Steps in Sand Casting
Sand casting is one of the oldest and most widely used metal casting processes. It involves creating a mold from sand and then pouring molten metal into the mold to create parts. This method is popular due to its adaptability and cost-effectiveness, making it suitable for a variety of applications in industries ranging from automotive to aerospace. This article will outline the essential steps involved in the sand casting process.
1. Pattern Making The first step in the sand casting process is creating the pattern, which is a replica of the object to be cast. Patterns are typically made from materials like wood, metal, or plastic, and they need to be slightly larger than the actual part, accounting for the metal's shrinkage as it cools. The pattern is designed to include allowances for machining, draft angles, and any complex features that will aid in molding.
Steps in Sand Casting
3. Molding In this step, the prepared sand is packed around the pattern to form a mold. The pattern is placed in a molding box and covered with sand, which is then compacted to create a solid mold. After compaction, the pattern is removed, leaving a cavity in the shape of the desired part. This process can involve single-part or two-part molds, depending on the complexity of the design.
steps in sand casting
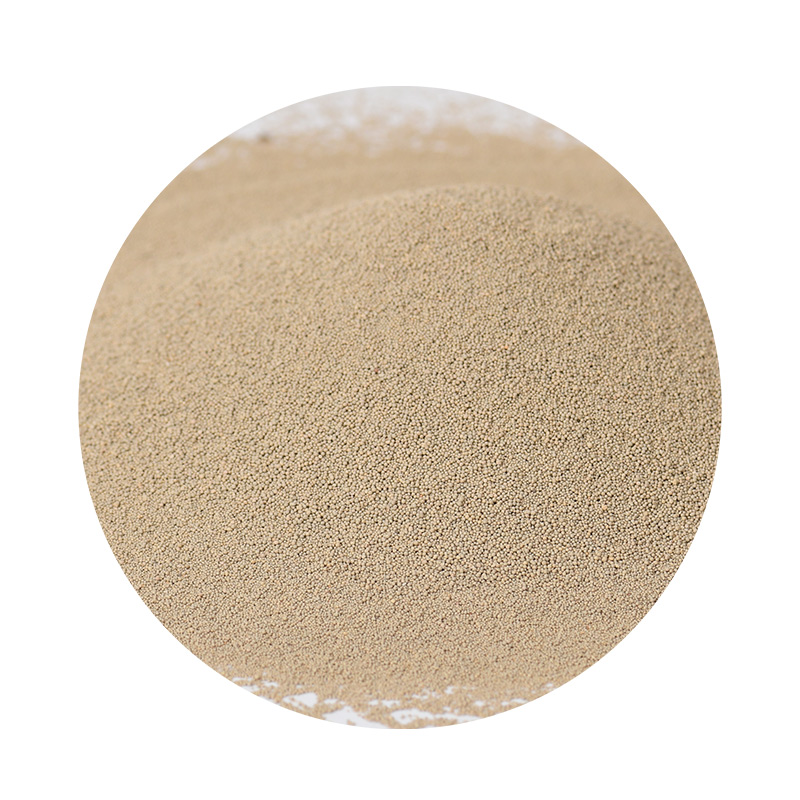
4. Making the Pouring System To facilitate the flow of molten metal, a pouring system is created. This includes a pouring basin, sprue, runners, and gates. These elements guide the molten metal into the mold cavity efficiently and help reduce turbulence, which can lead to defects in the finished part.
5. Melting and Pouring the Metal Once the mold is prepared, the metal is melted in a furnace. The temperature and type of metal used depend on the specifications of the cast. After the metal reaches the appropriate temperature, it is poured into the mold through the pouring system. Care is taken to avoid introducing impurities or inclusions during this stage.
6. Cooling and Solidification After pouring, the molten metal is allowed to cool and solidify within the mold. The cooling time varies based on the metal type, thickness of the casting, and mold material. After sufficient cooling, the mold is broken apart to retrieve the cast part.
7. Finishing The final step involves cleaning and finishing the cast part. This may include trimming excess metal, machining for precision, and surface treatments to achieve the desired finish.
In conclusion, sand casting is a versatile manufacturing process that consists of several critical steps. From pattern making to finishing, each stage is vital to producing high-quality cast components used in numerous applications across various industries. Its effectiveness and efficiency continue to make sand casting a popular choice in the field of manufacturing.
Post time:Σεπ . 04, 2024 11:45
Next:golden sand foundation