What is Sand Casting in Engineering?
Sand casting is one of the oldest and most widely used metal casting processes in engineering, renowned for its versatility and cost-effectiveness. This method involves creating a mold from a mixture of sand, clay, and water, which is then used to form metal parts by pouring molten metal into the mold cavity. The process has been refined over the years and finds applications in various industries, including automotive, aerospace, and manufacturing.
What is Sand Casting in Engineering?
After the sand mold is prepared, it is split into two halves a cope (top) and a drag (bottom). Once the pattern is removed, the two halves are reassembled, and the casting process can begin. Molten metal, which is heated to the appropriate temperature to achieve a liquid state, is poured into the cavity of the mold. The metal flows around the pattern, filling all voids and capturing the fine details of the design. After the metal cools and solidifies, the mold is broken away to reveal the cast part.
what is sand casting in engineering
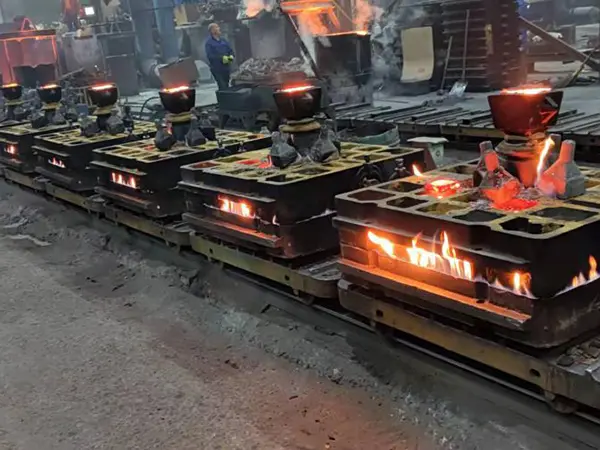
One of the primary advantages of sand casting is its ability to produce complex shapes and large components. Unlike other casting methods, sand casting can accommodate a wide range of sizes and configurations, making it suitable for producing everything from small intricate parts to large industrial components. Moreover, the sand molds can be reused multiple times, although the sand will eventually wear out and require replacement.
However, sand casting is not without its drawbacks. The surface finish of sand-cast parts is generally rougher compared to those produced by other casting methods, which may necessitate secondary machining processes. Furthermore, there can be issues with dimensional accuracy, as the sand mold may not retain its shape perfectly during the pouring and cooling processes.
In summary, sand casting is an essential and widely adopted method in engineering that balances versatility, efficiency, and economic considerations. Its ability to produce complex shapes and accommodate various metal types makes it an enduring choice for manufacturers. While not perfect, the technique continues to be a foundational process in metalworking, symbolizing a blend of traditional craftsmanship and modern engineering practices.
Post time:Ago . 30, 2024 07:54
Next:Hard Sand Casting