Lost Foam Castings A Revolutionary Approach to Metal Casting
Lost foam casting is an innovative casting process that has gained popularity in various industries due to its precision and efficiency. This method combines the traditional principles of casting with modern technology, allowing for the production of complex shapes with minimal waste. In this article, we will delve into the fundamentals of lost foam castings, its advantages, applications, and the future of this casting method.
What is Lost Foam Casting?
Lost foam casting is a process that involves creating a pattern made of foam, which is then encased in a sand mold. The pattern is typically made from expanded polystyrene (EPS) foam. The key steps in the lost foam casting process include pattern making, molding, and casting.
1. Pattern Making The process begins with creating a foam pattern that is an exact replica of the final product. This pattern is fabricated using CNC machines or manual labor, depending on the complexity and design specifications.
2. Molding The foam pattern is then coated with a thin layer of fine sand mixed with a binding agent. This mixture creates a mold around the foam pattern. The coating is essential as it provides a surface for the molten metal to flow into and supports the shape during casting.
3. Casting Once the mold is created, it is heated, causing the foam to vaporize. This step is crucial because it leaves behind a cavity that is the exact shape of the original pattern. Molten metal is poured into the cavity, filling the void left by the evaporated foam. After the metal solidifies, the mold is removed, revealing the final cast product.
Advantages of Lost Foam Castings
Lost foam casting offers numerous benefits that make it an attractive option for manufacturers
- Complex Geometries One of the most significant advantages of lost foam casting is its ability to produce complex and intricate shapes that would be challenging or impossible to achieve with traditional casting methods.
- Reduced Material Waste Traditional casting methods often create significant waste material. However, lost foam casting minimizes waste since the foam pattern vanishes during the process, leaving no leftover materials.
- Enhanced Surface Finish The foam pattern can be manufactured to achieve a high-quality surface finish. This characteristic reduces the need for extensive post-processing and machining, thereby saving time and resources.
lost foam castings
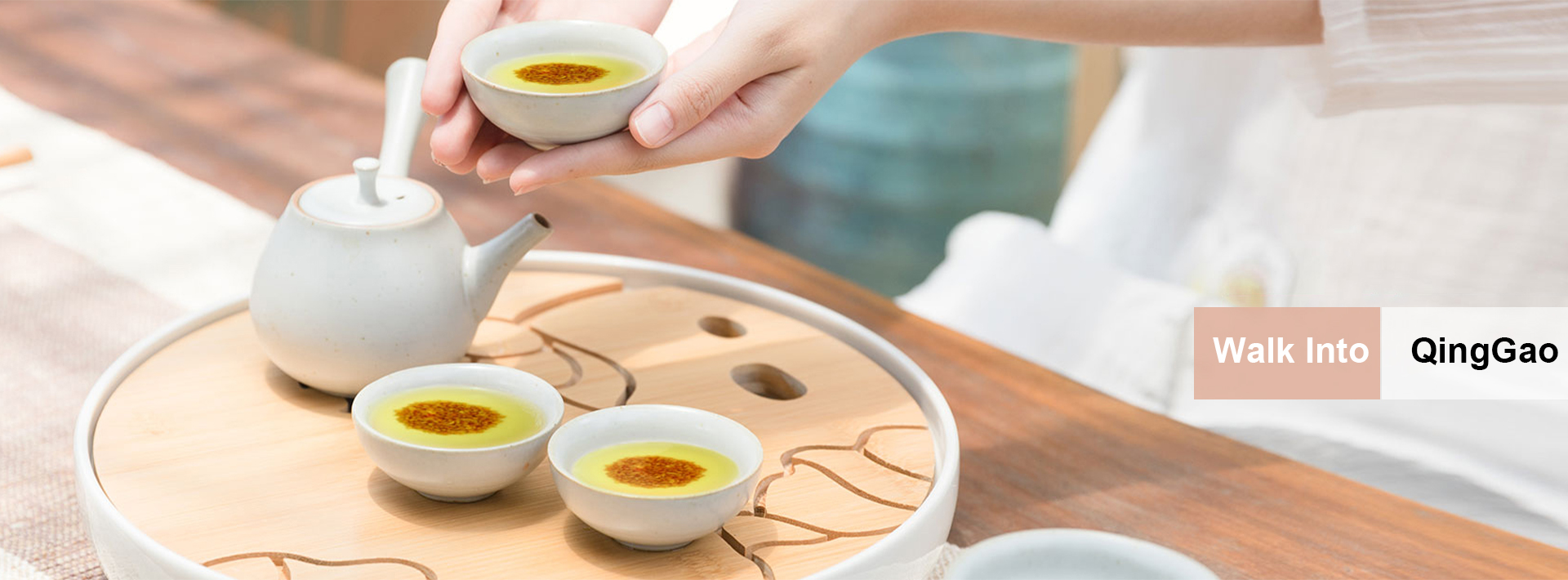
- Cost Efficiency Though the initial setup for lost foam casting may be higher compared to sand casting, the overall cost-effective nature of the method results from reduced wasted materials and shorter lead times.
- Versatility Lost foam casting can be applied to a wide variety of metals, including aluminum, iron, and steel, which expands its applicability across different industries
.Applications of Lost Foam Castings
The versatility of lost foam casting means it can be used in several industries
- Automotive Industry Lost foam casting is frequently used to manufacture engine components, brackets, and transmission cases. The ability to create lightweight parts with complex geometries is particularly beneficial in automotive applications.
- Aerospace Sector In aerospace, lost foam casting's precision is paramount. It is used to create critical components that require high strength-to-weight ratios and exceptional surface finishes.
- Marine Applications Components for boats and ships, such as engine mounts and propellers, can be efficiently produced using lost foam casting, ensuring longevity and durability in harsh environments.
- Industrial Equipment Manufacturing Machinery parts and fixtures benefit from the method's ability to produce durable and precise components with minimal waste.
The Future of Lost Foam Casting
As industries continue to seek methods that improve efficiency and reduce environmental impact, lost foam casting is poised for growth. Advancements in materials science, including the development of new types of foams and binders, could enhance the process even further. Additionally, integrating digital technologies such as 3D printing for creating foam patterns may streamline manufacturing processes and increase design possibilities.
In conclusion, lost foam castings represent a significant advancement in the field of metal casting. With its ability to create complex shapes, reduce waste, and produce high-quality components, this method is becoming increasingly popular across various industries. As technology continues to evolve, the potential for lost foam casting to revolutionize manufacturing practices will only grow, making it an essential technique for the future.
Post time:dets. . 19, 2024 06:03
Next:sand casting foundries