Understanding Sand Casting A Versatile Foundry Process
Sand casting, also known as sand mold casting, is one of the oldest and most widely used metal casting processes in the foundry industry. This method involves creating a mold from sand to produce metal parts, and it can accommodate a wide range of materials, including aluminum, brass, bronze, cast iron, and steel. The versatility and cost-effectiveness of sand casting make it an attractive option for both small-scale operations and large manufacturing facilities.
The Process of Sand Casting
The sand casting process begins with the creation of a pattern, which is a replica of the final product that needs to be cast. Patterns can be made from various materials, including metal, wood, or plastic, and they can be single-piece or multipart, depending on the complexity of the component.
Once the pattern is ready, a molding material—usually a mixture of sand, clay, and water—is formed around it to create a mold. This mixture is packed around the pattern to ensure it holds its shape. After the mold is prepared, the pattern is removed, leaving a cavity in the shape of the desired part.
The next step involves pouring molten metal into the mold cavity. The metal is heated to a liquid state, typically at a temperature range appropriate for the specific material being used. Once the metal is poured in, it fills the cavity and takes its shape. The molten metal is then allowed to cool and solidify, which may take several minutes to hours, depending on the size and material of the part. After the metal has cooled, the sand mold is broken away to reveal the cast part, which may require additional finishing processes such as grinding or machining.
Advantages of Sand Casting
One of the primary advantages of sand casting is its ability to produce large parts at a relatively low cost. The materials used for sand molds are generally inexpensive and can be reused multiple times. This makes sand casting an economical choice for production runs of all sizes, from prototypes to larger series.
sand casting description
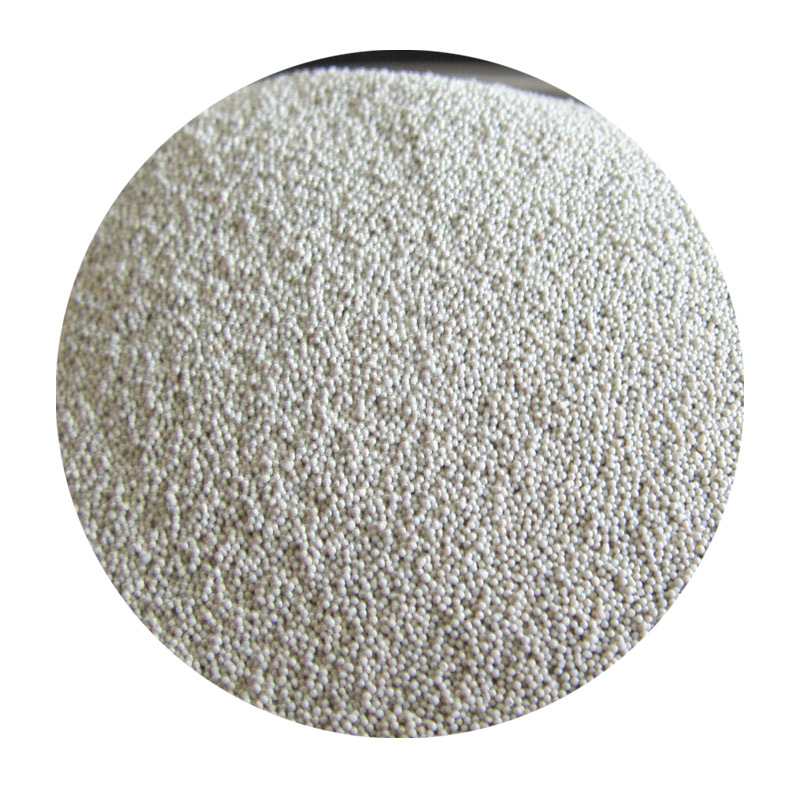
Another benefit is the flexibility in design. Sand casting can accommodate complex shapes and intricate details that might be challenging to achieve with other casting methods. Additionally, the process allows for the easy incorporation of various alloys, enabling manufacturers to tailor the mechanical properties of the final product to specific applications.
Moreover, sand casting is compatible with a wide range of metals, which broadens its application across different industries, including automotive, aerospace, construction, and artistic sectors
.Limitations of Sand Casting
Despite its many advantages, sand casting does have some limitations. The surface finish of sand-cast parts is typically rough and may require additional processing to achieve a desired finish. Additionally, the dimensional accuracy of sand casting might not meet the stringent tolerances required for certain applications, which could lead to further machining or adjustments.
Furthermore, while sand casting is economical for larger quantities, it may not be the best choice for very high-volume production runs due to the time required for mold creation and the inherent limitations in cycle time compared to other methods like die casting.
Conclusion
Sand casting remains a pivotal manufacturing technique in the metalworking industry, primarily due to its cost-effectiveness and flexibility in producing complex shapes. While challenges exist regarding surface finish and dimensional accuracy, the benefits often outweigh these concerns for many applications. As technology advances, the sand casting process continues to evolve, incorporating modern techniques and materials that enhance its capabilities and efficiencies. This enduring process is likely to remain a cornerstone of metal casting well into the future, illustrating the importance of tradition and innovation in manufacturing practices.
Post time:okt . 19, 2024 15:57
Next:တံဆိပ်အရုပ်ထိုးနည်းလမ်းများနှင့် လုပ်ငန်းဆောင်နည်းများ