The Advantages of Sand Casting
Sand casting, also known as sand mold casting, is one of the oldest and most versatile metal casting processes. This technique involves creating a mold from a mixture of sand, clay, and water, into which molten metal is poured to create cast parts. Despite the emergence of advanced techniques, sand casting remains a popular choice for its numerous advantages.
Cost-effectiveness
One of the most significant advantages of sand casting is its cost-effectiveness. The materials used for sand molds are generally inexpensive and readily available. Sand, clay, and water are basic components that can be sourced easily in large quantities. Additionally, the sand can be reused multiple times, which reduces material costs. This aspect makes sand casting particularly attractive for small-scale production and for manufacturers looking to minimize expenses.
Flexibility in Design
Another advantage of sand casting is its exceptional flexibility when it comes to design. Unlike other casting processes that require highly specific molds, sand casting allows for a wide variety of shapes and sizes. Complex geometries, intricate details, and larger components can be produced with relative ease. This flexibility makes sand casting suitable for a broad spectrum of applications, ranging from automotive parts to artistic sculptures.
Scalability
Sand casting is highly scalable, making it an ideal choice for both small and large production runs. Molds can be created for one-off projects as easily as they can for thousands of pieces. As demand grows, manufacturers can adjust their production techniques without a significant overhaul of equipment or processes. This scalability is a considerable advantage for businesses looking to expand or diversify their product lines over time.
Good Tolerance
While sand casting is often regarded as a less precise method compared to other casting techniques, modern advancements have improved its accuracy and tolerance levels significantly. With advancements in mold making and pouring techniques, sand casting can achieve acceptable tolerances, making it suitable for various engineering applications. This aspect is particularly advantageous when tight tolerances are not critical to the part’s function.
advantage of sand casting
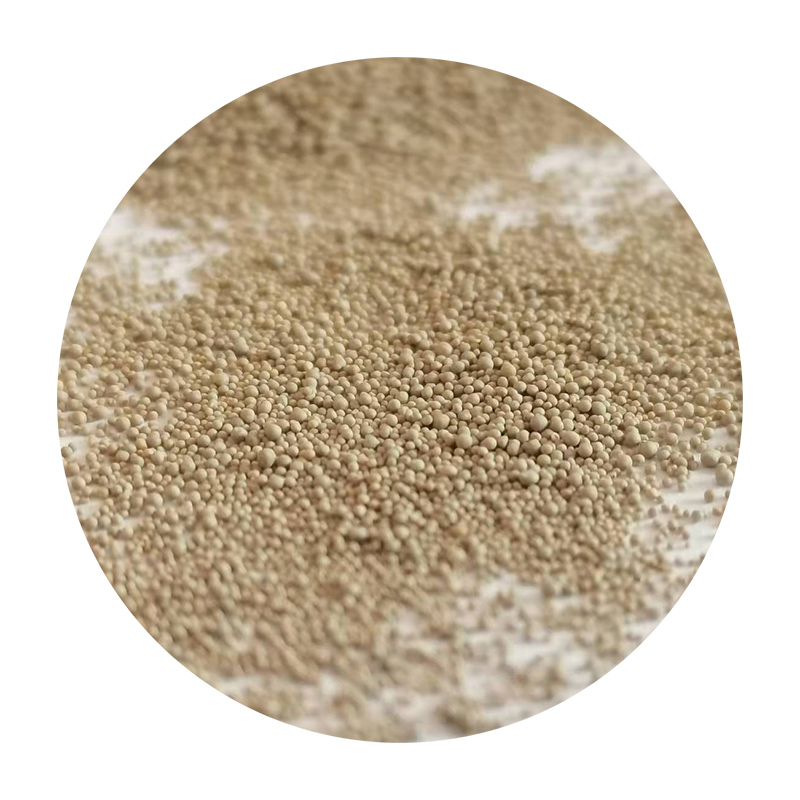
Suitable for Various Metals
Sand casting is not limited to a specific type of metal; in fact, a wide range of metals can be cast using this method. Ferrous metals, such as cast iron and steel, as well as non-ferrous metals like aluminum, bronze, and brass, can all be effectively molded using sand casting. This versatility allows manufacturers to choose the most appropriate metal for their specific application without being constrained by the casting process.
Rapid Prototyping
The speed of sand casting also contributes to its advantages. Because molds can be created quickly, manufacturers can produce prototypes in a relatively short amount of time. Rapid prototyping is essential in product development cycles, allowing designers and engineers to test and verify their designs before committing to larger production runs. This quick turnaround time can streamline the development process and facilitate faster bring-to-market strategies.
Minimal Labor Costs
Although some degree of labor is involved in sand casting, especially in creating the molds, the process can be quite automated. Automated molding systems and pouring techniques have significantly reduced the labor-intensive aspects of sand casting. Moreover, the skill level required for certain processes is generally lower than that required for more advanced casting techniques. This results in further savings on labor costs.
Environmentally Friendly
Lastly, sand casting is generally considered to be an environmentally friendly option. The sand used in the process is a natural material that does not produce harmful by-products. Additionally, since most of the sand can be reclaimed and reused for future casting, waste is minimized. Many foundries are also adopting green practices, such as using eco-certified binders and adopting technologies that reduce energy consumption.
Conclusion
In conclusion, the advantages of sand casting make it an enduring choice in the manufacturing industry. Its cost-effectiveness, flexibility, scalability, and suitability for various metals provide significant benefits for a wide range of applications. Moreover, the ability to produce prototypes quickly and its environmentally friendly nature further enhance its attractiveness. As manufacturers continue to innovate and improve the sand casting process, it is likely to remain a staple in the production of metal components for years to come.
Post time:jan . 01, 2025 12:20
Next:ကာရိုနာပစ္စည်းများကို စင်ကြယ်စွာ အဆိပ်အပြား သင့်လျော်စွာ လုပ်ဆောင်ခြင်း