Understanding the Sand Casting Process
Sand casting is one of the oldest and most versatile metal casting processes, widely used in foundries across the globe. This process involves creating a mold from a mixture of sand, clay, and water, into which molten metal is poured to create a variety of metal parts and components. This article aims to explain the sand casting process, its advantages, and its applications.
The Sand Casting Process
The sand casting process begins with the creation of a pattern. A pattern is a replica of the final product, typically made from a material such as wood, metal, or plastic. This pattern is used to form the mold. The process can be broken down into several key steps
1. Mold Creation The pattern is placed in a box called a flask, and fine sand mixed with a binding agent like clay and water is packed around the pattern. Once the sand is compacted, the pattern is removed, leaving a cavity in the shape of the desired part. This cavity forms the mold.
2. Pouring After the mold is prepared, it is typically dried and reinforced. The next step involves heating the metal to its melting point and pouring it into the mold cavity. The molten metal fills the space left by the pattern, taking its shape.
3. Cooling Once the metal has been poured, it is allowed to cool and solidify. Cooling time varies depending on the metal and size of the casting, but it is crucial for ensuring that the final product has the desired properties.
4. Casting Removal After the metal has cooled and solidified, the sand mold is broken away to reveal the cast metal part. This can involve knocking off the sand or using vibrations to shake it loose.
what is sand casting process
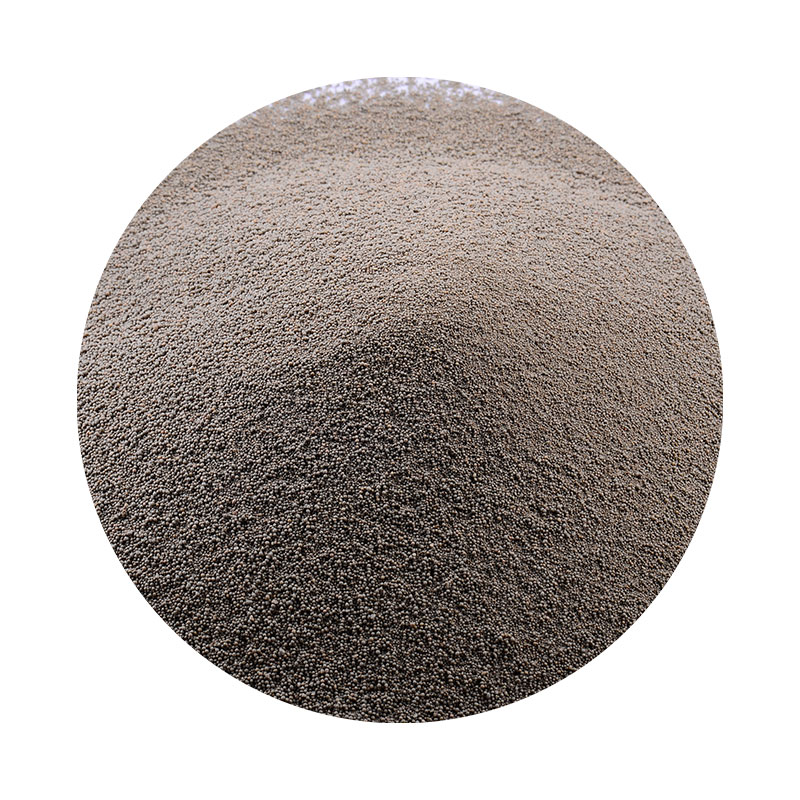
5. Finishing The final step involves cleaning the casting, which may involve removing any remaining sand, grinding off excess material, and performing surface treatments to achieve the desired finish.
Advantages of Sand Casting
Sand casting offers several advantages that make it a popular choice among manufacturers. Firstly, this process is cost-effective, especially for small to medium production runs. The materials (sand, clay, and water) are inexpensive and easily accessible.
Secondly, sand casting is incredibly versatile, allowing for the creation of both simple and complex shapes. Moreover, it accommodates a wide range of metals, including aluminum, copper, and iron.
Lastly, the sand casting process is less resource-intensive compared to other casting methods. The molding sand can be reused several times, making it an environmentally friendly option.
Applications of Sand Casting
Due to its versatility and cost-effectiveness, sand casting is utilized in various industries. It is commonly used for manufacturing automotive components, machinery parts, and various tools. The ability to produce large castings, such as engine blocks and pump housings, further emphasizes its role in heavy industries.
In conclusion, the sand casting process is a foundational technique in metal fabrication, combining tradition with innovation. Its efficiency, versatility, and cost-effectiveness mark it as an enduring choice for manufacturers looking to produce high-quality metal parts.
Post time:Σεπ . 05, 2024 07:23
Next:sand casting tolerances