before the molten metal is poured. They create the internal geometry of the casting.
4. Casting Once the mold is prepared, molten metal is poured into it, filling the cavity. After cooling, the sand mold is broken away to reveal the finished casting.
The Sand Casting Process
The sand casting process involves several key steps
sand casting processes
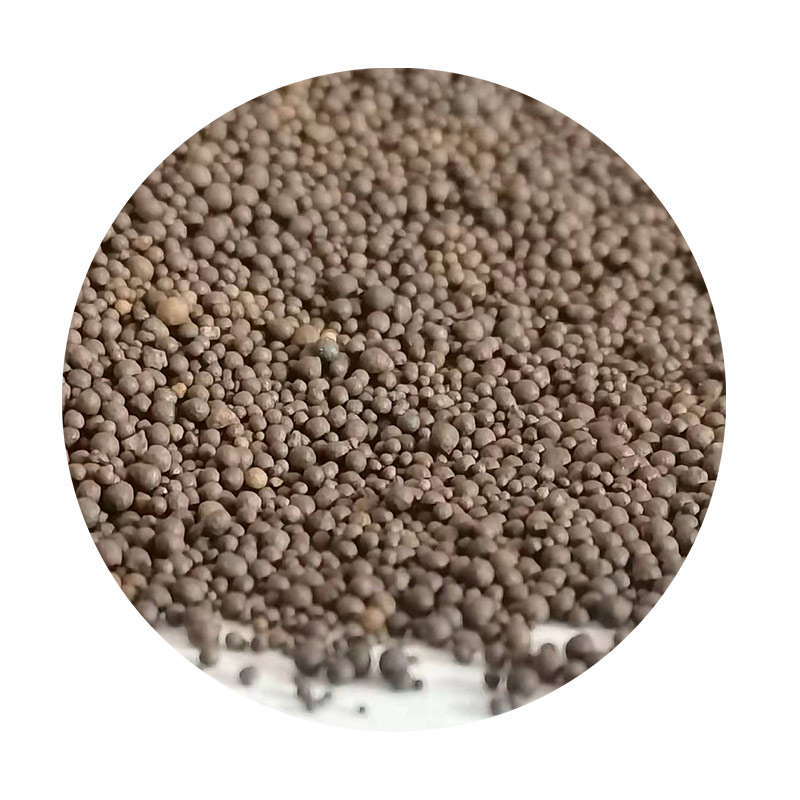
2. Mold Preparation The pattern is then placed in a molding box, and sand is packed around it, forming the mold cavity. This molding sand is typically a mixture of fine sand, clay, and water. Once the sand is compacted, the pattern is removed, leaving a hollow cavity.
3. Core Placement If needed, cores are positioned in the mold to create internal features. The cores are secured in place to prevent them from shifting during the pouring of metal.
4. Melting and Pouring The metal is melted in a furnace and then poured into the mold through a pouring basin and sprue, allowing for even distribution.
5. Cooling and Finishing After the metal solidifies, the sand mold is broken away, and the casting is cleaned. Additional finishing processes, such as grinding or machining, may be performed to achieve the desired surface quality.
Advantages of Sand Casting
One of the primary advantages of sand casting is its ability to produce complex shapes that might be difficult or expensive to achieve with other manufacturing methods. Sand casting is also cost-effective for small to medium production runs, as it requires minimal tooling compared to other casting methods like die casting or investment casting. Additionally, the process is adaptable to a variety of materials, including ferrous and nonferrous metals, making it a go-to choice for many industries.
Applications of Sand Casting
Sand casting is prevalent in various sectors. In the automotive industry, it is used to create engine blocks, transmission cases, and various other components. The aerospace sector utilizes sand casting for parts that require high strength and resistance to thermal stresses, such as turbine housings. Other applications include the production of hardware, decorative items, marine components, and more.
Conclusion
Sand casting remains a vital manufacturing process due to its adaptability and cost-effectiveness. Understanding its components, methods, and applications allows engineers and manufacturers to harness its benefits in producing high-quality metal parts. As technology advances, the sand casting process continues to evolve, integrating new materials and techniques that promise to enhance its efficiency and effectiveness even further. Whether for small-scale artisanal work or large industrial production, sand casting remains an indispensable tool in the world of metalworking.
Post time:dets. . 31, 2024 09:47
Next:Innovative Sand Casting Techniques Through Advanced 3D Printing Solutions