Understanding Sand Casting Processes
Sand casting is one of the most versatile and widely used manufacturing processes in the metalworking industry. This technique involves creating a mold from sand, which is then filled with molten metal to create various components. Understanding sand casting processes is crucial for industries ranging from automotive to aerospace, where precision and reliability are paramount.
The sand casting process begins with the preparation of the mold. Typically, a mixture of fine sand and a binding agent (such as clay) is used to create a mold that can withstand the heat of molten metal. The sand is first compacted around a pattern, which is a replica of the desired part. Patterns can be made of various materials, including metal, plastic, or wood, depending on the complexity of the design and the volume of production needed.
Once the pattern is in place, the sand is packed around it to form a mold. After the sand has been sufficiently compacted, the pattern is removed, leaving behind a cavity that replicates the shape of the desired component. This process can be done in different ways, such as using a two-part mold or a single-piece mold, depending on the part's intricacy and desired finish.
One of the key advantages of sand casting is its ability to produce complex geometries and large parts with ease. The flexibility of sand as a molding material allows for intricate designs that may be challenging to achieve with other manufacturing methods. Additionally, there is a wide range of metals that can be cast using this process, including aluminum, cast iron, bronze, and steel.
sand casting processes
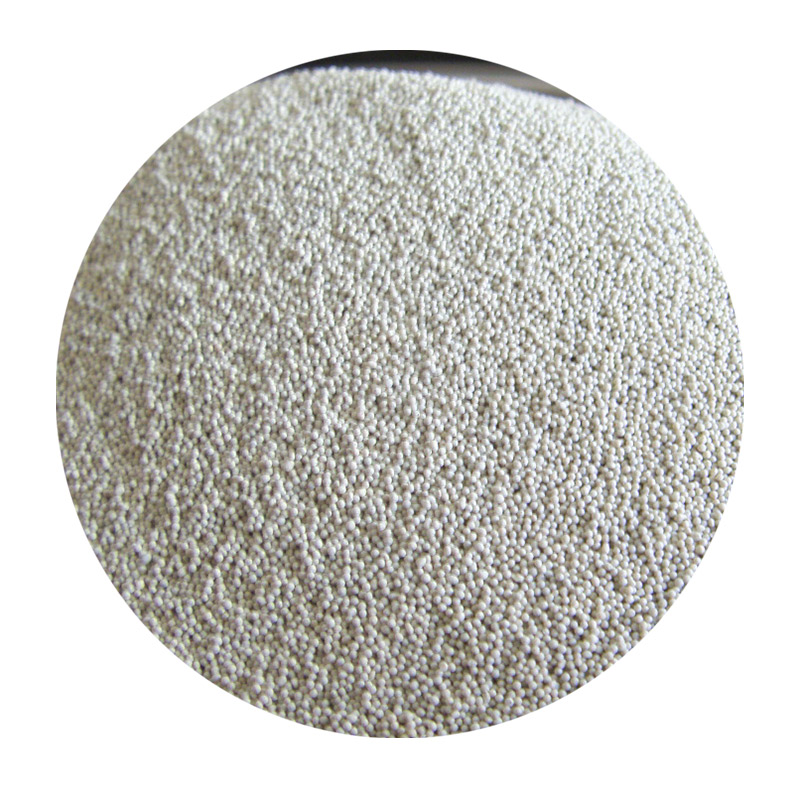
Once the mold is prepared, the next step involves heating the metal until it reaches a molten state. This molten metal is then poured into the mold cavity, filling it and taking the shape of the pattern. The cooling time required for the metal to solidify depends on several factors, including the thickness of the casting and the type of metal being used.
After the metal has solidified, the mold is broken apart to retrieve the casting. This step usually involves some cleanup processes, such as removing excess sand and any surface defects. The final product may require further processing, such as machining, polishing, or coating, to meet the desired specifications and finish.
Despite its numerous advantages, sand casting does have limitations. The surface finish of cast parts may not be as smooth as those produced through other methods, such as forging or machining. Additionally, there can be issues related to sand adhesion and inclusions during the casting process. To mitigate these challenges, advancements in technology and materials continue to minimize defects and improve the overall quality of sand-cast products.
In summary, sand casting processes play a vital role in modern manufacturing. Combining versatility, cost-effectiveness, and the ability to create complex shapes makes this method a popular choice across various industries. As technologies evolve, the sand casting process will likely continue to adapt, leading to even greater precision and efficiency in the production of cast metal components.
Post time:okt. . 31, 2024 07:16
Next:sand casting advantages