Lost Foam Casting Method A Comprehensive Overview
Lost foam casting (LFC) is a sophisticated metal casting process that offers unique benefits over traditional casting methods. By eliminating the need for a rigid mold, LFC allows for greater design flexibility, improved surface finish, and reduced production costs. This article seeks to explore the mechanics and applications of the lost foam casting method, elucidating why it has become a preferred choice in various industries.
What is Lost Foam Casting?
Lost foam casting is a process that uses a foam pattern to create a mold for metal casting. The process begins with the creation of a polystyrene or polyurethane foam pattern that reflects the dimensions of the desired final product. This pattern is then coated with a ceramic shell or a sand mixture to create a mold. Once the mold is formed, the foam is vaporized when molten metal is poured into it, leaving a cavity that takes the shape of the foam pattern. This is the essence of the lost aspect of the method—the foam pattern is lost in the casting process.
The Process
The lost foam casting process can be broken down into several steps
1. Pattern Creation The first step involves crafting a foam pattern, which can be shaped easily using techniques such as CNC machining or hot-wire cutting.
2. Mold Coating After the pattern is created, it is coated with a fine sand mixture bound by a thermosetting resin. This coating forms a shell around the foam pattern, ensuring that the final product has a high-quality surface finish.
3. Drying The coated pattern is then dried to harden the shell.
4. Pouring The final step involves pouring molten metal into the shell. As the metal fills the cavity, the foam vaporizes, allowing the metal to take on the exact shape of the pattern.
5. Cooling and Finishing Once cooled, the shell is broken away to reveal the newly cast object. Any excess material can be machined or finished according to specifications.
lost foam casting method
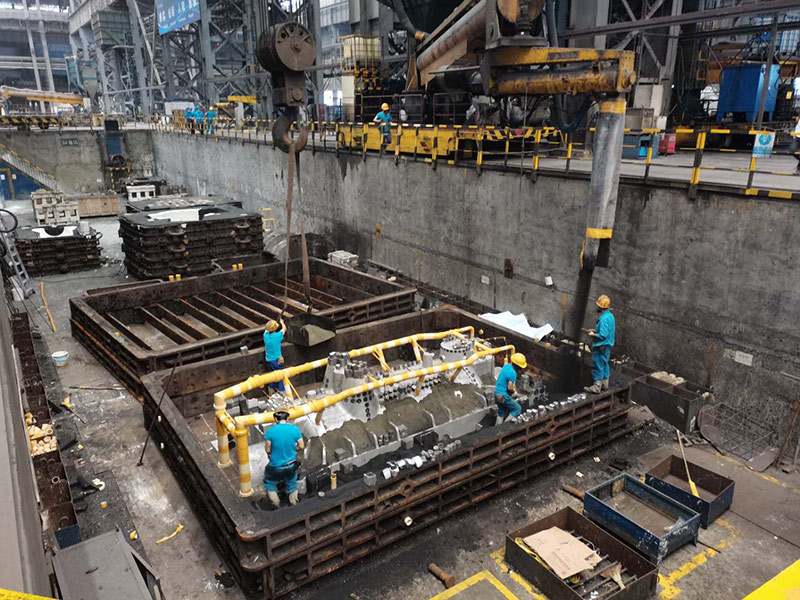
Advantages of Lost Foam Casting
Lost foam casting boasts numerous advantages that make it a favorable option for manufacturers
- Complex Geometries LFC allows for the creation of intricate shapes that would be difficult or impossible to achieve with traditional casting methods. This is particularly beneficial in industries that demand high design complexity, such as automotive and aerospace.
- Reduced Material Waste Since the foam pattern is vaporized, there is minimal material waste in the process. Additionally, the ability to mold complex shapes eliminates the need for additional machining, further conserving resources.
- Improved Surface Finish The lost foam casting method typically produces parts with superior surface finishes right out of the mold, reducing the need for extensive post-processing.
- Cost-Effectiveness LFC is often more economical for small to medium-sized production runs. The reduced need for tooling and the rapid mold creation process contribute to lower overall production costs.
Applications
Lost foam casting finds applications across various sectors. The automotive industry utilizes this method for producing engine blocks, cylinder heads, and various components, benefiting from the precision and reduced weight of the castings. Aerospace components, often requiring intricate designs and tight tolerances, are also suited for LFC. Additionally, the method is being increasingly adopted for producing art sculptures and decorative items, showcasing its versatility.
Conclusion
In summary, the lost foam casting method represents a transformative approach to metal casting that excels in design flexibility, efficiency, and cost-effectiveness. Its ability to produce complex geometries with exceptional surface finishes makes it a valuable asset across numerous industries. As technology continues to evolve, the lost foam casting method is poised to play an even more significant role in the future of manufacturing.
Post time:dec . 05, 2024 10:30
Next:foundry sand density