Types of Sand in Foundry
The foundry industry relies heavily on the use of various types of sand for metal casting processes. Sand is a vital material that affects the quality and characteristics of the final cast product. Understanding the different types of sand commonly used in foundries is essential for optimizing production and ensuring the desired properties of castings.
Types of Sand in Foundry
2. Green Sand Green sand is a mixture of silica sand, clay, and water, making it suitable for producing molds for casting ferrous and non-ferrous metals. The name green refers to the moisture content rather than the color. Green sand molds are known for their ability to produce intricate shapes and are capable of retaining heat, which is crucial for the casting process. Its reusability is also a significant advantage, making it cost-effective.
types of sand in foundry
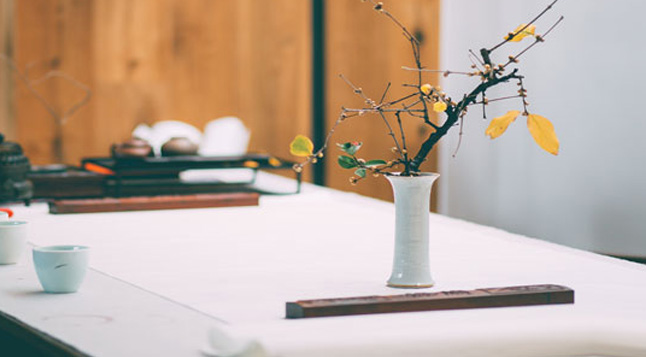
3. Resin Sand Resin sand, or chemically-bonded sand, is created by adding resins to silica sand. This type of sand offers superior strength and dimensional accuracy compared to green sand. The resin binds the sand grains together, resulting in a strong mold that can withstand the high pressures of molten metal. Resin sand is ideal for producing complex and detailed patterns, making it a popular choice for various industries.
4. Nobake Sand Nobake sand molds are created without the addition of water. Instead, they utilize a chemical binder that hardens when cured. This method allows for quick production of molds and is particularly advantageous for large casting applications, where traditional sand molding might be impractical. Nobake sand provides excellent surface finish and dimensional stability.
5. Specialty Sands In addition to the common types, foundries may also use specialty sands, such as zircon sand or chromite sand, which offer unique properties. Zircon sand is known for its high thermal stability and low expansion rate, making it suitable for precision castings. Chromite sand, on the other hand, possesses excellent resistance to thermal shock and is often used in steel casting applications.
In conclusion, the selection of sand type significantly influences the casting process and the quality of the final product. Each type of sand has its own set of advantages, and foundries often choose based on specific requirements of the casting work. An understanding of these different sands enables foundries to optimize their operations and produce high-quality castings efficiently.
Post time:sep . 22, 2024 19:16
Next:what materials are used for sand casting