The Resin Coated Sand Process A Comprehensive Overview
The resin coated sand process is a cutting-edge technique used primarily in the manufacturing of metal components. It combines traditional sand casting with advanced materials technology, leading to superior product quality and efficiency. This method is particularly beneficial in industries such as automotive, aerospace, and machinery where precision and performance are critical.
What is Resin Coated Sand?
Resin coated sand consists of standard foundry sand that is coated with a thermosetting resin binder. This coating process enhances the properties of the sand, making it more resilient and capable of creating finer details in castings. The resins used are typically phenolic or furan, which, when heated, bond the sand grains together to form a hard, durable mold.
The Process
1. Preparation of the Sand The first step involves selecting high-quality foundry sand. This sand is often washed and dried to remove impurities that could affect the finish of the final product.
2. Coating the Sand The dry sand is then mixed with resin and a catalyst, which initiates the curing process. It is essential that the mixing is uniform, as uneven distribution can lead to defects in the final casting.
3. Molding Once coated, the sand is packed into mold patterns. The use of the resin enhances the sand’s ability to retain its shape, allowing for intricate designs and thin-walled castings. The molds are created using a variety of techniques, including manual packing or automated machinery, depending on the scale of production.
resin coated sand process
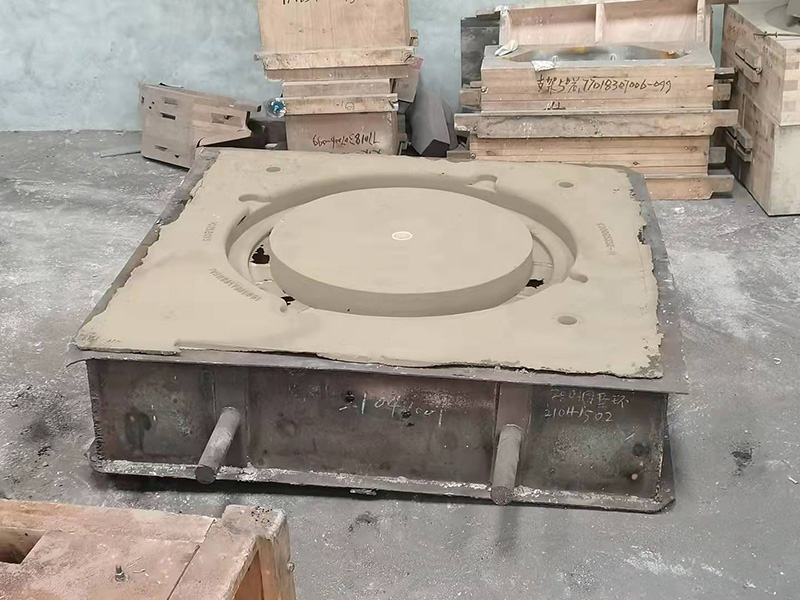
4. Curing The molds are then subjected to heat, which cures the resin and hardens the sand. The heat can be applied in various ways, such as through the use of ovens or induction heating. This curing step is crucial as it solidifies the mold, preparing it for the metal pouring process.
5. Metal Pouring After the molds have cooled down and hardened, molten metal is poured into the prepared molds. The precise nature of the resin coated sand allows for a more uniform cooling of the metal, which is essential for reducing defects like warping and shrinkage.
6. Cooling and Demolding Once the metal has cooled and solidified, the sand mold is broken apart to reveal the cast metal component. The resin coated sand can be easily recycled and reused in subsequent molding processes, making this method both efficient and environmentally friendly.
Advantages of the Resin Coated Sand Process
The resin coated sand process offers a variety of advantages over traditional sand casting methods. These include
- Superior Surface Finish The resin provides a smoother finish on the castings, often eliminating the need for additional machining. - Enhanced Dimensional Accuracy This process allows for tighter tolerances, which is critical in high-performance applications. - Reduced Casting Defects The properties of resin-coated sand significantly diminish issues related to sand penetration and mould collapse. - Environmental Benefits The ability to recycle sand reduces waste and consumption of raw materials.
Conclusion
The resin coated sand process represents a significant advancement in metal casting technology. Its ability to produce high-quality, precision components efficiently makes it a preferred choice in many industries. As manufacturing processes continue to evolve, the adoption of such innovative techniques will be crucial in meeting the demands of modern engineering and production.
Post time:sept. . 10, 2024 01:49
Next:foundry sand composition