Iron Sand Casting An Overview of the Process and Its Applications
Iron sand casting is a versatile and highly effective method of producing metal parts, utilizing iron-rich sand as the primary raw material. This process is a crucial component of metallurgical engineering and has applications in various industries. In this article, we will explore the fundamentals of iron sand casting, its advantages, and its applications.
The Basics of Iron Sand Casting
Iron sand casting involves the creation of metal parts by pouring molten iron into molds made from sand that contains high concentrations of iron oxide. This method is particularly advantageous because it utilizes locally-sourced materials that are both abundant and cost-effective. The casting process typically includes several steps pattern making, mold preparation, melting the iron, pouring the molten metal, and finishing the cast part.
1. Pattern Making The first step in the casting process involves creating a pattern of the desired metal part. This pattern can be made from various materials, including wood, metal, or plastic. The accuracy of the pattern is crucial, as it directly influences the dimensional tolerance of the final product.
2. Mold Preparation Once the pattern is ready, it is used to create a mold from iron sand mixed with a binder, which helps to hold the mold shape. The mixture is packed around the pattern, and once set, the pattern is removed, leaving a cavity that defines the shape of the final product.
3. Melting the Iron Next, the iron is melted in a furnace. The melting process is meticulously controlled to achieve the desired temperature and ensure the metal is in a liquid state for pouring. Iron sand casting typically uses pig iron or scrap iron, which are melted together in the furnace.
4. Pouring the Molten Iron The molten iron is carefully poured into the mold cavity. This step requires precision to avoid defects such as air pockets or inclusions, which could compromise the integrity of the final product.
5. Finishing the Cast Part Once the iron has cooled and solidified, the mold is broken open to reveal the cast part. This part may require additional finishing processes, such as grinding, machining, or surface treatment, to meet specific design specifications.
Advantages of Iron Sand Casting
Iron sand casting offers numerous advantages that make it a preferred method in the manufacturing of metal components
iron sand casting
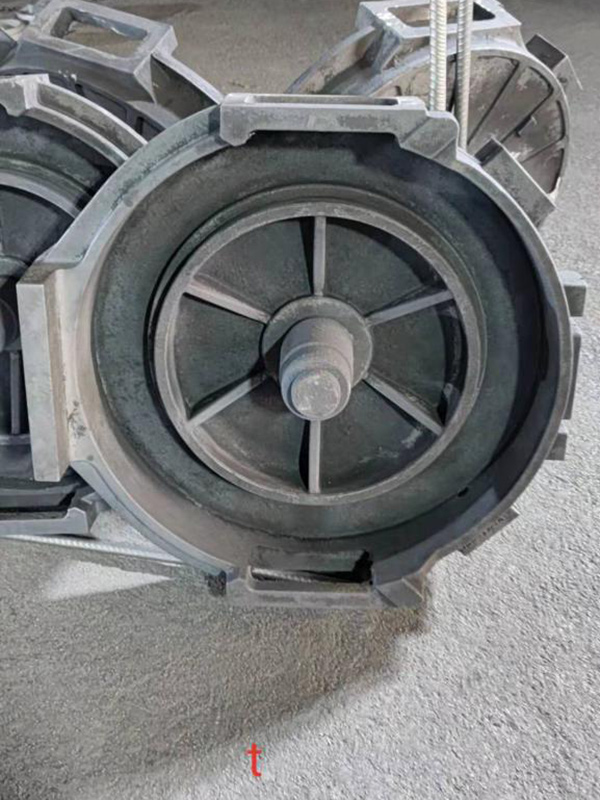
- Cost-Effectiveness The use of iron sand, which is relatively inexpensive and widely available, reduces material costs. Furthermore, the ability to recycle scrap metal enhances economic efficiency.
- Flexibility This casting method can accommodate a wide variety of part sizes and shapes, making it suitable for numerous applications across different industries, from automotive to construction.
- Durability Iron castings are known for their strength and resilience, which makes them ideal for components subjected to significant stress and wear.
- Short Lead Times The overall process allows for quick turnaround times from design to production, facilitating rapid prototyping and meeting urgent manufacturing needs.
Applications of Iron Sand Casting
Iron sand casting is utilized in a diverse array of industries, reflecting its versatility. Some common applications include
- Automotive Components Many parts in vehicles, including engine blocks, transmission cases, and brake components, are produced through iron sand casting due to the method's ability to create complex geometries with high precision.
- Construction Materials Structural components, such as beams and columns, are often cast in iron sand due to their durability and strength.
- Machinery Parts Heavy machinery relies on robust iron castings for gears, housings, and other critical components that must withstand heavy loads.
- Pipe Fittings and Valves The oil and gas, as well as water management industries, frequently use iron sand casting for producing pipe fittings and valves, where reliability and strength are paramount.
In conclusion, iron sand casting is an essential method in modern manufacturing that showcases the ability to efficiently produce high-quality iron components. Its cost-effectiveness, flexibility, and durability make it a preferred choice across various industries, ensuring that it remains a fundamental process in metallurgical engineering.
Post time:okt. . 12, 2024 01:18
Next:Exploring the Benefits and Techniques of Coated Sand Casting in Manufacturing