Advantages of Lost Foam Casting
Lost foam casting is a revolutionary method in the field of metal casting that offers several advantages over traditional casting techniques. This innovative process involves creating a foam pattern which is then coated with a refractory material and placed in a sand mold. Once molten metal is poured into the mold, the foam pattern vaporizes, leaving behind the desired shape. Here are several key advantages of lost foam casting that make it an attractive option for manufacturers.
1. High Precision and Detail One of the primary benefits of lost foam casting is its ability to produce highly detailed and precise parts. The foam patterns can be manufactured to extremely tight tolerances, allowing for the production of complex geometries that may be difficult or impossible to achieve with traditional methods. This level of precision is especially advantageous in industries such as aerospace and automotive, where component accuracy is critical for performance and safety.
Advantages of Lost Foam Casting
3. Simplified Machining The smooth surface finish achieved through the lost foam casting process often requires minimal post-casting machining. This reduction in machining requirements can lead to lower production costs and shorter lead times, allowing manufacturers to bring products to market more quickly. By decreasing the need for secondary operations, companies can streamline their production processes and enhance overall efficiency.
advantages of lost foam casting
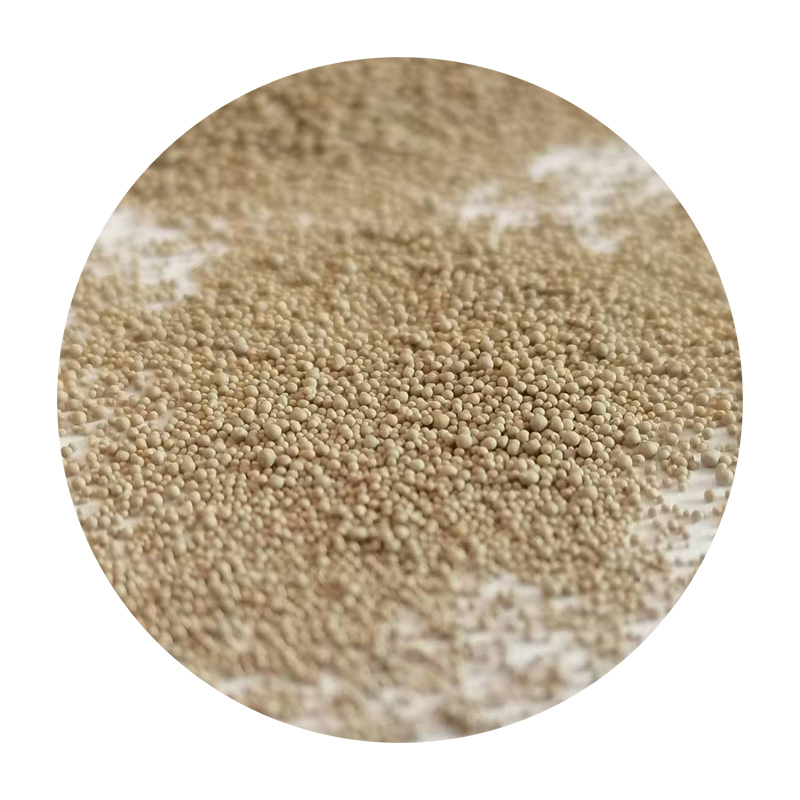
4. Versatility in Materials Lost foam casting can be used with a wide range of metals, including aluminum, iron, and bronze, giving manufacturers the flexibility to choose materials that best suit their application needs. This versatility makes it an attractive option for producing a variety of components, from intricate decorative pieces to heavy-duty industrial parts.
5. Environmental Benefits The lost foam casting process is generally more environmentally friendly than traditional casting methods. The reduction in waste generation and the ability to use recyclable materials for foam patterns contribute to a greener manufacturing process. Additionally, the use of a chemical-free sand mold reduces the environmental impact associated with other casting materials.
6. Cost-Effective Production Although the initial setup for lost foam casting may require an investment in equipment and materials, the long-term benefits often outweigh these initial costs. The combination of reduced waste, lower machining needs, and shorter production times results in considerable cost savings for manufacturers.
In conclusion, lost foam casting offers numerous advantages that make it an appealing choice for modern manufacturing. With its ability to produce high-precision, low-waste components in a variety of materials, this process stands out as a forward-thinking solution in the ever-evolving landscape of metal casting technologies. As industries continue to seek more efficient and sustainable production methods, lost foam casting is likely to gain even more prominence in the coming years.
Post time:sep . 22, 2024 13:12
Next:spherical sand