Understanding the Sand Casting Foundry Process
Sand casting, also known as sand mold casting, is a versatile and widely-used manufacturing process that involves creating metal parts from molten metal. This technique is favored for its ability to produce complex shapes with high precision and is particularly popular in the foundry industry. Let's explore the sand casting foundry process in detail.
The first step in the sand casting process is the preparation of the pattern. A pattern is a replica of the part to be cast, usually made from metal, wood, or plastic. It is created with a bit of extra size to account for the shrinkage of metal as it cools and hardens. This pattern will form the mold cavity in which the molten metal will be poured.
Once the pattern is ready, the next stage involves preparing the sand mixture. The sand used in casting is typically a combination of silica sand, a bonding agent (such as clay), and water. The proportions of these components can vary depending on the specific requirements of the casting. The sand is carefully mixed to ensure consistency and the right level of moisture, which helps it retain shape when compacted.
The mold is created by compacting the sand mixture around the pattern. This is done in two halves the top half (cope) and the bottom half (drag). The pattern is placed in a molding box, and sand is packed around it. The molding sand must be tightly compressed to ensure that it can withstand the pressure of the molten metal during pouring. After the sand has been compacted, the pattern is removed, leaving behind a cavity that mirrors the shape of the intended part.
sand casting foundry process
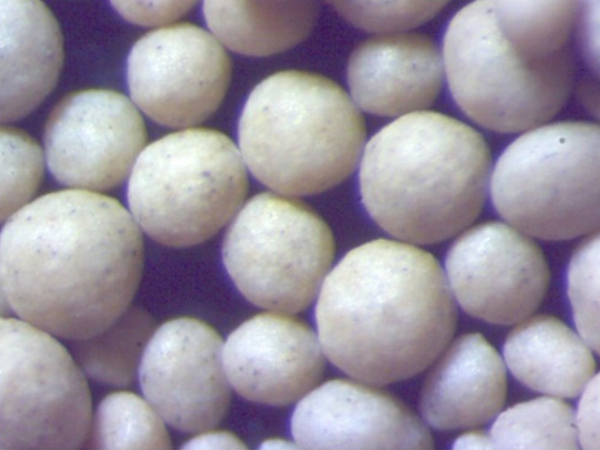
At this point, the next step involves adding the necessary gating system, which includes channels through which the molten metal will flow into the mold. These gates are crucial for ensuring that the cavity is completely filled without any air pockets or defects. Once the gating system is established, the mold halves are reassembled, and the mold is ready for pouring.
The molten metal, which can be made from a variety of materials such as aluminum, iron, or bronze, is then heated until it achieves a liquid state. The temperature and composition of the metal are carefully controlled to ensure optimal characteristics in the final cast. Once ready, the molten metal is poured into the mold through the gates, filling the cavity and taking the shape of the pattern.
After the metal cools and solidifies, the mold is broken apart to reveal the cast part. This process may involve manual or mechanical methods to remove the sand, which can be reused for future castings. Finally, the cast part may undergo further finishing processes such as sanding, machining, or surface treatment to achieve the desired specifications and surface quality.
In conclusion, the sand casting foundry process is an efficient and effective way to produce complex metal parts. Its adaptability and scalability make it suitable for both small-scale and large-scale production. Understanding each step, from pattern creation to final finishing, is essential for manufacturers seeking to leverage the full potential of sand casting in their operations.
Post time:nov . 20, 2024 03:25
Next:low volume sand casting