Understanding Metal Sand Casting A Comprehensive Overview
Metal sand casting is one of the oldest and most widely used manufacturing processes in the foundry industry. This technique involves pouring molten metal into a mold that has been created by compacting sand around a pattern. Once the metal cools and solidifies, the sand mold is broken apart to retrieve the finished casting. The affordability, versatility, and ability to create large-scale components make sand casting a popular choice in various industries, including automotive, aerospace, and construction.
The Sand Casting Process
The sand casting process can be divided into several key steps
1. Pattern Making The first step in metal sand casting is creating a pattern that will define the shape of the final product. Patterns are typically made from durable materials such as wood, metal, or plastic. They are designed to account for shrinkage and various allowances that will occur during the cooling of the metal.
2. Mold Creation Once the pattern is made, a mold can be created. Sand is mixed with a binding agent, usually a type of clay or resin, and compacted around the pattern. This process can utilize either green sand (moist sand) or chemically bonded sand depending on the requirements of the project. The mold consists of two halves, known as the cope and drag.
3. Core Making For complex shapes with internal cavities, cores made of sand are often required. Cores are inserted into the mold before pouring the metal to ensure the final casting has the desired internal features.
4. Pouring the Metal After the mold and core are prepared, molten metal is poured into the mold cavity through a series of channels known as gates and risers. The temperature and material of the metal can vary greatly, including aluminum, iron, or magnesium, based on the requirements of the casting.
5. Cooling and Solidification Once the metal is poured, it must cool and solidify. This can take anywhere from a few minutes to hours, depending on the size of the casting and the metal used.
6. Mold Removal After sufficient cooling, the sand mold is broken away to reveal the finished casting. This step may involve shaking, blasting, or other methods to separate the sand from the metal.
7. Finishing Processes The final step often involves various finishing operations, such as sanding, machining, and surface treatment. These processes help refine the casting and ensure it meets design specifications.
Advantages of Sand Casting
metal sand casting
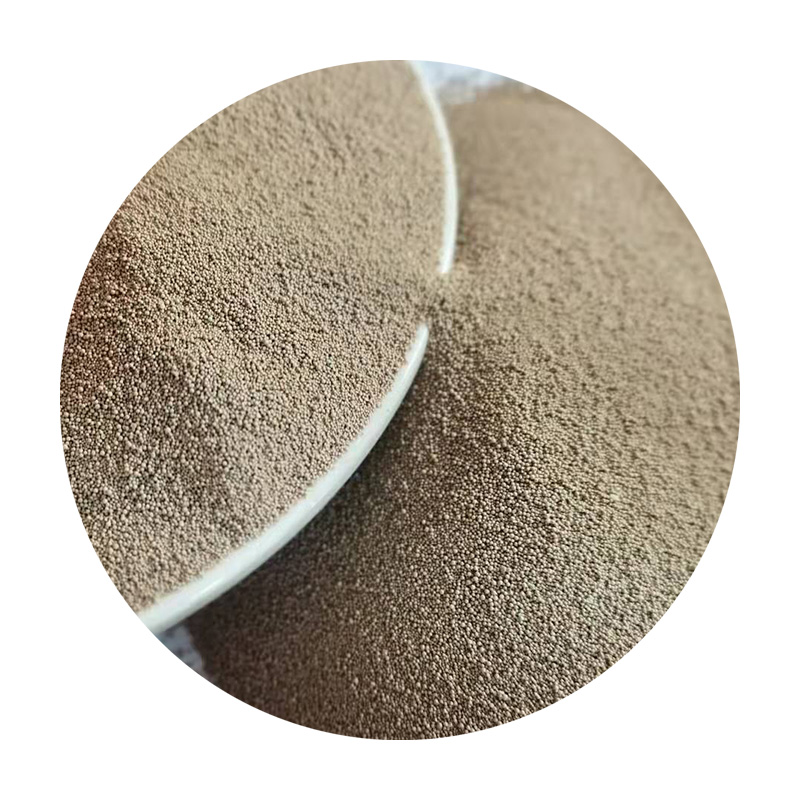
Metal sand casting has numerous advantages that make it a preferred method in many contexts
- Cost-Effective The low cost of raw materials and the relatively simple process make sand casting a cost-effective solution for producing both small and large quantities of parts. - Flexibility A wide range of metals can be cast using this method, including iron, steel, aluminum, and various alloys. This versatility allows for the production of diverse components tailored to specific applications.
- Customizable With the ability to create complex shapes and designs, sand casting is highly customizable. Pattern modifications can be made easily for prototype development or tailored production runs.
- Large Scale Capability Sand casting is particularly suitable for large items, such as engine blocks or heavy machinery components, which may be difficult to produce using other methods.
Challenges and Considerations
While sand casting offers many benefits, there are also challenges associated with the process
- Surface Finish The surface finish of sand-cast products may not be as smooth as those produced by other casting methods, requiring additional finishing processes.
- Dimensional Tolerances The dimensional accuracy of sand castings can be less precise than that of other casting methods, such as investment casting.
- Environmental Concerns The use of sand and binders raises environmental concerns, particularly regarding waste management and the recycling of materials.
Conclusion
Metal sand casting is a fundamental process in the manufacturing industry, celebrated for its versatility and cost-effectiveness. While it is not without challenges, the technique has proven to be a reliable means of creating high-quality castings across a variety of sectors. As technology advances and environmental considerations become increasingly prominent, the sand casting process is likely to evolve, continuing to play a significant role in modern manufacturing. Understanding the intricacies of this process can aid manufacturers in making informed decisions that optimize production efficiency and product quality.
Post time:dets. . 16, 2024 19:10
Next:foundry sand used in construction