Unlocking New Possibilities 3D Printing in Sand Casting
In recent years, the manufacturing landscape has undergone a monumental transformation thanks to advancements in technology. Among these innovations, the combination of 3D printing and sand casting has emerged as a powerful tool that is reshaping traditional manufacturing processes. This hybrid approach not only streamlines production but also enhances the quality and precision of cast parts, making it an invaluable asset in various industries.
Understanding Sand Casting
Sand casting is one of the oldest and most versatile casting processes used for creating metal parts. It involves creating a mold from a mixture of sand and a bonding agent, after which molten metal is poured in to form a solid object. Traditionally, this process required meticulous manual work, from carving patterns to managing mold-making and pouring. While effective, it often led to longer lead times and higher costs due to the labor-intensive nature of the process.
The Rise of 3D Printing
3D printing, also known as additive manufacturing, has gained significant traction since its inception. This technology allows for the creation of complex geometries by layering materials based on digital models. Compared to traditional subtractive manufacturing, where material is removed to create the final product, 3D printing adds material only where necessary. This approach can drastically reduce waste and result in innovative designs that were previously impossible to achieve.
Combining Forces 3D Printing and Sand Casting
The integration of 3D printing into the sand casting process is revolutionizing both fields. By using 3D printing to create patterns or molds directly, manufacturers can eliminate several steps in the traditional sand casting process. With the ability to produce molds using 3D-printed sand, they can generate highly complex shapes and intricate designs that traditional machining would struggle to replicate.
3d printer sand casting
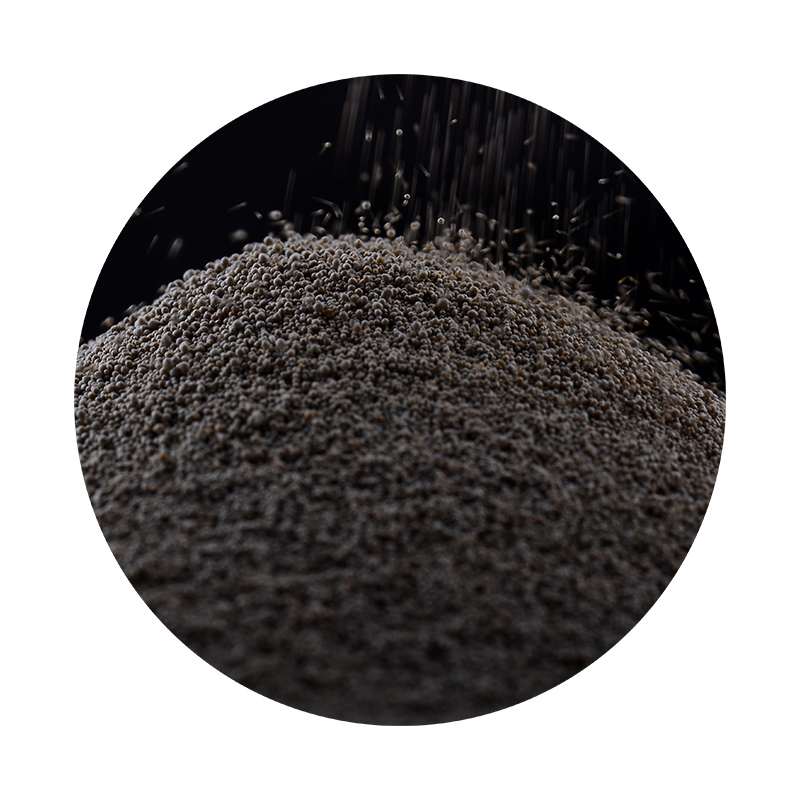
One of the most significant advantages of 3D-printed sand molds is the reduction in lead time. In traditional sand casting, creating a pattern can take days or even weeks depending on the complexity. However, with 3D printing, a mold can be produced in a matter of hours. This rapid prototyping capability is invaluable for industries that require quick turnaround times, such as aerospace or automotive manufacturing.
Enhanced Precision and Complexity
In addition to speed, the precision offered by 3D printing is another critical factor driving its adoption in sand casting. Conventional methods can introduce variability and imperfections in the molds, leading to defects in the final product. In contrast, 3D printing can achieve tighter tolerances and more consistent quality due to its layer-by-layer approach. Manufacturers benefit from reduced scrap rates and improved yield, ultimately enhancing their bottom line.
Moreover, the design freedom provided by 3D printing allows for the creation of complex internal geometries, such as lattice structures or cooling channels, that would be impossible with traditional casting methods. This capability not only improves functionality but also enhances the performance of the final product.
Challenges and Future Outlook
Despite the numerous advantages, the integration of 3D printing with sand casting is not without its challenges. Material limitations, production scale, and initial investment costs can pose obstacles for some manufacturers. However, as technology continues to evolve, these challenges are gradually being addressed. New materials are being developed, and costs are expected to decrease, paving the way for more widespread adoption.
The future of sand casting with 3D printing looks bright. As industries increasingly focus on sustainability and efficiency, this innovative approach will likely play a crucial role in the transition toward greener manufacturing practices. By minimizing waste, reducing energy consumption, and enabling more effective resource utilization, 3D printing in sand casting aligns perfectly with the goals of modern manufacturing.
In conclusion, the synergy between 3D printing and sand casting is a clear indication of how technology can enhance traditional processes. By combining speed, precision, and design freedom, this integration is set to transform the manufacturing landscape, enabling companies to produce high-quality components more efficiently than ever before. As we continue to explore the possibilities, one thing is clear the future of manufacturing is here, and it is driven by innovation.
Post time:dets. . 22, 2024 23:00
Next:metal sand casting