The Art of Sand Casting A Comprehensive Guide
Sand casting is one of the oldest and most widely used metal casting processes in the world. Its versatility and simplicity make it an ideal choice for manufacturing a range of components, from small intricate parts to large heavy-duty machinery components. This article explores the sand casting process, its advantages, applications, and best practices to achieve high-quality castings.
The Sand Casting Process
At its core, sand casting involves creating a mold from a sand mixture, pouring molten metal into the mold, and allowing it to cool and solidify. The process can be broken down into several key steps
1. Pattern Making The first step involves creating a pattern that replicates the shape of the final product. Patterns can be made from various materials, including wood, plastic, or metal. They are typically slightly larger than the final item to account for shrinkage during cooling.
2. Mold Preparation Once the pattern is ready, it is pressed into a mixture of sand and binder to create the mold. The sand must be carefully prepared to ensure that it can retain the shape and withstand the molten metal's temperature.
3. Core Making For parts with hollow sections, cores made of a similar sand mixture are inserted into the mold. Cores are essential for creating internal geometries that would be impossible to form otherwise.
4. Pouring After the mold and cores are prepared, the molten metal is poured into the mold cavity. Care must be taken during this step to minimize turbulence, which can introduce defects into the casting.
5. Cooling Once the mold is filled, the metal is allowed to cool and solidify. The cooling time depends on the size and thickness of the casting.
6. Mold Removal After the metal has cooled, the sand mold is broken away to reveal the casting. This step can be done manually or with the help of machinery.
7. Finishing The final step involves removing any excess material, smoothing surfaces, and performing any necessary machining to achieve the desired dimensions and finish.
Advantages of Sand Casting
One of the primary reasons sand casting remains popular in various industries is its numerous advantages
- Cost-Effective Sand casting requires relatively low initial investment, making it economical for both small and large production runs.
- Versatility It can be used for a wide range of metals, including aluminum, brass, iron, and steel. Additionally, it allows for the production of large and complex shapes.
make sand casting
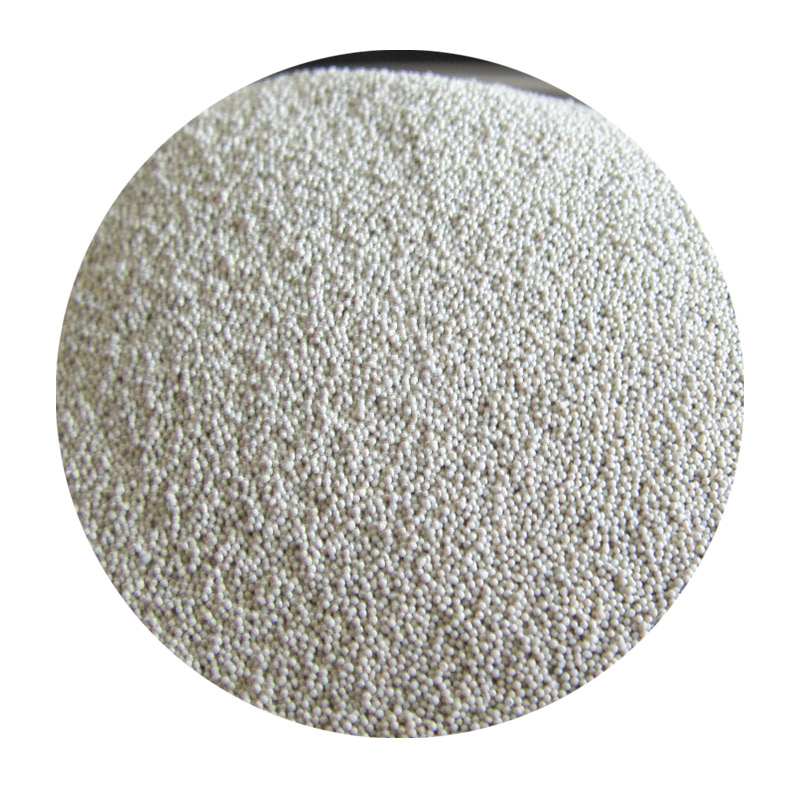
- Customization The process allows for easy modifications to patterns, enabling customizations for specific applications.
- Strength and Durability Castings produced through sand casting are often strong and capable of withstanding high levels of stress and wear
.Applications of Sand Casting
Sand casting is employed in multiple industries, proving its effectiveness and adaptability. Some of the common applications include
- Automotive Industry Producing engine blocks, transmission cases, and a myriad of small parts essential for vehicle manufacturing.
- Aerospace Fabricating components like brackets, rigging fittings, and housings that require high precision and reliability.
- Heavy Machinery Creating large structural components for construction and industrial applications that demand durability.
- Art and Sculpture Artists utilize sand casting techniques to produce unique pieces and sculptures, showcasing creativity in metalwork.
Best Practices for Quality Castings
To ensure high-quality results in sand casting, certain best practices should be followed
- Pattern Quality Invest time in making precise patterns as any imperfections will be reflected in the final casting.
- Mold Consistency Maintain a consistent sand mixture to achieve uniform results. The right balance between sand, binder, and moisture is crucial.
- Temperature Control Monitor the temperature of molten metal closely to prevent defects such as porosity and shrinkage.
- Post-Casting Inspection Inspect castings for defects early in the process to allow for corrective measures before significant resources are invested.
In conclusion, sand casting is a timeless and efficient method for producing a wide range of metal components. By understanding and implementing the steps involved, the benefits, and best practices, manufacturers can harness the full potential of sand casting to meet their specific needs while delivering high-quality products.
Post time:okt. . 10, 2024 15:29
Next:sand casting manufacturer