The Significance of Ceramsite Foundry Sand in Modern Manufacturing
In the realm of modern manufacturing, the quest for advanced materials that enhance efficiency and product quality is ever-present. One such innovative material that has garnered attention is ceramsite foundry sand. This specialized type of sand, created through the firing of clay or other aluminosilicate materials, offers a unique combination of properties that make it an essential component in the metal casting process.
What is Ceramsite Foundry Sand?
Ceramsite foundry sand is a lightweight, spherical grain material known for its excellent thermal stability, low moisture absorption, and high strength. It is made from the calcination of clay at high temperatures, resulting in a durable and chemically inert product. Its structure allows for better flow characteristics compared to conventional foundry sands, thus making it easier to work with during the casting process.
Advantages of Ceramsite Foundry Sand
1. Reduced Defects One of the most notable benefits of using ceramsite foundry sand is its ability to reduce casting defects. Its uniform particle size and shape facilitate better mold filling and reduce the likelihood of air entrapment. Consequently, manufacturers often report fewer defects such as shrinkage and gas porosity, leading to higher quality castings.
2. Enhanced Surface Finish The spherical nature of ceramsite grains contributes to a smoother surface finish on castings. This is particularly important for applications where aesthetics and surface integrity are critical, such as in automotive or aerospace components. The improved finish also reduces the need for extensive post-processing, saving time and costs.
ceramsite foundry sand
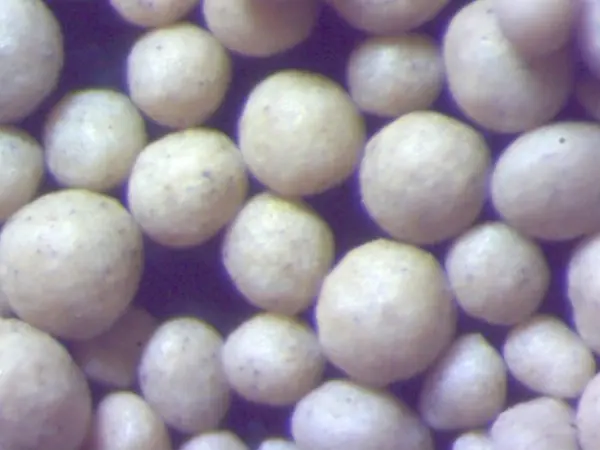
3. Thermal Properties Ceramsite foundry sand displays exceptional thermal resistance, allowing it to withstand the extreme temperatures of molten metals. This property is crucial for maintaining mold integrity and ensuring dimensional accuracy during the casting process. Additionally, the low thermal conductivity of ceramsite helps in reducing heat loss, contributing to overall energy efficiency.
4. Recyclability In response to growing environmental concerns, the recyclability of ceramsite sand is a significant advantage. After use, it can be reclaimed and reused multiple times, thus reducing waste and the demand for new raw materials. This not only promotes sustainability but also results in cost savings for manufacturers.
5. Lightweight Nature The lightweight characteristics of ceramsite foundry sand make it easier to handle and transport compared to traditional sand options. This can lead to lower shipping costs and easier implementation in foundry operations.
Applications in Various Industries
Ceramsite foundry sand is increasingly being used in various industries, particularly in the production of automotive parts, construction equipment, and machinery. Its unique properties make it suitable for both ferrous and non-ferrous metal casting processes. As industries continue to seek ways to optimize manufacturing processes, ceramsite foundry sand stands out as a versatile and effective solution.
Conclusion
As the manufacturing sector continues to evolve, the need for high-performance materials becomes paramount. Ceramsite foundry sand presents a compelling case with its advantages in quality, efficiency, and sustainability. By integrating ceramsite sand into foundry practices, manufacturers can not only improve their product offerings but also contribute to a more sustainable future in manufacturing. With its growing adoption and proven benefits, ceramsite foundry sand is undoubtedly here to stay as a vital resource in the metal casting industry.
Post time:dets. . 12, 2024 21:56
Next:sand castings supplier