Foundry Casting Sand The Backbone of Metal Casting
Foundry casting sand is an essential component in the metal casting industry, playing a crucial role in the creation of metal parts through the process of sand casting. This technique is one of the oldest and most versatile methods for shaping metals and has been used for thousands of years. In this article, we explore the properties, types, applications, and significance of foundry casting sand in modern manufacturing.
What is Foundry Casting Sand?
At its core, foundry casting sand is a mixture mainly composed of silica sand, along with other binding materials and additives. This mixture forms the mold that shapes molten metal into desired configurations during the casting process. The properties of the sand, including grain size, shape, and chemical composition, significantly impact the quality of the final cast product.
Types of Foundry Casting Sands
1. Silica Sand The most common type used in the foundry industry, silica sand consists primarily of silicon dioxide (SiO2). Its excellent thermal stability and ability to withstand high temperatures make it ideal for creating molds.
2. Resin Sand This type of sand is coated with a resin binder, which enhances its strength and allows for more intricate mold designs. Resin sands cure rapidly and provide superior surface finishes on castings.
3. Clay Sand Typically made by mixing silica sand with clay, this traditional casting sand retains moisture and adds plasticity to the mold, allowing for greater flexibility during production.
4. Zircon Sand Zircon sand is known for its high melting point and low thermal expansion, making it suitable for applications requiring high precision and durability.
5. Chromite Sand With good thermal properties and resistance to metal penetration, chromite sand is often used for casting ferrous metals. It also reduces the risk of casting defects.
Applications of Foundry Casting Sand
Foundry casting sand is used in various industries, including automotive, aerospace, and general manufacturing. Some of the key applications include
foundry casting sand
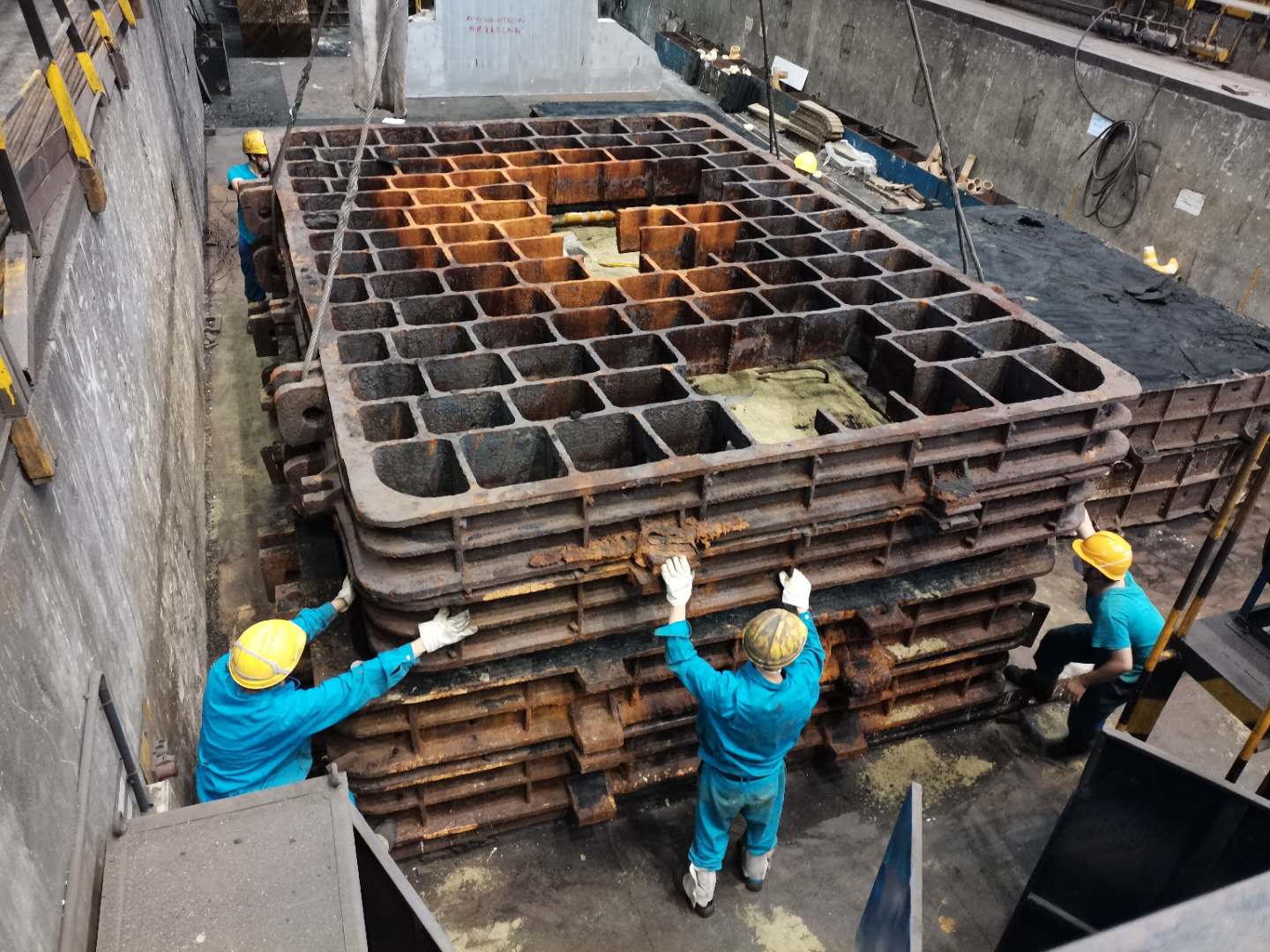
- Automotive Components Many vehicle parts, such as engine blocks, transmission cases, and gears, are created using sand casting methods. The versatility and cost-effectiveness of sand casting allow for complex geometries that meet stringent performance requirements.
- Aerospace Parts The aerospace industry often demands high-precision components that can withstand extreme conditions. Foundry casting sand enables manufacturers to produce lightweight yet strong parts necessary for aircraft performance.
- Artistic Castings Sand casting is also a popular method for creating artistic and decorative metal objects, such as sculptures and architectural elements. The intricate details achievable with fine molds allow for vibrant and aesthetically pleasing results.
Advantages of Using Foundry Casting Sand
The use of sand in casting offers several advantages
- Cost-Effectiveness Sand casting is one of the most economical methods of metal forming, as it requires relatively low initial investment and provides high efficiency in production.
- Flexibility Molds made from casting sand can be easily modified for various designs and sizes, accommodating both small-scale and large-scale production runs.
- High Tolerance for Heat Foundry casting sand can withstand high temperatures, making it suitable for molten metals, reducing the risk of mold degradation.
- Reusability Used sand can often be reclaimed and prepared for reuse, contributing to sustainability in manufacturing processes.
Conclusion
In summary, foundry casting sand embodies the fusion of art and engineering in metal casting, paving the way for the production of intricate designs and durable components across various industries. Its diverse types and inherent qualities make it a vital resource in the foundry sector, continuously evolving with advancements in technology. As industries progress towards more innovative solutions, the significance of casting sand remains steadfast, highlighting its role as the backbone of metal casting practices worldwide. This age-old material continues to prove indispensable, ensuring that both traditional craftsmanship and modern manufacturing thrive side by side.
Post time:nov . 14, 2024 11:40
Next:resin bound sand