Sand Casting Techniques An Overview
Sand casting, one of the oldest and most versatile metal casting techniques, has been employed for centuries to create a wide range of metal parts and components. This process involves creating a mold from sand, which is then filled with molten metal to form the desired shape. The simplicity and adaptability of sand casting techniques make it a favored choice across various industries today, including automotive, aerospace, and artistic sculpture.
The Process of Sand Casting
The sand casting process can be broken down into several key steps
1. Pattern Making The first step in sand casting is creating a pattern. A pattern is a replica of the object to be cast, usually made from materials such as wood, metal, or plastic. Patterns are designed with allowances for shrinkage, machining, and other factors that might affect the final product.
2. Mold Preparation Once the pattern is ready, the next step is to prepare the mold. This is typically done using a mixture of sand and a binder. The sand, often silica, is compacted around the pattern. This compaction process can be executed manually or with the help of machinery. After the sand is shaped around the pattern, the mold is then removed carefully, leaving a cavity that mirrors the pattern's shape.
3. Core Making In cases where hollow spaces are required in the final casting, cores made of sand can be added to the mold. Cores are inserted into the mold prior to pouring molten metal. They are also made from sand but are reinforced with binders to hold their shape.
4. Melting and Pouring The metal to be cast is melted in a furnace and poured into the prepared mold. The temperature of the molten metal and the pouring technique are crucial for ensuring a successful casting. Different metals, such as aluminum, cast iron, or bronze, can be used depending on the application.
5. Cooling and Extraction Once the molten metal fills the mold, it is left to cool and solidify. Cooling time can vary based on the size and complexity of the part being cast. After cooling, the sand mold is broken away to reveal the cast part.
6. Finishing The final step includes cleaning, trimming, and machining the cast part to meet required specifications. This may involve removing sand residues, grinding, or applying surface finishes.
Advantages of Sand Casting
sand casting techniques
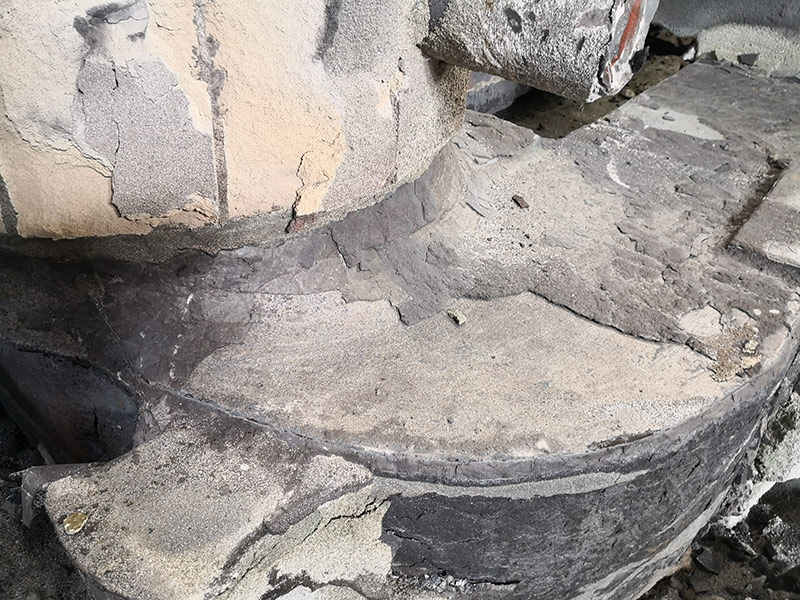
Sand casting offers several advantages that make it a popular choice for manufacturers
- Cost-Effectiveness The materials and equipment required for sand casting are relatively inexpensive compared to other casting methods
. This makes it accessible for both small and large-scale production runs.- Flexibility Sand casting can produce complex shapes and large parts. It accommodates a variety of metals, making it adaptable for various applications.
- Scalability This technique is scalable, allowing for both prototype designs and mass production without significant changes in setup.
Challenges in Sand Casting
Despite its benefits, sand casting also comes with challenges
- Surface Finish The surface finish of sand-cast products is typically not as smooth as that achieved through other casting methods, which may necessitate additional finishing work.
- Dimensional Accuracy While sand casting can produce complex shapes, it may not achieve the same level of dimensional accuracy as more advanced techniques, such as die casting.
- Environmental Concerns The use of sand and binders can raise environmental concerns, particularly related to dust and disposal.
Conclusion
Sand casting remains a reliable and effective method for producing metal components, thanks to its versatility and cost-effectiveness. While it faces competition from newer technologies, the adaptability and widespread availability of sand casting techniques ensure its relevance in modern manufacturing. As industries continue to seek ways to balance quality and cost, sand casting will likely maintain its position as a key player in the world of metalworking.
Post time:Νοέ . 05, 2024 03:20
Next:sand sintering