Parts of Sand Casting
Sand casting, a widely utilized manufacturing process, involves pouring molten metal into a mold made of sand to create a desired shape. It is noted for its versatility and cost-effectiveness, making it a preferred option in various industries from automotive to aerospace. To understand sand casting better, it is essential to analyze its key components, processes, and materials involved.
1. Molding Sand The Foundation of Sand Casting
The heart of the sand casting process is the molding sand. This type of sand is specifically formulated for its unique properties which allow it to withstand high temperatures and retain shape when moistened. The main ingredients typically include silica sand, clay, and water.
- Silica Sand The primary component, silica sand provides strength and helps in mold formation. The grain size and shape of the particles can significantly impact the final product's surface finish and dimensional accuracy. - Clay Usually bentonite clay, it acts as a binder, improving the mold's cohesiveness and giving it structural integrity. The amount of clay used can modify the mold's rigidity. - Water Water is added to activate the clay and assists in achieving the desired consistency for the sand mixture. However, too much water can weaken the mold and cause defects.
2. Pattern Creating the Mold Shape
A pattern is a replica of the final product and is used to create the mold cavity. It can be made from various materials, including wood, metal, or plastic. The pattern needs to be slightly larger than the part itself to account for shrinkage, which occurs as the metal cools. Patterns can be simple one-piece designs or complex multi-part patterns, depending on the intricacy of the final product. The design of the pattern influences the ease of mold assembly and the quality of the cast part.
3. Mold Forming the Cast Structure
Once the pattern is created, it is used to form the mold. This involves packing the molding sand around the pattern to create a cavity that will define the shape of the finished part. After the sand is compacted, the pattern is removed, leaving behind a negative impression. The mold is then carefully assembled, often requiring multiple halves that fit together to ensure a complete cavity.
parts of sand casting
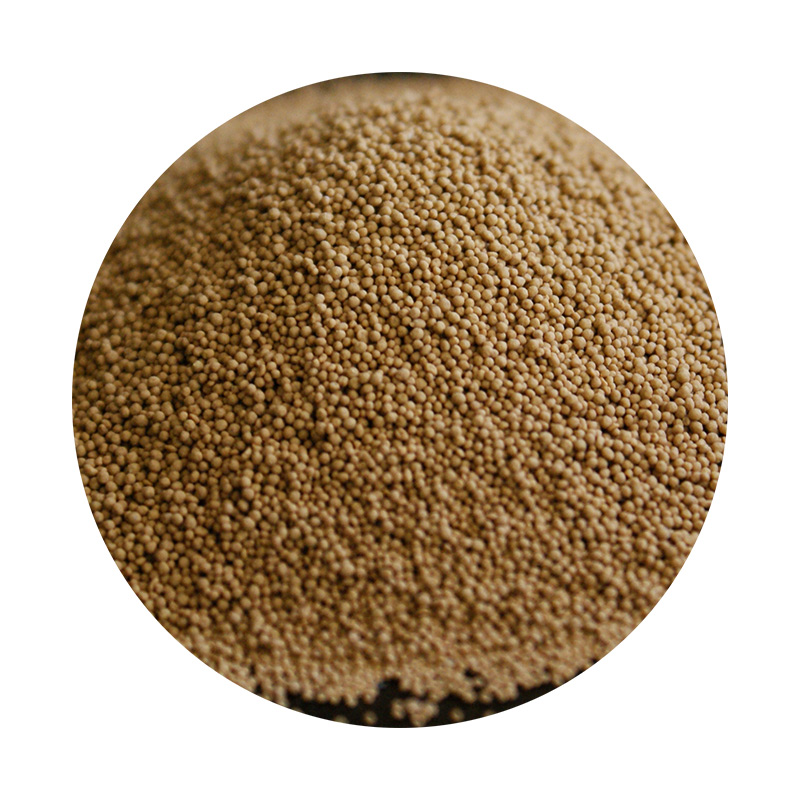
The mold can also be equipped with cores, which are internal parts that define hollow sections of the casting. Cores are typically made of sand mixed with a binder and are placed within the mold before pouring the molten metal.
4. Pouring Filling the Mold with Metal
The next step is the pouring process, where molten metal is carefully introduced into the mold cavity. Proper temperature control is critical during this stage to prevent defects like cold shuts or porosity. The pouring rate must also be controlled to avoid turbulence, which can introduce air bubbles into the casting.
Different types of metals can be used in sand casting, including iron, aluminum, and copper alloys. The choice of metal will depend on the desired mechanical properties, thermal characteristics, and application of the cast part.
5. Cooling and Finishing the Cast
Once the metal has filled the mold, it is allowed to cool and solidify. Cooling time varies depending on the thickness and size of the casting. After solidification, the mold is broken open to retrieve the cast part.
However, the casting often requires further finishing to achieve the desired final specifications. This may include removing excess material (known as flash), machining for dimensional accuracy, and surface treatment to enhance appearance and resistance to corrosion.
Conclusion
In conclusion, understanding the parts of sand casting provides insight into its effectiveness as a manufacturing process. From the formulation of molding sand to the intricacies of pattern design and the careful pouring of molten metal, each component plays a crucial role in determining the quality and functionality of the final product. Sand casting continues to be a vital process in modern manufacturing, proving its adaptability and efficiency across various applications.
Post time:nov . 25, 2024 05:41
Next:Simple Sands Ceramics for Elegant Home Decor and Unique Artistry