Understanding Sand Casting Tolerances
Sand casting is one of the oldest and most versatile metal casting processes used in manufacturing today. It involves creating a mold from a mixture of sand, clay, and water, and then pouring molten metal into the mold to form a desired shape. One critical aspect of sand casting that significantly influences the quality of the final product is the tolerances associated with the process. This article explores what sand casting tolerances are, their importance, and how they can be achieved effectively in cast metal products.
What are Sand Casting Tolerances?
Tolerances in sand casting refer to the allowable variations in dimensions and quality of the cast parts. These specifications dictate how much a finished piece can differ from its intended design dimensions without compromising functionality. Typically, tolerances are expressed in terms of linear dimensions (like length, width, and height), angular dimensions, and surface finish.
The tolerances allowed in sand casting can vary depending on factors like the type of metal used, mold fabrication methods, and the overall design specifications of the component being cast. Generally, sand casting tolerances can range from ±0.5 mm for small components to ±2.5 mm for larger pieces.
Importance of Sand Casting Tolerances
1. Functionality and Fit Precise tolerances are crucial for ensuring that moving parts fit together correctly. For example, in automotive applications, engine components must have tight tolerances to function effectively and avoid mechanical failures.
2. Cost Efficiency Adhering to tolerances prevents the need for costly rework and reduces waste. If a cast part does not meet the required tolerances, it may need to be scrapped or re-manufactured, leading to significant financial losses.
3. Quality Assurance Established tolerances help maintain consistent product quality. By having predefined limits, manufacturers can ensure that each batch of cast components meets quality standards, leading to improved customer satisfaction and reduced returns.
sand casting tolerances
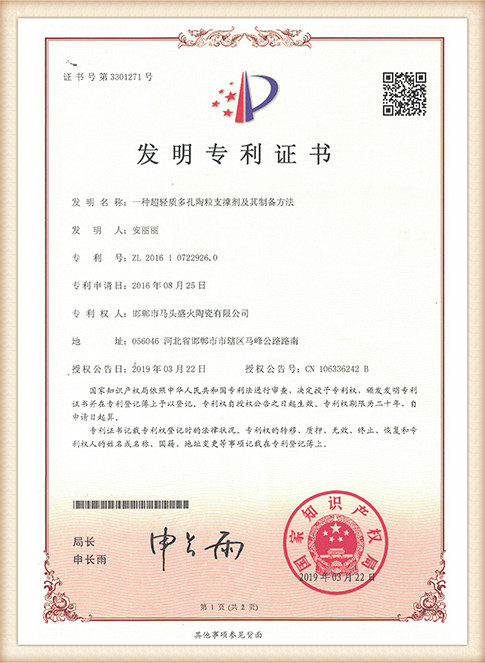
Achieving Tolerances in Sand Casting
Several factors influence the capability to achieve desired tolerances in sand casting
1. Mold Preparation The quality of the mold impacts the accuracy of cast parts. Ensuring that the mold is properly designed and manufactured with minimal imperfections will contribute significantly to achieving tighter tolerances.
2. Material Selection Different metals have varying shrinkage rates and cooling characteristics. Selecting the right material that behaves predictably during solidification can help in minimizing dimensional variations.
3. Casting Parameters Control over the pouring temperature, filling rate, and cooling rate of the molten metal is vital. These parameters should be closely monitored to ensure uniformity, as variations can lead to defects and tolerance deviations.
4. Post-Casting Processes Finishing processes such as machining, grinding, or surface treatment can help bring cast components within tight tolerances. If the casting process cannot achieve desired specifications, these secondary operations can correct dimensional inaccuracies.
5. Inspection and Quality Control Implementing robust inspection and quality control measures is essential for maintaining tolerances. Techniques like coordinate measuring machines (CMM) and laser scanning can be employed to measure parts accurately and ensure they conform to specifications.
Conclusion
Sand casting is a valuable manufacturing process that, when used effectively, can produce high-quality parts with precise tolerances. Understanding the significance of tolerances and how to achieve them is essential for manufacturers looking to compete in today’s fast-paced industrial environment. By focusing on mold preparation, material selection, control of casting parameters, and post-casting treatments, the industry can enhance the overall quality and functionality of cast products. This proactive approach to managing tolerances not only boosts efficiency but also paves the way for innovation and excellence in metal casting.
Post time:nov . 12, 2024 10:25
Next:sanding a 3d print