Sand Casting 101 An Introduction to the Foundry Process
Sand casting is one of the oldest and most widely used metal casting processes in the manufacturing industry. Its basic principle involves pouring molten metal into a mold made of sand, which solidifies to form the desired shape. This versatile method is applicable to a variety of metals and alloys, making it suitable for producing complex designs and large components.
The Sand Casting Process
The sand casting process begins with the creation of a pattern, which is a replica of the final product. Patterns can be made from various materials, including wood, metal, or plastic, and they must account for material shrinkage as the metal cools. There are two common types of patterns expendable and permanent. Expendable patterns are destroyed to remove the casting, while permanent patterns are reused.
Once the pattern is ready, the next step involves preparing the mold. A mixture of sand, clay, and water is typically used to create a mold that can withstand high temperatures. This sand mixture, known as “green sand,” retains its shape without the need for any additional binding agents when compacted around the pattern. The pattern is placed in a mold box and covered with the sand mixture, which is then compacted to ensure that it holds the shape of the pattern.
After the mold is prepared, it is carefully opened to remove the pattern, leaving a cavity that reflects the design of the part to be cast. The mold is then reassembled, and metal is heated to its melting point in a furnace. Once molten, the metal is poured into the mold cavity through a gating system, which is designed to ensure an even flow and minimize turbulence that could lead to defects.
sand casting 101
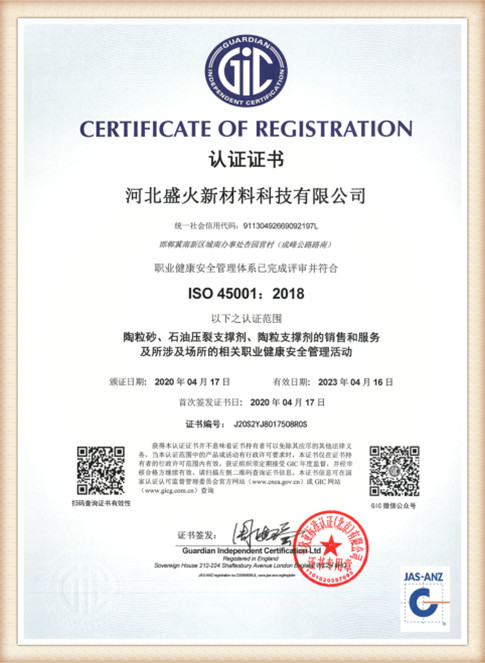
As the molten metal cools, it solidifies and takes on the shape of the mold. The cooling time depends on the size and thickness of the casting, as well as the type of metal used. Once the metal has fully solidified, the mold is broken apart to remove the newly formed casting.
Advantages and Applications
Sand casting offers several advantages. Its capability to produce large and complex parts at a relatively low cost makes it a popular choice for various industries, including automotive, aerospace, and construction. Additionally, the process allows for the use of a wide range of metals, from aluminum and iron to copper and magnesium alloys.
Another significant benefit is its adaptability. Sand casting can accommodate both small and large production runs, making it an excellent option for both prototype development and high-volume manufacturing. Moreover, the molds can be easily modified to create different shapes or sizes, providing flexibility in design.
Conclusion
In summary, sand casting is a time-honored manufacturing process that remains relevant due to its versatility, cost-effectiveness, and ability to produce intricate designs. As technology advances, techniques such as 3D printing and computer-aided design are being integrated into sand casting to enhance precision and efficiency. As a fundamental method in the foundry industry, understanding sand casting allows manufacturers to leverage its advantages and meet the diverse needs of various applications. Whether it's for small-scale prototyping or large-scale production, sand casting continues to play a crucial role in the world of manufacturing.
Post time:okt. . 15, 2024 07:08
Next:Affordable Sand Casting Solutions for Cost-Effective Manufacturing Processes and High-Quality Parts